Increased availability of low-cost connected devices has made it possible to collect vast amounts of data from the field. At the same time, advances in machine learning allow companies to apply analytics to discover, interpret, and communicate insights. The combination is already opening new opportunities for those companies that are building significant new capabilities in a part of the business that long seemed resistant to change.
Stay current on your favorite topics
For example, an elevator company installed IoT sensors in equipment to gather continuous monitoring data, and used that data to predict failures ahead of time. The insights enabled the company to optimize maintenance operations, leading to reduced downtime and improved customer experience. Similarly, by adding software capabilities to routers, telecommunications companies can gather in-depth telemetry information that can be fed into analytics engines to generate actionable insights into performance. Such opportunities are already significant and will grow further as the rollout of 5G mobile networks advances and the IoT becomes more mature.
Traditional improvement levers, such as innovative product design, process optimization, and agile ways of working, are still applicable and continue to deliver impact. But to achieve the next S-curve in growth, industrial services companies need advanced analytics-led insights to drive proactive issue identification and resolution.
Companies can apply repair analytics to increase the quality of customer experience by solving issues in the field sooner and faster, enabling higher machine uptime and fewer service calls (see sidebar, “The value is real”). And the opportunity to reduce costs is substantial. For many industrial-services companies, the cost of servicing and repairing equipment in the field has always represented a large portion of costs— often up to 70 percent of operating expenses. Industry players that take a wait-and-watch attitude will likely find themselves at a significant competitive disadvantage in terms of both customer experience and cost base.
Why now?
Although the concept of repair analytics is not new, the convergence of several technology and business trends is accelerating progress toward widespread adoption (see sidebar, “Technology trends”). The volume of data continues to double every three years as information pours in from digital platforms, wireless sensors, and billions of mobile phones. Data storage capacity has increased while its cost has plummeted. Data scientists now have unprecedented computing power at their disposal, and they are devising and leveraging ever-more-sophisticated algorithms.
Additionally, following the general business trend, many industrial companies are seeking to differentiate themselves on the basis of customer experience. And the bar for success is getting higher, with raised customer expectations for quality of service, including uptime and availability. The need to focus on the customer experience is even greater at industrial companies that have turned to aftermarket services to generate additional revenues. As the customer experience moves to center stage, companies must look for new ways to meet customers’ ever-increasing expectations.
Would you like to learn more about our Operations Practice?
What’s the impact?
Companies can use repair analytics to generate tremendous value. Beyond the traditional goal of cost optimization, repair analytics provide opportunities for service companies to increase agility, allocate resources optimally, improve quality of service and customer experience, and develop additional revenue streams.
Increased agility. By speedily identifying the cause of a fault, and automating processes such as parts ordering, repair analytics reduces wait times—enabling companies to achieve faster, more reliable service in both proactive and reactive scenarios.
Optimal resource allocation. With repair analytics, companies can identify failures ahead of time and optimize resource planning, such as for parts, field labor, expert technicians, and external vendor equipment planning and allocation. One medical devices company leveraged repair analytics and ensured parts delivery beforehand to reduce the number of field visits by 20 percent.
Quality of service and customer experience. Companies that successfully apply repair analytics can avoid many issues in the field, or solve such issues more quickly and effectively—even in cases where the customer is not yet aware of the issue. This enhanced capability promotes better quality of service, which upgrades customer experience, helps companies meet commitments in service level agreements (SLAs), and avoid costs. The improvement in customer experience is substantial, enabling the company to achieve a key source of differentiation in today’s business environment.
Capturing additional revenues. Repair analytics allows companies to generate additional revenues in a variety of ways. First, companies can leverage repair analytics to create new service offerings or expand existing offerings, such as by providing maintenance and repair services that have traditionally been the customer’s responsibility. Second, companies can increase the service levels of existing offerings. For example, companies can promise longer uptimes and faster issue resolution—and charge more for these enhanced service levels. Third, companies can use repair analytics to free up workforce capacity and redeploy it to new revenue-generating activities within the services business.
Reducing costs. Repair analytics can help companies reduce both operating expenses related to service provision (such as from complex field-force operations, remote-resolution centers, and call centers), and capital expenditures related to installations in the field. By using a suite of repair-analytics tools, one industrial company managed to increase the percentage of issues resolved remotely from 50 percent to approximately 80 percent. This improvement, in turn, allowed the company to reduce the cost of field operations and focus its field force on providing better coverage of high priority issues.
How do you start?
While the value at stake is high, many companies fail to achieve the full benefits of applying advanced analytics to repair services. They often stay in the experimental or pilot phase, without reaching full-scale deployment. Based on our experience, successful companies get four main things right:
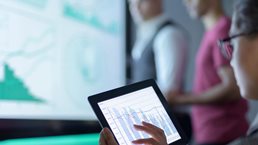
Aftermarket Services: The near-term growth opportunity in targeting the right customers
1. Identify and prioritize use cases
It is important to identify and prioritize use cases based on potential impact and ease of implementation, to ensure that the right ones are selected. The impact assessment should also consider the effect on customer satisfaction and quality of service, which many companies overlook.
Several types of machine-learning use cases are available for repair analytics:
- Anomaly detection. Companies can apply machine-learning techniques to a large amount of equipment data to identify issues and underlying factors that would otherwise be undetected. Such models can be applied retrospectively to identify overall trends and the reasons for issues. For example, one industrial-services firm found that a significant number of unexpected failures occurred a few months after a specific spare part was used in a particular equipment line. This insight allowed the company to develop guidance about the usage of spare parts to avoid future issues.
Anomaly detection can even be applied in real time. To identify anomalies, a company can determine a dynamic baseline of different performance indicators for a specific type of equipment. The company can then apply machine learning to identify which variables will be taken into the baseline. These would include both traditional variables (such as time, day, and seasonality) and other variables (such as usage patterns and external environment effects) that might affect equipment performance and the specific indicator. By implementing real-time anomaly detection in its manufacturing operations, a global advanced-industries conglomerate reduced error-detection time by two-thirds while also increasing yield. - Alarm management. As field equipment sends more alarms to remote resolution centers, it becomes more onerous for staff to identify and resolve issues. The effective processing of alarm data is critical, so that real issues are distinguished from false alarms and their root causes can be identified. Many companies ask experienced agents or equipment specialists to create a set of rules for managing alarms. Although this approach can generate some impact, it is limited by the fact that humans cannot process the same amount of information and identify the same patterns as machine-learning algorithms. The approach is also labor-intensive, compared with a machine-learning algorithm that can improve and adapt the rules over time.
- Predictive maintenance. Ideally, to reduce costs, issues should be predicted and prevented before they occur. For example, over the course of one year, a major utility used its analytics infrastructure to predict 200 events relating to customer service and prevent them from actually happening. Although some issues cannot be predicted (such as external physical harm to equipment), many issues can be (such as those resulting from degradation over time). Issues preemptively identified can be resolved remotely (for example, by remote rebooting and configuration) or through a field visit. Such a field visit can be scheduled before the failure and at a more convenient time, which will reduce costs.
A telco uses this approach to predict failures at cell sites, allowing it to reduce utilization of field technicians and increase the sites’ average uptime. An industrial company that installs security equipment in small businesses uses predictive models to forecast when weather conditions would cause equipment to deteriorate. Based on the forecasts, the company arranges for replacement parts to be drop-shipped before issues occur. - Next best action. Machine-learning models can support human decision making by assessing issues and their severity, and then making recommendations for addressing them. Such recommendations will provide the human agent (either a field technician or a remote resolution agent) or an automation engine with the optimal “next best action” to solve the issue in the fastest way and at the lowest cost.
One business-to-business equipment manufacturer used such a model to optimize its call-center operations. The engine recommends the next resolution step to an agent on the basis of installed-equipment information, real-time environmental data, and keywords used by the customer at the beginning of a call. The use of the intervention has significantly reduced call duration and eliminated unnecessary field visits.
Advanced troubleshooting models are often used to assist other automation engines. RPA bots that usually do simple automation tasks (such as running troubleshooting commands when connected to devices) can become “smart” bots that apply machine learning in the back end to determine the next best action.
Machine-learning models can also augment the use of virtual agents. Most commercial virtual agents only use the customer’s input during a call to determine the next action. By adding machine-learning models to the back end, a company can significantly decrease resolution time and increase the percentage of calls that virtual agents handle successfully. - Optimization. Companies can use machine learning to optimize planning. One example is the optimization of field-force deployment to maximize the impact on customer experience and minimize cost. Another example is to optimize the deployment of different types of equipment based on the costs of the equipment, initial installation, and future repairs.
One European utility is using AI to optimize the installation of its network infrastructure. In a pilot program, the company collected extensive data about the relevant conditions in a specific area, such as the types of trees and depth of their roots. A neural network applies deep learning to the data to assess 30 categories of such conditions. The assessment is used to determine the optimal route for rolling out cable.
2. Make the required operating-model changes
The failure to advance machine learning from experimentation to at-scale deployment often results from poor collaboration between the business, the machine-learning team, and the IT or digital teams. The solution is therefore to define a new operating model.
This model should ensure that the various stakeholders can collaborate to address the right problems, develop machine-learning solutions, and apply the solutions within the existing IT systems. Industrial companies, in particular, might need to set up a remote-monitoring unit that tracks model insights and alarms, and acts on them or coordinates with plant or field operations to take action. It is also important that the company deploy the required change-management expertise within the business.
3. Set the right data and tech foundation
To scale up repair analytics, companies need the right data strategy and technology stack. In the short term, companies may need both to install the right sensors to collect the sufficient data, and to ensure that the data being produced is in a form that can be extracted and analyzed. For the technology stack, the initial requirement is to decide whether to use existing analytics platforms, which are widely available but may not exactly fit an individual business’s requirements, or create new platforms in-house.
4. Combine analytics with other levers
To maximize the value created by advanced analytics, it is essential to combine implementation with other levers such as process improvement and automation. Often, a process must be changed completely to adapt it to advanced analytics. In addition, as noted above, advanced analytics can provide a “brain” for simpler types of automation, such as RPA.
5. Design products to enable repair analytics
As repair analytics rises in importance, products will need to be designed to enable collection of the right data at the right frequency to support remote troubleshooting. Furthermore, decisions about data collection should be made whenever new equipment is deployed in the field, based on a careful predeployment analysis to facilitate decision making.
For existing equipment, adding sensors and controllers is increasingly viable as a form of retrofitting. But a thorough prioritization and cost-benefit analysis should be used to maximize the value of retrofitting investments. Companies should also use data from external sources (such as environmental data). Finally, a basic—but easily overlooked—source of insights comes from maintaining a detailed, accurate database of past service actions, so that over time, advanced troubleshooting models can start to identify which actions have worked in the past.
With enabling technologies now widely available, it’s time for companies to apply advanced analytics to their equipment-repair operations. Indeed, strong capabilities in repair analytics are a prerequisite to realizing the potential of aftermarket services as a growth platform. But successful implementation requires more than just data and advanced technology. It also requires the right talent and the ability to collaborate effectively across business and IT teams. Companies that master the diverse challenges will be rewarded with both bottom- and top-line growth.