The world has changed for manufacturers. Preparation for uncertainty has become an industry norm, with executives expecting the impact of disruption—whether from geopolitical tensions, climate change effects, technology breakthroughs, or supply chain vulnerabilities—to increase by 15 to 25 percent over the next five years.1
At the same time, advanced manufacturing is now flourishing in markets where stagnation had seemed intractable. Growth in the US manufacturing sector, for example, had languished at 1.4 percent over the past two decades. More recently, AI, digital technologies, sustainable features, and higher skill have reinvigorated the market: over the past five years, US industrials companies have generated total shareholder returns about 400 basis points higher than in the previous 15 years.
The accelerating pace of the Fourth Industrial Revolution (4IR) can help enable this type of next-level performance while also increasing workforce inclusivity and sustainability. The Global Lighthouse Network,2 now in its fifth year, provides an expanding pool of examples. In effect, each Lighthouse cohort provides a three- to five-year look ahead at the future of operations across the value chain.
The most recent cohort affirms a 4IR inflection point, marked by two factors. First, machine intelligence technologies—AI that, rather than seeking to simulate human intelligence, empowers machines with the specialized intelligence needed to perform complex tasks in the cyber-physical world of production—are reaching unprecedented levels of maturity. Second, leading companies are redefining the concept of a pilot as they scale impact by using entire factories, rather than individual use cases, as pilots.
This series of three articles will explore: (1) the current status of global manufacturing, with a particular focus on (2) what AI looks like among today’s leading manufacturers, and (3) the capabilities they have built to deploy it with both speed and scale. In this first installment, we’ll explore how the maturity of AI marks a 4IR inflection point; examine how leading manufacturers are redefining the leading edge of manufacturing with this technology; and finally, consider three types of strategic responses—to innovate, to accelerate, or to follow fast—that manufacturers will need to consider as industry becomes more competitive. The second and third articles, respectively, will focus on the at-scale impact of AI within the manufacturing sector and the essential capabilities that drive AI adoption.
The S-curves of industrial revolution
Global industry transformation has never been instantaneous. Each “revolutionary shift” saw a lag period between the introduction of the enabling foundation and widespread adoption. Consider the steam engine. The Roman architect Vitruvius made mention of a rudimentary steam-powered device as early as 15 BC. Why, therefore, did widespread adoption take more than 1,800 years? The answer is simple: steam was neither practical nor cost-effective until breakthrough engine technologies—along with the infrastructure of coal supply chains—made it so. This tipping point essentially eliminated the learning curve, allowing the “doing curve” to steepen. The front-runners had done the learning. It wasn’t until the late 18th century that, in the space of just 20 years, steam engine adoption in industry increased from practically nothing to nearly 80 percent.
What steam was to the First Industrial Revolution is what AI will be to the fourth. And much as coal supply chains and factory infrastructure were the tipping point that enabled steam power to race up the adoption curve, data collection and data infrastructure are doing the same in the fourth. Already, some of the world’s leading factories generate multiple petabytes of data a week. If all ten million factories in the world operated at this level, they would double all human information in less than a month (see sidebar “The evolution of the revolutions”).
The adoption S-curve
We can see a pattern as we look back upon each industrial revolution: it has always taken the shape of an “S-curve.” The first phase is a learning curve, which tends to be long, and is marked by trial and error as early front-runners figure out how to make things work. It then moves on to the next phase, the “doing” part of the curve. This is when the foundational technology has been established, and organizations work to deploy it across their production networks. Finally, we see an optimization curve, which is when industries align around what works best. New standards and protocols become ingrained, and costs start to stabilize (Exhibit 1). One need only look back at a now-ubiquitous technology, such as the smartphone, to recognize this three-phase S-curve in play.
One of the most significant differentiators for members of the Global Lighthouse Network—the 153 factories at the forefront of the Fourth Industrial Revolution—is that we believe them to be three to five years further along 4IR’s adoption curve than are other manufacturers. Today, they aren’t focused on piloting use cases. Instead, they’ve built the capabilities to get new use cases right quickly and without trials. For companies with multiple Lighthouses, entire factories serve as pilots for networkwide deployment at scale. Leaders are now capturing the value of 4IR technologies ten and 50 factories at a time, where others are still working to find value within a single factory.
Lighthouses are accelerating, and so too is the maturity chasm they have put between themselves and everyone else. This chasm is evident in the wake of recent disruption and volatility. Consider that 85 percent of Lighthouses saw revenue reductions of less than 10 percent during the height of the COVID-19 pandemic; this was true for only 14 percent of other manufacturers. Lighthouses could react quicker: although they faced the same supply chain risks, 65 percent of Lighthouses were already dual-sourcing and increasing inventory by 2022, compared with only 24 percent of other companies.
AI is defining the Fourth Industrial Revolution
The true power of AI for the Fourth Industrial Revolution lies with the fact that it sits at the top of a “pyramid” of 4IR technologies—it is playing the role of conductor for 4IR technologies, which together perform a symphony of impact (Exhibit 2).
Consider the example of a rapid changeover at a production site (Exhibit 3). This requires flexible robotics to handle different products, automated guided vehicles to move materials and parts, 3-D printing to customize line fixtures, and wearable technology to keep managers and technicians informed with real-time data. What orchestrates this complex interplay of elements, each of which is individually complex? The answer: AI.
But AI needs terabytes of data generated by and collected from a broad range of sources: enterprise systems, machine sensors, connectivity infrastructure, and human workers. That’s why the most advanced front-runners are ahead. They had the foresight to make investments and take on risks involved in building the data foundations that are needed to power AI technologies and unlock their potential impact (see sidebar “Understanding AI: How it actually works).
With AI, machine intelligence can orchestrate highly complex technologies for rapid solutions.
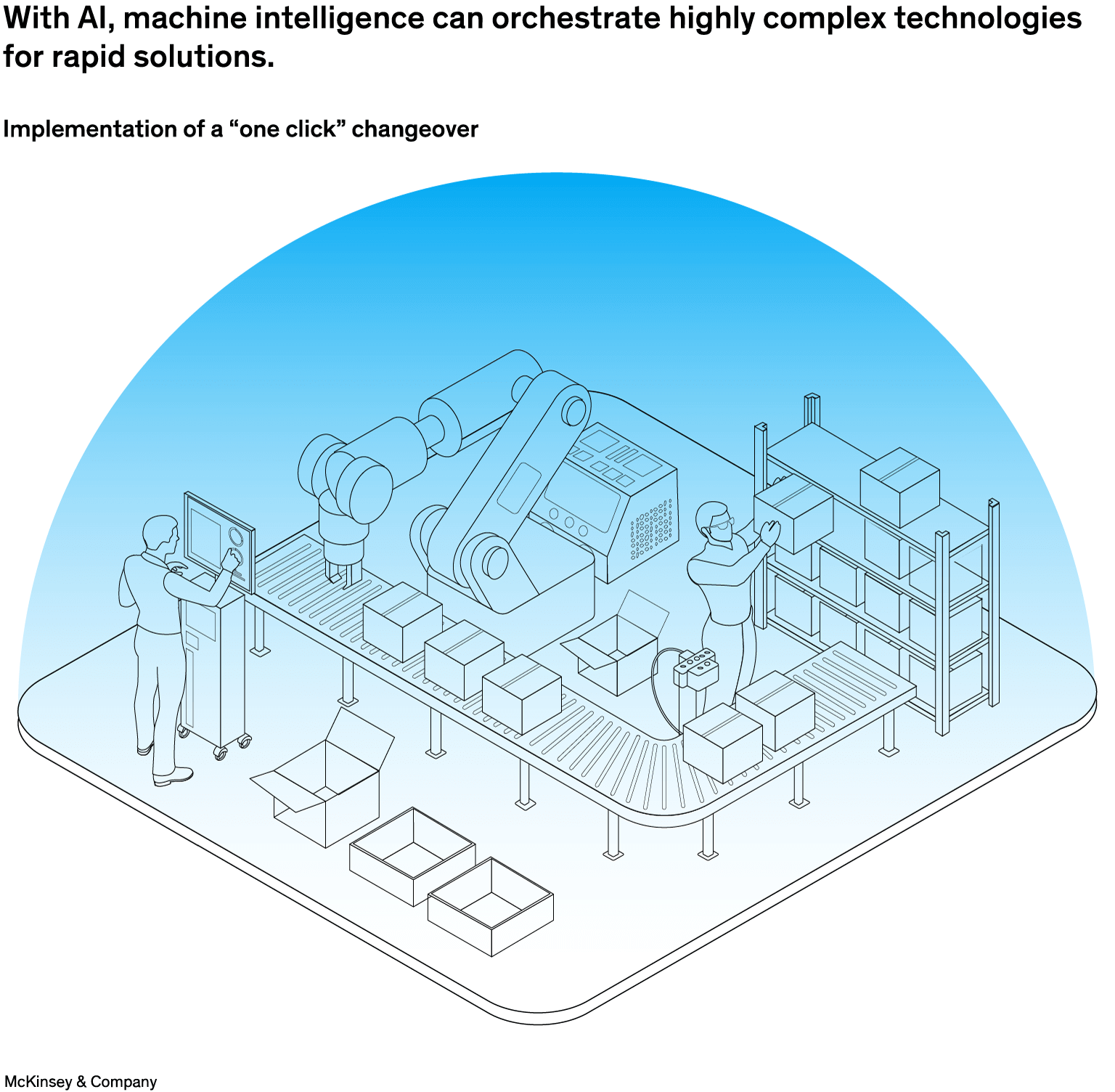
Capabilities to tackle the scaling slump
AI is defining the Fourth Industrial Revolution, and Lighthouses are showing us that AI has myriad new use cases and possibilities for unimaginable performance improvements.
Use cases inform capabilities, and capabilities lead scale. Back in 2018, cutting-edge use cases looked like localized applications of advanced analytics and autonomous vehicles, or radically transparent data connectivity and visualization dashboards, and similar digital-lean solutions. These use cases took much longer for Lighthouses to implement than they do today; where most Lighthouses say it took ten to 20 months average time to implement their first five use cases, 75 percent say they can now do it in less than six months. Even more impressively, 30 percent claim they can do it in less than three months.
This is because for early use cases, factories first had to rewire their data collection and connectivity layers, design tech stacks that added to or upgraded legacy infrastructure, train their people on how to use advanced new tools, and reorganize themselves to deploy digital solutions quickly and with strong feedback. Once built, these capabilities became the foundation for the rapid deployment of new use cases. One Lighthouse, for example, says it was able to implement a gen-AI-based technician adviser in just days and weeks, not months and years.
Ongoing challenges see Lighthouses move from pilot purgatory to scaling slump. At the factory level, capabilities are a solved problem, at least for Lighthouses. Now, many Lighthouses are in the valley that follows the “false peak” of the learning curve, stalling on impact while they rewire themselves for network scale. This isn’t easy. Taking a technology that works in one place and extending it across an entire production network introduces massive new challenges: data, technology, talent, and organizational challenges that exist at a single site are not the same at the macro level—and neither are the solutions. For that gen-AI-based technician adviser to see the light of two dozen factories, those factories must first be ready to receive it.
Those that overcome the scaling slump can define entire industries. This is because they set standards. The adoption of steam engines in manufacturing is an early example. For a more modern-day example: consider Toyota, which managed to scale its production system at the macro level. Shortly after, lean manufacturing and Six Sigma became standard fare for companies all across the world—with the accompanying emergence of new standards, protocols, certifications, and regulatory measures. The innovations became institutionalized; Toyota defined the new normal, which is reflective of the optimization phase of the adoption curve. In other sectors outside of manufacturing, such as tech and banking, AI is already at this stage, so the conversations are focused on standards and regulatory compliance. These sectors can deploy AI at scale, fast—for example, Microsoft was able to integrate ChatGPT into Bing mere months after its launch.
And like both the steam engine in the First Industrial Revolution and AI technologies in tech and banking, we expect 4IR’s breakthrough technologies to catapult from single digit to widespread adoption within the decade. Lighthouses are leading the way. Already, AI-based use cases make up over 60 percent of the use cases presented by new Lighthouse applicants, up from just 11 percent in 2019.
Lighthouses are accelerating the leading edge: How will you respond?
Although it may be some time before gen AI and other highly advanced emerging technologies see networkwide adoption in manufacturing, Lighthouses are already achieving factory-scale adoption. All of the newly recognized Lighthouses have at least one gen AI pilot in process, and several have implemented, tested, and iterated gen AI use cases for impact in as little as days or weeks—not months or years. Again, they’re able to do so because they’ve already built the necessary enablers: solid data and tech infrastructure, a strong talent base, and agile operating models.
They’ve coupled these enablers with clear business strategy and effective change management. Notably, Lighthouses avoid the trap of investing in technology for its own sake, instead ensuring that every use case presents clear business value. Paradoxically, they’ve surged ahead by taking a patient, measured approach—typically between ten and 20 months for use case implementation, with an ROI period of approximately two and a half years. This takes patience and a steady hand, but the returns are worth it. Lighthouses’ 4IR use cases have averaged between two and three times ROI within three years and between four and five times ROI within five years.
As Lighthouses continue to push through the scaling slump, their ability to implement use cases more rapidly is improving. The most recent three Lighthouse cohorts implemented use cases 26 percent faster than the first three did, and 75 percent of Lighthouses report that they’re able to deploy a new advanced use case in under six months; 30 percent can do so in less than three months. Technology adoption is self-perpetuating. The more companies progress, the faster they progress. This also provides them with added agility and ability to respond to disruption—a major factor in the expanding performance gap between leaders and laggards.3
This moment compels a decision: Lead, innovate, or follow fast
What does an inflection point mean for manufacturers? It compels a crucial decision about how to respond. The global front-runners—Lighthouses—along with an increasing number of other leading organizations are pushing through the scaling slump, achieving network-level impact. What will other companies do?
There is more than one intelligent response. An organization might choose to be a network-level digital innovator. This is an industry pathfinder that takes a risk on—and proves, at the factory level—the next big thing. This is the path that many Lighthouses have taken. But there’s also a smart path forward for the industry accelerator. This company focuses on network-level impact, changing the landscape for an entire industry. Finally, there’s great opportunity that lies with being a fast follower. This company embraces the playbook already written by the innovators and accelerators, capturing value while skipping the costs and tribulations of the learning curve altogether (Exhibit 4).
Each of these three responses can comprise an intelligent strategic response. This exciting juncture of the Fourth Industrial Revolution provides a momentous opportunity for manufacturers to choose a course of action. There’s freedom in that, and it means that companies can take the approach that best suits their circumstances and business needs. But make no mistake: this inflection point also means that inaction is a sure-fire path to failure.
The next two articles in this series will explore what advanced AI and gen AI look like among today’s leading manufacturers, and the capabilities that are powering Lighthouses to scale advanced technologies across full production networks.
This article originally appeared in the Global Lighthouse Network whitepaper Adopting AI at speed and scale, published on December 14, 2023.
The Global Lighthouse Network is a World Economic Forum initiative. The initiative was co-founded with McKinsey & Company and is counselled by an advisory board of industry leaders who are working together to shape the future of global manufacturing. The Advisory Board includes Foxconn Industrial Internet, Johnson & Johnson, Koç Holdings, McKinsey & Company, Schneider Electric and Siemens. Sites and value chains that join the network are designated by an independent panel of experts.