Economic growth in emerging economies is bringing prosperity, rising living standards, and overdue relief from poverty, but increased consumption typically increases resource use—especially the use of plastics—and waste production. As Exhibit 1 illustrates, the rapid surge in waste volumes since 2007 is straining waste-management systems in many developing countries, with negative effects in economic, health, and ecosystem terms. The Philippines is a case in point: it produces 2.7 million metric tons1 of plastic waste per year—600,000 metric tons in metro Manila alone.2 While the country has high waste-collection rates overall (84 percent nationwide), 17 percent of collected plastics is lost into the marine ecosystem after collection because of illegal dumping and poor landfill siting and operating practices. For uncollected plastics, the ocean-leakage rate is even higher, at 31 percent. The economic losses in tourism, fisheries, and healthcare are considerable. We estimate that each metric ton of uncollected mixed waste represents an average loss of approximately $375.3 As Inge Lardinois and Arnold van de Klundert wrote 20 years ago: “By almost any form of evaluation, solid waste management is a growing environmental and financial problem in developing countries. Despite significant efforts in the last decades, the majority of municipalities in the developing countries cannot manage the growing volume of waste produced in their cities.”4
While the importance and urgency of protecting the ecosystem is increasingly understood, the cost of the efforts required can be unaffordable for already overstretched municipal budgets. While statistics are still spotty, municipalities in developing countries might be spending 20 to 50 percent of their budgets on solid-waste management.5 The default solution has been to encourage private-sector waste operators to get involved through concessions or other forms of public–private partnerships. This can take away some of the financial pressure and inject much-needed expertise into local waste-management systems. Our work with municipal waste agencies around the world indicates it does not in itself guarantee any focus on value recovery, since this is usually not an explicit part of the mandate.
From waste streams to income streams
With the right approach, many waste streams can become income streams, yielding economic value with technology available today. Three examples from across the waste spectrum indicate the potential. For instance, pound for pound, there is more gold in electronic scrap than in gold ore.6 Collecting and selling used polyethylene terephthalate (PET) bottles can earn a waste picker a living ($3.50 a day).7 And every metric ton of used clothing collected could generate revenue of $1,975, if garments were sold at current secondary-market prices, comfortably outweighing the cost of $680 required to collect and sort each metric ton.8
Nevertheless, the value in many waste flows is not being captured today. Even the stable and relatively successful systems of PET-bottle and fiber recovery still extract only 40 to 60 percent of their potential total value.9 Why is this so? And how could the management of such relatively low-value products and materials be rendered profitable?
Our analysis suggests that the aggregate extractable value from consumer-waste flows is often higher than people think, and certainly higher than current recovery rates imply. The challenge that must be addressed to increase rates of recovery and valorization lies in the aggregation of volumes: scale and volume are needed to justify investment in technology and infrastructure that is capable of extracting more value. In other words, the critical challenges are the high degree of dispersion of many consumer materials and products, as well as the lack of an integrated infrastructure and a well-managed—reverse—supply chain operated at scale and based on sound management practices.
Keys to success for waste-management systems in emerging economies are the ability to aggregate waste flows into meaningful volumes around which businesses can be developed and the ability to organize the supply chain professionally at high levels of operational efficiency and environmental and societal effectiveness. Who or what mandates or operates such a system can vary, as long as the parties ramp up and yield results fast—staying on top, and preferably ahead, of the large and growing volumes of waste that are developing in emerging economies. Exhibit 2 illustrates the potential positive effect of aggregating flows and providing the necessary scale for high-performing value recovery:
- The PET-bottle-collection system that requires the lowest level of aggregation—collecting PET bottles as part of mixed waste—allows for energy recovery via incineration, yet its economic yield is so low as to require a so-called gate fee to cover operations. At the next level, recovering the bottles’ material value via a mixed-recyclables or mixed-plastics stream could yield approximately $150 to $300 per metric ton. The highest values, approximately $350 to $600 per metric ton, require the highest level of aggregation, in the form of a bottle-only collection system.
- Similarly, metals are commonly extracted from tires in small backyard operations where tires are burned in open fires—posing great risks to health and environment. Aggregating tires to feed them as fuel into industrial processes (rather than just backyard fires) could increase the value extracted from old tires tenfold. And when initiatives to organize the tire-waste flow cover not only collection but also the processes to recycle specific materials (not just using tires as industrial fuel), the value extraction from tires could see a further doubling.
- In the processing of electronic and electrical waste, too, shifting from backyard recycling—harmful to workers and environment—to processing in smelters with strong environmental controls could multiply the value that can be extracted. Currently, the required scale, and hence waste-volume aggregation, for smelters is significant, and only a few plants are available around the world to produce these high yields. Recently, technology companies have developed hydrometallurgical alternatives, which they claim generate higher yields and can be run profitably with smaller feedstock volumes. Once commercial installations are fully operational, they might therefore pose an interesting challenge to today’s large-scale paradigm for (precious) metals extraction. These smaller installations would, however, still require incoming materials that have been aggregated into “clean” unmixed waste flows.
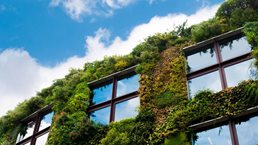
Would you like to learn more about our Sustainability & Resource Productivity Practice?
How aggregation can work—fast
Solutions for aggregating and organizing solid-waste flows—increasingly augmented by product-stewardship or extended-producer-responsibility programs—already exist at the municipal and regional levels, providing some instructive examples.
We will illustrate this with a few examples. Each example provides evidence that volume aggregation can be organized, creates significant economic value, and changes the complete material supply chain. Take organic waste. It typically makes up around 30 percent of household waste in developed countries, and up to 65 percent in developing ones.10 It is the biggest source of odors and pests in places where collection services are inadequate, causes groundwater contamination where disposal methods are substandard, and emits powerful greenhouse gases that are often not prevented from entering the atmosphere. Moreover, such “wet” organic materials contaminate other materials, dramatically reducing their recycling value. A growing number of cities in Europe and North America, however, have set up successful programs to divert organics away from conventional landfills or incinerators; in in the Flemish region of Belgium, for example, diversion volumes for organic household waste via municipal channels grew from 0 to over 350,000 metric tons over a ten-year period, despite initial public resistance and numerous challenges in producing marketable outputs such as certified compost.11
Cities are continuously tweaking programs to fit local needs. For example, Toronto decided to increase convenience for its citizens in order to raise participation and diversion rates, even though this means their processing facilities now need to remove plastic bags and the plastic parts of diapers.12 The city of Portland, Oregon, adjusted its program in the other direction, banning all nonfood items, even compostable ones, from its organics flow—in order to produce better-quality composts. Both programs have met their different, self-defined goals for diverting organic waste.
Successful programs are not limited to developed countries. Santa Cruz, the second-largest island of the Galapagos Archipelago, has separately collected organic waste since 2006, and the program covers nearly 100 percent of households.13 In Telangana, India, a group of young entrepreneurs recognized both the urgent and growing need for waste-collection services in tier-three cities and the need to restore the surrounding farmland, where soil had been losing its fertility. These entrepreneurs founded Waste Ventures India (WVI), which turns municipalities’ organic waste into compost that fetches sufficiently high prices from farmers to cover about 45 percent of project operations, even at low municipal separation rates of approximately 8 percent of the waste stream. This allows WVI to charge competitive rates for its collection activities.
In a different part of the world, the Recycling and Economic Development Initiative of South Africa (REDISA) was set up in late 2012 to tackle scrap-tire collection and distribution to processors for the whole territory of South Africa. With a double mandate to reduce the environmental and health threats from poor tire-management practices and improve the lives of underprivileged South Africans, REDISA quickly put in place a management structure and collection network to address the most pressing problem: discarded tires were burned locally in open fires, with no protection whatsoever for public health or the environment. As a result of REDISA’s concerted effort to put out tire fires, collected volumes increased from 4 to 70 percent of end-of-life volumes from 2013 to 2015 (Exhibit 3). In the meantime, the team started to develop treatment capacity. It is already moving all collected tires into environmentally preferable treatment routes and is ramping up to have all recoverable scrap tires collected and treated within the country by 2016. By 2020, the initiative plans to have the majority of scrap tires going into a high-value material-recovery process.14
Economic and environmental benefits need not be mutually exclusive (Exhibit 4). The collection and sorting of recyclables, such as tires, can provide livelihoods for many individuals outside of larger companies—and often outside of the formal labor market altogether. Moreover, processing and recycling can give birth to a number of small to midsize companies. For every 1,000 metric tons of tires REDISA collects, up to ten full-time jobs are created, often in parts of the country where customary employment schemes have less reach, thus offering livelihoods to people who may otherwise have limited access to the job market. All in all, the REDISA system is on track to be operating cost neutrally from a societal perspective by 2017, just five years from its inception. By 2020, it is expected to deliver an aggregated economic benefit of approximately $6 million to South Africa. In addition, if REDISA reaches its planned objectives for collection and treatment, we estimate that, by 2020, the system will also generate an annual environmental benefit of $22 million, and the employment it creates will have grown further, to the equivalent of approximately 1,900 full-time jobs.15
Success factors: Today and tomorrow
From strong roots in Europe, product-stewardship programs are growing around the world, including in developing and emerging markets; for instance, there are programs for electronic waste in China, plastic packaging in Tunisia, and various material flows in Brazil. Some of these schemes are industry owned, and some are run by third-party organizations or government agencies. Regardless of who is in charge of a waste-management scheme, the most successful programs share a number of common elements, which need to be in place to deliver positive outcomes in a cost-efficient way. Analysis suggests there are at least three factors that really make a difference.
Cash-backed reliability
A thriving resource-recovery system requires a strong balance sheet of some sort. Recyclers or other downstream users of the waste must be comfortable to invest—sometimes significant amounts—in commodity industries with razor-thin margins. This is essential to be able to build capacity that absorbs most if not all collected materials. They need access to feedstock in sufficient volumes and with consistent quality. Processors need reliable off-take agreements with assurances on volume and consistency in order to plan, invest, and create commercially and operationally viable product flows.
The South African tire aggregator, for example, actively supports the development of processing capacity by researching new processing options and paying out gate fees in the start-up phase of new facilities. It also reduces the access barrier by entering into contractual agreements with the various tire processors and guaranteeing them a minimum volume of feedstock.16
For such feedstock guarantees to be credible, processors and other system partners need to be able to hold the management of a waste-management scheme accountable. This means any private-system operator needs to have a strong, externally audited balance sheet and cash-flow position. If the system operator is an industry itself, the companies behind it will be held liable; with a government-run scheme, it is the public sector that assumes the risk. In the model pioneered by WVI, the company worked with the local government to craft a more effective contractual arrangement where the authorities provide the use of capital expenditures in lieu of monetary payment.17 The land, a shed, and equipment are made available by the municipality and operated by WVI, so buyers of WVI’s products and services have visibility into operations and can be confident about the system’s staying power.
Transparency
When a private company takes on the system-management mandate, maintaining full transparency on material flows is critical to operate successfully. Transparency builds credibility with system suppliers and partners and facilitates government monitoring of system outcomes (ecosystem and public health, as well as social impact). Transparency also enables producers that pay into the system to assess efficiency and continuous-improvement efforts. Internally, such visibility allows the company to make adjustments to chosen collection and treatment methods, systems management, or the approach to regulatory support.
WVI tracks both Progress Out of Poverty indicators and job creation, including compensation levels. WVI also has built out a full-fledged IT infrastructure to track its core impact and business metrics. The WVI IT system has a fully built-out front end that allows it to move from an operating model based on formal employees to one that allows workers to remain “their own boss” and is therefore more suited to pull in large numbers of informal workers. The back end of the system supports managerial decisions and aggregates reporting into an easy-to-use dashboard for key performance indicators (KPIs).
REDISA maintains a detailed management dashboard, reports to the South African authorities on a monthly basis, and is audited on an annual basis. Its mandate is assigned on an initial five-year basis, renewable after review by the government, ensuring continued high performance against its government-mandated KPIs. Its advanced IT systems help recognize pockets of value (and the absence of such value) and tailor approaches, support swift management decisions, and facilitate reporting and accounting. REDISA has also built out tracking facilities across the country, allowing for better follow-up on problems, swifter payouts, and focused capacity building.
Strong management bench
Much of the waste-management sector has traditionally been dominated by the informal economy; it was prone to opportunistic practices and fragmentation, too often rife with corruption, and avoided by top talent. Given the economic and social importance of waste recovery in fast-growing economies, this setup will need to be replaced by a more industrial approach, stronger performance management, and better management talent. The most successful systems have shifted the sector toward a more industrial culture, recruited competitively for people with in-demand skills, and built high-performing leadership teams—all on a bedrock of strong analytics to inform strategic and operational decisions.
REDISA’s top team has a combined 140 years of management experience in business, backed by strong academic credentials.18 WVI has complemented its leadership’s local anchoring with analytical and innovation talent from leading consultancies and top-ranked universities around the world. It has also taken a strong analytical approach to workforce retention and performance—studying in detail the needs and motivations of informal workers in the waste-management space, and adjusting compensation models accordingly.19
Planning ahead to enhance value creation
Many waste-management solutions are path dependent. This means actions that address the problem now can lock out superior solutions (such as new materials or waste-avoidance practices) later because they shape materials markets for decades. Europe’s dense incineration infrastructure has often been cited as a hindrance to the market environment for increased recycling. It is feasible, however, to tackle the immediate needs that come with the growing volumes of waste, derive value today, and set up the system to create further value in the future. To do so requires a system setup that respects the principles of the circular economy, which strives to create more economic, environmental, and social value by moving from landfill to recycling or—better still—to reuse, by extending product lifetime or by moving toward a new generation of regenerative materials.
WVI is fully “upwardly compatible” with more circular solutions and takes a technology-agnostic approach to organic-waste processing, seamlessly connecting collection systems, government cooperation, and processing. It started out with composting, which fulfills the immediate demands of stabilizing the material, reducing its volume, and reducing harmful greenhouse gases. Moreover, it yields sellable products in the form of compost and composting liquor. But WVI is also considering anaerobic digestion or the production of refuse-derived fuel in its new city contracts—which both offer more flexibility in the quality of the waste intake.
In South Africa, REDISA is already developing infrastructure for commercially and environmentally preferable treatments. In addition, it has the potential to redirect tires to retreaders in even higher volumes by making greater use of its own logistics network and IT infrastructure. The system is also able to support product tagging to further enhance the performance of this and other recovery loops, for example, by providing an incentive for improved tire design. Producers who make tagged tires with less toxic materials can be rewarded with a more attractive tariff. Furthermore, REDISA is directly stimulating research into such designs.
In Europe, national activities to address the collection and processing requirements of the EU’s Directive on Waste Electrical and Electronic Equipment have focused on safely disposing of and recycling materials, most frequently through shared compliance mechanisms. These have proved effective in avoiding the worst risks to environmental and public health. They could also include or be complemented with incentives to move beyond materials recycling—for example, to design for disassembly or to create refurbishing programs. The Netherlands, for instance, has recently introduced a new mechanism called the Register. Here, manufacturers can officially register any volumes that they themselves or their service providers have taken back for the purposes of value recovery. Allowing for such volumes to be tracked and counted against manufacturers’ compliance obligations could stimulate further initiatives by manufacturers to recover higher value.
High-growth countries are facing a paradigm shift because the volume of waste grows faster than they can deal with it. Public–private partnerships in themselves cannot guarantee success: cleaning up alone will not do the job. More systemic solutions—from waste avoidance to reuse—are needed. In emerging economies, we are also starting to see a new role for industries, as they are pushed to take ownership of their end-of-life waste streams.
In such an environment, a crucial new capability is knowing how to set up industrial operating platforms for waste aggregation. These platforms must be cost effective from the start. This is achieved in two ways: first, by aggregating waste flows into streams large enough for business development and, second, by managing the supply chain—with its upstream and downstream contracts—professionally, with a strong IT backbone, and at a high level of operating efficiency and transparency. The assurances such a platform offers could build trust and stimulate investment in a business that traditionally has suffered from a lot of volatility.
The chance to tap into new sources of value through better waste management and win the “race against waste” is cause for optimism. There are few areas where entrepreneurial success comes with more benefits to the economy and society at large.