In the past five years, a select group of companies have started pulling ahead in their efforts to implement Industry 4.0 across their manufacturing networks. Leading manufacturers are now realizing significant value from data and analytics, AI, and machine learning (ML). However, a large majority remain stuck in pilot purgatory, struggling to capture the full potential of their transformation efforts or deliver a satisfactory return on investment.
While digital transformations are notoriously difficult to scale up across networks of factories, the pressure to succeed is intense. Companies at the front of the pack are capturing benefits across the entire manufacturing value chain—increasing production capacity and reducing material losses, improving customer service and delivery lead times, achieving higher employee satisfaction, and reducing their environmental impact. Scaled across networks, these gains can fundamentally transform a company’s competitive position.
With so much at stake, manufacturers are putting significant time and money behind their digital transformations. These investments are paying off for some, but most remain unable to scale successful pilot programs or fully leverage new tools and technology to see meaningful returns.
This article explores some of the common pitfalls associated with digital transformations and how a more strategic and value-driven approach could help manufacturers in the race to get ahead.
Delivering value across every area of the factory
The digitally enabled factory of today looks very different from the leading factory of ten years ago. Advances in data and analytics, AI, and ML—and the array of technology vendors in the market—mean manufacturers can choose from hundreds of potential solutions and tech applications to improve their ways of working.
Implemented successfully, these solutions deliver irresistible returns. Across a wide range of sectors, it is not uncommon to see 30 to 50 percent reductions in machine downtime, 10 to 30 percent increases in throughput, 15 to 30 percent improvements in labor productivity, and 85 percent more accurate forecasting (Exhibit 1).
Digital transformations are revolutionizing all aspects of manufacturing, touching not just processes and productivity but also people. The right applications of technology can lead to more empowered decision making; new opportunities for upskilling, reskilling, and cross-functional collaboration; better talent attraction and retention; and improved workplace safety and employee satisfaction.
Customers see the impacts through reduced manufacturing lead times, right-first-time launch management, and improved customer service and complexity management. And, of course, there are the win–win advantages associated with reduced environmental impact, made possible through lower emissions and reduced waste and more efficient energy, water, and raw-material consumption.
These productivity, process, and people improvements are not easy to accomplish—especially across a network of individual manufacturing sites, each with its own site leadership, IT infrastructure, and workplace culture. It is not uncommon to hear of companies achieving impressive results through pilot programs at one factory site only to find themselves unable to replicate these local wins across their network.
This was the situation at a global industrial company. Facing a considerable ramp-up in demand—volume more than doubled over just three years, which translated to producing more than 50 million additional parts—the business embarked on an ambitious digital transformation at one factory. The goal was to increase overall equipment effectiveness (OEE) by ten percentage points and reduce product unit costs by more than 30 percent.
The project delivered: the factory was admitted to the Global Lighthouse Network, a World Economic Forum initiative, in collaboration with McKinsey, that recognizes leadership in the Fourth Industrial Revolution. The site started welcoming external visitors to showcase its transformation. But despite this achievement, it was unclear to the company how to take this local success story and replicate it across other sites.
Would you like to learn more about our Operations Practice?
The common pitfalls of scaling digital transformations
There are five common reasons why manufacturers are not succeeding on this journey.
Siloed implementation. By pursuing digital transformations as a theoretical exercise, many companies unwittingly set up independent delivery teams that are decoupled from business leaders, site operations, manufacturing excellence, and central IT. Others focus too much on replicating a single site experience, failing to appreciate wider network complexities.
Failure to adapt. By deploying a one-size-fits-all approach, manufacturers miss the opportunity to build in the customization and adaptation needed to leverage the unique circumstances, culture, and values of separate factory sites.
Analysis paralysis. Performing a full and deep up-front analysis of an entire network can leave a manufacturer out of steam before a transformation can get off the ground. Instead, robust, accurate-enough insights can be gleaned from a well-developed extrapolation methodology.
Technology-driven rather than value-driven. A technology-first rollout means that solutions are deployed without a clear link to real value opportunities, business challenges, or capability requirements. The result: undermining crucial buy-in from the people charged with making deployment work.
Letting the ‘perfect’ defeat the good. By waiting until a fully fledged, ideal-state data and IT/OT (information technology/operational technology) architecture is defined and implemented before rolling out Industry 4.0 solutions, manufacturers lose out on the shorter time-to-impact made possible through a proven and pragmatic minimal viable architecture.
Three company archetypes join the race
Manufacturers playing catch-up to the leading companies generally fall into one of three company archetypes.
The cautious starters. These companies are investigating how to begin their digital-transformation journeys. They need help to identify the full value that Industry 4.0 can bring to their business and to develop a network-wide strategy and deployment road map.
The frustrated experimenters. These companies have started experimenting through pilot programs with some successes. However, they find themselves deploying technologies without a clear understanding of how to achieve financial ROI.
The ready-to-scalers. These companies are deploying solutions and technologies but remain unable to maximize the returns or scale at pace across their networks. They need to recalibrate by focusing on how to capture the full benefits of Industry 4.0 or how to accelerate rollout to respond to shifts in business and customer needs.
Slowing down to go fast
No matter where a company falls on the spectrum of archetypes, there is great value in slowing down and regrouping around a new, more targeted strategy aimed at maximizing the value of a digital transformation.
An important lesson from the few organizations that have succeeded in scaling digital innovations is how they started their impact journey. Before jumping headfirst into procurement and deployment, the leading companies spend time identifying the full potential of Industry 4.0—pinpointing high-leverage areas across the manufacturing value chain—and architecting a laser-focused digital-manufacturing strategy and deployment road map.
The first phase of this approach includes a network scan to identify the value at stake and a priority list of technology use cases, taking into consideration data, IT/OT, and organizational maturity. An accompanying road map can then build on this groundwork, defining the deployment strategy and targeted sites for initial rollout, followed by a network-wide rollout plan to reach scale.
Taking the time up front to perform a network scan to find opportunities for big wins and quick wins can create significant momentum for a digital transformation. As manufacturing sites begin to capture financial and operational value—not to mention the benefits associated with improved organizational capabilities, workforce satisfaction, customer service performance, and environmental impact—these returns can create a virtuous feedback loop where programs become self-funding and initiatives translate more quickly into competitive advantage.
Scaling success
It is this methodology that underpinned the approach taken by the industrial company mentioned earlier. Following its lighthouse success, the business needed to understand how and where to invest to maximize returns across its network. By performing a network scan on a subset of its manufacturing value streams across more than a dozen sites, it identified five sites that together represented around 80 percent of the value at stake. Further, it found that ten out of the 17 identified use cases for technology accounted for 75 percent of the potential impact.
With a sound value-capture deployment strategy in place, and after structurally investing in the required capabilities, the company was able to replicate the network scan approach across the rest of its manufacturing network and scale to other business areas. A senior stakeholder in the company said: “We essentially wrote the playbook for how to scale this into our other sites and are making great progress in these places—not only across our downstream production network but also within our upstream production sites, leveraging digital to reduce human interventions and increase compliance.”
In another example, a global consumer company had been piloting digital innovations in a number of business units for some time, but with few ideas achieving much impact beyond the individual line or site. Company leaders recognized the need to clarify which digital solutions could contribute to overall business needs and priorities, and where to focus transformation efforts to implement solutions at scale.
Following two months of up-front analysis focused on eight prioritized sites from a network of more than 40 factories in Europe and North America, the company realized that about 20 sites accounted for 80 percent of the total savings potential. It also identified a prioritized portfolio of digital solutions, with about two dozen use cases having relevance across the entire network, and a dozen identified as “no regrets” priorities.
Crucially, the process has enabled the company to understand the level of readiness of its data and technology infrastructure and the investment required in technical, managerial, and transformational capabilities. The company came out of the two months with an aligned and value-oriented road map for rolling out a digital transformation across its network. The plan integrated both digital and traditional lean or Six Sigma improvements, accounted for resources and technology requirements, and reflected a clear strategy for building capabilities at scale. The company went on to deploy at scale across multiple sites, pursuing more than $100 million of identified savings.
The seven golden principles for getting the best out of Industry 4.0
Whether manufacturers are starting out on their digital-transformation journeys—or recalibrating their approach after false starts or failed attempts—the approaches adopted by leading companies point to seven golden principles for scaling a successful digital transformation.
Communicate well and often. Establish an effective engagement plan and regular communication with critical senior stakeholders, site leaders, and a cross-functional core team.
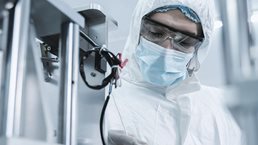
Lighthouses reveal a playbook for responsible industry transformation
Be specific. Focus on real business needs and current performance challenges, and follow a “strengths upward” approach, building on solutions that have already worked well at individual sites and can be rolled out pragmatically across the network.
Segment, select, and syndicate. Segment the manufacturing network and select representative sites for an up-front network scan. Syndicate the extrapolation methodology up front to indicate how focused insights will be scaled to derive a networkwide analysis.
Formalize the value at stake. In each assessed site, describe the actual value at stake by linking the most applicable Industry 4.0 solutions or use cases with current digital readiness, data availability, and IT/OT architecture.
Develop a three- to five-year vision for the network. Describe the total value at stake from prioritized bundles of use cases to align business leaders on the ambition, and form a compelling change story for the broader organization. An engaging visual representation of the key solutions can help to engage the broader organization with the vision (Exhibit 2).
Design a digital-manufacturing road map. Develop a prioritized rollout plan with a clear scaling strategy and articulation of the value to capture over time, integrating enablement of data and IT/OT architecture as well as resourcing requirements, capabilities, and change management.
Syndicate the vision and secure leadership buy-in. Circulate the business case and requirements with key stakeholders, aiming for a clear mandate from top leadership and close engagement on target setting and execution from site leaders.
Whether stuck in pilot purgatory or under mounting pressure to demonstrate returns, companies can become dispirited and discouraged. However, by taking just one or two months to slow down and develop a robust manufacturing strategy and deployment road map, companies can accelerate their Industry 4.0 transformations and chart a clear journey forward for the next few years.