Digital manufacturing and design are drawing attention from innovators and investors alike. Sometimes referred to as “Industry 4.0” (especially in Europe) or as the “Industrial Internet” (General Electric’s term), these labels reflect a basket of new digitally-enabled technologies that include advances in production equipment (including 3-D printing, robotics, and adaptive CNC mills1 ), smart finished products (such as connected cars and others using the Internet of Things), and data tools and analytics across the value chain.
These technologies are changing how things are designed, made, and serviced around the globe. In combination, they can create value by connecting individuals and machines in a new “digital thread” across the value chain—making it possible to generate, securely organize, and draw insights from vast new oceans of data. They hold the potential for disruptive change, analogous to the rise of consumer e-commerce. In 2010, when some two billion people connected online, the Internet contributed approximately $1.7 trillion to global GDP.2 What’s in store when 50 billion smart machines—deployed across factory floors, through supply chains, and in consumers’ hands—can connect with one another?
Competitors and policymakers are pooling their efforts to make that happen. In the past year, for example, more than 200 organizations from industry, government, and academia joined in supporting the Digital Manufacturing and Design Innovation Institute (DMDII) to advance digital integration in the manufacturing economy. Participants have committed more than $200 million to support the DMDII, and the US federal government is contributing an additional $70 million. Companies such as Caterpillar, GE, and P&G are among the industry partners. But even as the holy grail of a digitized value chain draws closer, industry leaders are expressing some prominent, common concerns.
McKinsey had an opportunity to poll executives at companies participating in the DMDII.3 While 80 percent of the respondents consider digital manufacturing and design to be a critical driver of competitiveness, only 13 percent rate their organizations’ digital capability as “high” (exhibit). And even among those leaders, many believe that their firms and their industries currently lack necessary standards, data-sharing, and cybersecurity capabilities.
Industry executives report that digital capabilities fall well short of current aspirations.
Across industries, executives at several manufacturers identified a need for dramatic improvements in certain software applications. Reporting dissatisfaction with some vendors’ products in areas such as computer-aided design (CAD), enterprise resource planning (ERP), and manufacturing execution systems (MES), these executives cited examples of applications they found too hard to learn, too slow to evolve and adapt, and sometimes too expensive for small businesses. Some systems are also closed—they don’t communicate with each other or allow others to build upon them. Achieving the transformative potential from digital manufacturing, by contrast, requires information systems that are open, interoperable, and user-friendly.
Successful implementation of digital-manufacturing solutions entails fluid digital communication across the value chain—this continuous flow of data is the digital thread. In response, a number of legacy software vendors, to their credit, are striving to capture a share of this new market. But it’s an open question whether they can move fast enough. The evolution of the consumer Internet does offer some insight for its more nascent industrial counterpart. Today’s consumer-based apps and cloud-based software, for example, are updatable, affordable for the masses, and intuitive to use. Manufacturing leaders yearn for design and manufacturing software solutions and for an app-store ecosystem that can reach the same bar.
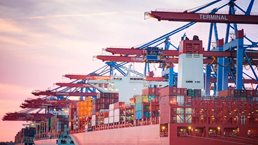
Would you like to learn more about our Operations Practice?
Enabling individuals and machines to communicate seamlessly would of course make production more cost efficient. But perhaps more compellingly, digitizing the value chain facilitates innovation and can directly improve the top line. For example, the aggregation and analysis of data across a product’s life cycle can increase the uptime of production machinery, reduce time to market, and make it possible to understand the product’s consumers. They also make product innovation less about “tribal knowledge” and gut feeling and more of an exercise in analyzing, testing, and responding to hard data and robust simulations.
To that end, the leaders we surveyed were particularly bullish about the impact of digital technologies on product development and design. When they were asked to rank the specific value-chain areas that would benefit most from digitization, one of the highest was the “design–make” link—including the ability to compare “as designed” intent with “as made” data from factories or to predict the quality of new products by using real-time simulations that leverage actual factory data.
Digital manufacturing is already proving its potential to create value at points beyond the design phase. Coca-Cola applied a flexible packaging process in its “Share a Coke” campaign, in which firms collaborated throughout the supply chain and helped increase the company’s soft-drink volumes across world markets. Daimler has rolled out “Mercedes me,” which, among other features, tracks the usage and wear of key automotive parts to help service automobiles more effectively. (For more, see “Marketing the Mercedes way.”) It’s important that the opportunities from digital manufacturing are not just for big corporations. Micro-manufacturers, for example, are using Etsy’s wholesale program as a digital distribution platform to scale themselves up to multimillion-dollar enterprises.
With compelling opportunities across the digital thread, venture-capital firms and other investors will continue to take notice. GE Ventures, for one, opened a Chicago office in 2014, drawn in large part by opportunities to apply digital manufacturing in America’s industrial heartland. Manufacturing remains, after all, a massive driver of the global economy, representing approximately 16 percent of global GDP.4 With those stakes, even marginal improvements will unlock significant wealth.