As the COVID-19 pandemic brought with it unparalleled disruptions to global supply chains across nearly every industry, supply-chain resilience has catapulted to the top of the C-suite agenda. CEOs representing some of the most innovative organizations around the world joined a discussion on navigating the most significant supply-chain disruption in scope and size in recent memory. Hundreds of participants across dozens of industries tuned in to hear from the CEOs of Tata Sons, GlobalFoundries, and Stanley Black & Decker, together with Susan Lund of the McKinsey Global Institute, about the recipe to build resilient operations and why digital capabilities are key to successful operations in the next normal. McKinsey senior partner Asutosh Padhi moderated the discussion, which revealed several important insights.
Supply-chain resilience emerges as business critical
For the past 20 years or longer, many companies have optimized supply chains primarily to achieve efficiency, using year-over-year cost reduction as the metric for what success looks like. However, the events of the past several years, ranging from the COVID-19 pandemic to trade tensions and climate-related disruptions, have changed the risk profile of global supply chains.
It’s estimated that significant disruptions to production now occur every 3.7 years, on average, adding new urgency to supply-chain-resilience questions for CEOs, boards of directors, and investors—not just operations leaders. Additionally, recent research from the McKinsey Global Institute found that as much as 45 percent of one year’s earnings could be lost each decade because of disruptions. Some companies are demonstrating that flexible and resilient supply chains can deliver more than productivity improvement: they can generate new value and profitable growth in the long term.
“We have gone through a series of disruptions related to trade, in particular, and also rampant inflation and massive shifts in foreign exchange that were changing the cost competitiveness of our supply chain,” said Jim Loree, the CEO of Stanley Black & Decker. “We put a performance-resiliency initiative in place, which focuses today’s technologies on value pools in the company to extract the maximum amount of margin impact. That initiative looks like it will produce about half a billion dollars of value.”
Would you like to learn more about our Operations Practice?
Historically, many industrial companies have undervalued what’s at stake should a supply-chain shock occur. The COVID-19 crisis exposed cracks in the rigid execution of a just-in-time operating model. At the same time, it opened new opportunities to drive innovation.
The buzzword in the past was “efficiency,” and supply chains were built to be just in time, not just in case. It’s clear that we now live in a different environment, however, in which trade will become much more targeted. So companies around the world are thinking about resilience strategically. While we know how to measure efficiency, the critical questions going forward will be how we measure resilience.
Digitization is accelerating to reimagine operations
The acceleration of end-to-end digitization will be critical in resolving long-standing trade-offs between efficiency and resilience. When implemented at scale, digitization can help companies dramatically increase resilience without enduring unsustainable increases in costs. But while the supply chain has been one of the most-hyped use cases for artificial intelligence and machine learning, fewer than 25 percent of companies say their supply chains have digital capabilities today.
Digitization can enable operational leaders to access crucial data on supply and demand, and it can provide a lens into the product availability, inventory, and order status of a company’s suppliers. “Throughout the COVID-19 pandemic, our manufacturing facilities around the world were designated as an essential service and remained operational to continue manufacturing semiconductor technology that is vital to so many industries,” said Tom Caulfield, the CEO of GlobalFoundries. “Leveraging digital technologies and aligning our operational strategy to our corporate strategy for an optimized global footprint enabled us to navigate the crisis.”
For example, GlobalFoundries used virtual-reality glasses so that a skilled technician in Asia who couldn’t travel to the company’s facility in Europe could help an on-site technician service a tool remotely. This type of innovative use of digital technologies enables agility and speed to mitigate short- and long-term operational disruptions, while conforming to physical-distancing mandates and keeping employees safe.
Digital technology can also improve an organization’s ability to “look around the corner” and prepare for the inevitable future shock. For example, predictive analytics can track and absorb the impact of disruptions. Data intelligence can help build resilience by analyzing procurement data to improve transparency and drive toward actionable insights. Meanwhile, Industry 4.0 technologies have achieved productivity breakthroughs in nearshore locations, especially in some high-value-adding, hard-to-ship categories.
The recipe for transforming at scale? Banmali Agrawala, the president of the infrastructure and the defense and aerospace groups at Tata Sons, boils it down to five elements: scale, speed and agility, partnerships, people, and competitiveness. Following that strategic framework, Tata Sons seeded two new businesses during the crisis—one in healthcare and one in electronics. “There is no point in being incremental: it’s important to think about scale more than ever,” Agrawala said. “At the same time, partnerships are extremely critical: re-creating the wheel is futile, and we found willing partners in almost every element of digital strategy we wanted to do.”
Four areas are key in actualizing resilience
The supply chains of industry leaders will be more aligned and responsive to business strategy while delivering in the face of shocks. As a result, investing in some crucial areas beyond digital is the next step toward resilience:
- Performance management. Introduce metrics used to measure resilience, and balance them with typical cost and growth metrics.
- Governance and process. Run supply-chain stress tests in concert with annual strategic-planning process to assess changing factors in the world and if they will create fragility in the supply chain.
- New tools and capability building. Build cross-functional understanding of end-to-end supply-chain dynamics, including functional best practices, and provide access to the tools needed to perform to the new expectations.
- Investor, board, customer, and employee understanding. Help each stakeholder group understand how the company is building resilience and why it matters to them.
The thread that pulls everything together? People.
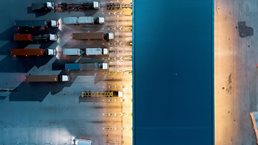
Why now is the time to stress-test your industrial supply chain
“Digital is increasing exponentially. And what is society’s ability to absorb the change? At the center of this change was always people,” said Loree. Stanley Black & Decker reassessed its business operating system in the context of volatility, uncertainty, complexity, and ambiguity. According to Loree, “these macrotrends were part of the rationale for creating a new operating system with people and technology at the center. We recognized the necessity for people and technology to work together and the necessity for lifelong learning of our people to keep current with ever-changing technology.”
Starting the journey to a more resilient supply chain can be daunting, but stress-testing the supply chain is an important starting point for evaluating agility and building an action plan. For industrial companies, the concept of getting more transparency into a supply chain and supplier tiers, stress-testing things that could go wrong, then applying a risk-management mindset and culture to the procurement organization will be one of the changes to come out of the COVID-19 crisis.
As organizations reimagine operations for the next normal, whether manufacturing companies reconfiguring their supply chains and production lines or service organizations adapting to emphasize digital-first, contactless customer journeys, such changes will have significant effects on the requirements for workforce skills and capabilities.