When a high-rise goes up, it is designed to withstand everything from gale-force winds to earthquakes and fires. But few multinational companies have applied the same kind of preemptive stress-testing to their supply chains. Manufacturers have built intricate production networks to deliver efficiency but have left little margin for error. The COVID-19 pandemic has revealed how fragile lengthy, complex supply chains can be—and how much society has riding on their continued smooth functioning.
In recent decades, global supply chains have evolved in ways that leave them more exposed to shocks. Some industries, including communication equipment, computers, and textiles, have grown two to three times more geographically concentrated since 2000. Some 80 percent of world trade now flows through countries with declining political-stability scores, as measured by the World Bank. More global production happens in areas that are highly vulnerable to climate change. And the world has grown more interconnected: when disaster strikes in one region, flows of goods, finance, people, and data quickly transmit ripple effects far and wide.
Even before the pandemic, companies were facing mounting losses from periodic supply-chain bottlenecks and shutdowns. Those costs aren’t “unforeseeable” anymore. In fact, our research found that shutdowns lasting a month or more occur every 3.7 years, on average. Manufacturers in some industries can expect unexpected events to erase the majority of a year’s profits over the course of a decade—and that’s just the baseline, accounting for probabilities like recurring storms and shipping snafus. Extreme one-off events can be far more damaging for companies and societies at large.
Given that the world is undergoing its second “once-in-a-generation” disruption in 12 years, a reappraisal is in order. Building a more resilient form of globalization will require action by both CEOs and policy makers.
A growing awareness of risk may cause some companies to restructure and regionalize their supply chains—at least where there’s a solid business case. Governments, too, may take action to boost domestic production of goods that are deemed essential or important to national competitiveness, reshaping industries in ways that market forces alone would not. All told, we estimate that up to a quarter of global goods exports, worth up to $4.5 trillion annually, could shift to different countries in the next five years or so.
But that leaves three-quarters or more of export flows fairly entrenched where they are at present. Luckily, companies have many other strategies for hedging against disruptions. Most large companies have little visibility beyond the suppliers they deal with directly, but they need to understand vulnerabilities in the deeper tiers of the network. Firms can also engage redundant suppliers for critical inputs, reduce product complexity for more flexible manufacturing, or hold more inventory and cash, just for a start.
A lot of this is well-established conventional wisdom. So why haven’t more companies acted on it? Short-termism is one reason. Many were unwilling to bear the present-day cost of preparing for future hypotheticals. But today, technology offers opportunities to be more resilient and more productive. In an increasingly volatile world, insuring against disruptions can pay off quickly.
CEOs are rapidly awakening to this new reality. Supply-chain operations were rarely on their radar; now, for more and more leaders, they are at the top of their agenda.
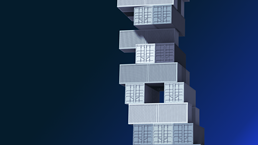
Risk, resilience, and rebalancing in global value chains
The empty supermarket shelves and shortages of medical supplies of recent months have driven home the fact that supply-chain stability is not just a business issue. It’s also about protecting the public interest. Policy makers have a role to play and can actively shape the likelihood and severity of supply chain shocks. Governments have capabilities at their discretion to manage risk that individual companies do not, such as building infrastructure to mitigate flooding and other climate risks, investing in early warning capabilities, and maintaining cutting-edge emergency management capabilities. Countries that want to build robust supply chains will need to make long-term commitments to adopting advanced manufacturing technologies, developing workforce skills that align with industry needs, and building digital and physical infrastructure.
For more than two decades, global supply chains have pushed the boundaries of distance and efficiency. Now the pandemic has delivered a wake-up call that some are stretched too thin—and it’s time to build more safeguards and resilience into the system.