Lean continues to help manufacturing and service companies the world over improve their performance. Yet at the same time, “optimal” production-system performance is becoming ever harder to define, let alone achieve. The next step in productivity and performance improvement will therefore require companies to take lean beyond the traditional focus on maximizing efficiency.
New challenges
Stay current on your favorite topics
In the future, companies are likely to face constraints on many different resources, including energy and clean water as well as raw-material inputs and the environment’s capacity to absorb waste products. They’ll need to design new types of equipment and production systems that can do more with less and that can move seamlessly between different types of products. And they’ll need to make complex trade-offs to operate those systems in a way that maximizes their overall resource productivity and the lifetime value of manufacturing assets.
Today’s lean practitioners also need to think far beyond the factory walls or even the boundaries of their own organizations. Volatile demand, fluctuating input prices, and complicated, extended supply chains require production systems that can respond appropriately to support changing commercial needs. Companies will constantly need to reevaluate the bigger picture, too, from make-versus-buy decisions for components (or complete products) to choices about whether to repair or replace aging equipment.
Meanwhile, manufacturing technologies are changing rapidly. Rising labor costs, along with cheaper robots and other automation technologies, are driving a dramatic increase in automation. And the nature of that automation is evolving: smart, flexible machines can increasingly take on complex, highly variable, or low-volume tasks. Intelligent machines can diagnose their own maintenance needs. And in hybrid manufacturing approaches, humans work alongside robots or share tasks with them.
New resources
Companies won’t have to navigate these challenges blindly. Technological change has brought with it a host of new resources that companies can draw upon to inform and support continuous improvement and transformation efforts.
First, there is data. Products, and the machines that make them, are studded with sensors collecting reams of data on everything from the temperatures and pressures inside production processes to the habits of customers in the field. Companies today are scratching at the surface of potential uses for the data: on a modern oil-production platform, for example, only 1 percent of the data generated by the 30,000 sensors is ever examined.1
Would you like to learn more about our Operations Practice?
And companies aren’t limited to their own data to inform process improvement. They also have the potential to access vast external data resources from a wide variety of public and proprietary sources. Social-media streams give unprecedented, near-real-time insight into levels of customer satisfaction with products and services. Government agencies provide data on everything from atmospheric conditions to traffic flows on highways.
Second, there is communication. Network technologies allow companies to share and combine data across great distances in real time. Manufacturers can see exactly how well their equipment and processes are performing. And companies don’t just monitor their remote assets; they can control them, too. Many companies now use central groups of reliability and process experts to troubleshoot critical equipment remotely, providing instantaneous, specialized support. One industrial-supply company operates its production plants entirely from a distance, sending maintenance teams into sites only when required.
Fast, high-bandwidth communication technologies are complemented by exploding data-storage capabilities. The “digital universe” of stored data is doubling every two years. By 2020, it is expected to reach 44 zettabytes.2 That’s the equivalent of 1.5 billion years of HD video content, or enough space to store an audio recording of all the human speech ever spoken. Smarter organization, search, and retrieval technologies make that data increasingly accessible—allowing companies to compare today’s production conditions with similar events across the lifetime of the asset, for example, or to look at manufacturing process data for the root cause of product failures in service.
Finally, there is intelligence. Fast computers and smart analytical technologies can spot trends and patterns in huge data sets. Digital models can test thousands of different scenarios to find an optimal solution. Decades of human experience can be embedded in knowledge bases, allowing process-control systems to make decisions faster and more accurately than human operators. Artificial-intelligence technologies allow computers to learn from experience, improving their performance over time.
Using new tools for improved decision making
A crucial task facing manufacturing companies today is to adapt and extend their existing improvement capabilities to make the best possible use of these new resources in solving the challenges they now face. Examples from some of today’s best companies give a glimpse of the potential of this extended lean toolkit.
Optimizing systems with complex inputs
Some conventional approaches to production optimization can have undesirable side effects. For example, focusing on maximum yield when running a process plant can lead to excessive energy consumption, needless wastewater-processing costs, or greater downtime and maintenance costs. As companies gain access to more data on historical performance, and use that data to build comprehensive models of plant behavior, they can take a much more holistic approach to their process management and control efforts.
A particularly powerful way to do this is by expressing plant performance in terms of profit per hour.3 One mining company used this approach when declining ore quality caused output to fall at a major site. The company structured its historical data to express processing performance in terms of profit per hour and then used a neural-network model (a type of artificial-intelligence technology that emulates the way biological brains learn) to explore the relationship between certain process variables, such as the concentrations of reagents used, and material recovery.
This analysis revealed that optimizing a handful of variables had the potential to boost the quantity of materials extracted from a given grade of ore by more than 7.5 percent—with a slightly greater increase in profit per hour, since the optimized process also reduced the consumption of other inputs. That surprising finding ran counter to the engineering department’s previous beliefs about how best to optimize processes. Reducing the material wasted in processing not only helped the mine meet its production targets, but also cut costs significantly because the mine extracted and processed less material and could run in a less demanding manner. Consequently, profit per hour increased by 9 percent.
Scenario modeling
Modern manufacturing systems and their related supply chains are highly complex. Materials and components are sourced from multiple suppliers at varying prices and quality levels. These inputs may flow through different production routes and through different equipment within individual plants, or through processes that take place at different plants or with different subcontractors. They may be transformed into different products, subproducts, by-products, and waste products, with associated interactions and restrictions. Different customers in different markets may buy those various products, at prices that change frequently. All that complexity makes it hard for manufacturers to be sure they are making the best decisions about what they buy, make, or sell at any given time.
Historically, the models manufacturers use to support these decisions have relied heavily on lots of assumptions and simplifications, such as the use of approximate “transfer pricing” to determine which raw material to buy, which individual product to make, and even which manufacturing unit or location should produce each product. These assumptions and simplifications can lead to poor decisions. Artificially high transfer prices may generate suboptimal use of network assets or make high-potential opportunities appear unprofitable.
Today’s powerful computer systems allow companies to build detailed models of their entire value chain, from procurement all the way to customer demand and final delivery. Advanced optimization packages, using detailed data, can rapidly test hundreds or even thousands of different combinations of products, manufacturing facilities, and processes, with the aim of maximizing the margin for the organization within defined constraints. Critically, while the behind-the-scenes analysis in such systems is highly advanced, the latest tools are simple to operate, with straightforward spreadsheet-like interfaces.
One European manufacturing company used such an approach to identify immediate tactical changes that delivered cost savings of several million euros per year. The company started manufacturing a key intermediate product on an underutilized line instead of buying it from a third party. It also shifted the production of another key intermediate to different equipment that offered higher yields, reducing raw-material costs. The company then identified several short-term strategic opportunities to increase capacity through the application of an operational- and reliability-excellence program for key production assets. Incremental sales volumes resulted, thanks to increased production capacity across several high-margin product categories. Together, these changes allowed the organization to boost its earnings before interest and taxes (EBIT) by more than 50 percent in a commodity industry historically used to low returns on sales.
Using real-time data
Fast data collection and analysis allow companies to fine-tune process parameters in real time or “near” real time. One chemical company used such an approach to optimize yields in a continuous-reaction process. The company applied a neural-network model to adjust the operating point of the reaction based on feedstock quality and catalyst life. The new approach boosted yields by 0.5 percent, a significant jump in a highly optimized process that was already more than 90 percent efficient.
Automated learning and decision making
The availability of more data and the processing power to deal with huge data sets are changing the way manufacturing systems are controlled. Sites can use historical process data to adjust their control systems automatically, resulting in systems that recognize and react instantly to disturbances, such as a change in the quality of the material entering a process. Machines can also use such data to continuously improve their performance over time.
Advanced-analytics techniques are also becoming much better at dealing with the kinds of fuzzy issues whose solutions once required deep operator experience or trial and error. A change in the output of a manufacturing process might have numerous root causes—from tool or part wear to upstream materials contamination. Armed with data on the characteristics of the system, fault-detection-and-classification (FDC) systems can use statistical models to interpret the most likely causes and then either automatically adjust process parameters to compensate or recommend to operators the best corrective actions.
Integrating across activities/functions
Companies can now integrate data on the production system’s activities with data on the system’s outputs, revealing correlations between the activities and the outputs. These correlations help to ensure that the lean system is operating effectively so that issues can be quickly identified and fixed.
An example is overall equipment effectiveness (OEE), a familiar measure of operating productivity. By combining historical OEE levels with information from other organizational functions, such as supply-chain and sales data, companies can assess and understand the true business impact of process and equipment losses stemming from problems such as unplanned downtime, slow-running equipment, and slow changeovers.
Leading lean companies use benchmarking to set stretch targets for their higher-level asset-productivity measures (such as machine utilization) and operational-efficiency ones (including cost per unit, per plant, and per product). By linking business-performance metrics with OEE data on individual lines, companies see the likely impact of missed targets on financial performance, helping them prioritize the implementation of countermeasures to avoid loss.
When parts of a production system do underperform, data analysis can aid root-cause identification—for example, by correlating OEE measures with adherence to operating standards for measures such as staffing levels or the use of standard operating procedures in changeovers. The same approach can help prove the value of lean activities, such as leader standard work, in boosting performance and productivity, which has until now been difficult to do.
Cross-functional data can also directly improve manufacturing planning. Rather than adjusting their standards for batch sizes, production sequences, and product changeovers on an ad-hoc or periodic basis, companies can combine historical data and forecast trends to create schedules and production plans almost in tandem with changes in demand.
Capturing and sharing knowledge
Advanced software tools are also revolutionizing the way organizations store and communicate their know-how across the enterprise. Leading companies have always made efforts to capture and codify best practices, from waste-reduction ideas to techniques for fine-tuning equipment-operating parameters and maintenance activities. The latest generations of these software systems have become more powerful (thanks in part to built-in calculation engines) and better integrated, with links to an organization’s planning, maintenance, and manufacturing-control systems.
This combination of power and integration helps companies use their knowledge to the fullest extent. If an energy-saving idea is implemented successfully in one plant, for example, such systems can identify other facilities in a company’s worldwide network that could use the same approach. They can even calculate the likely savings, so staff can prioritize the change in their ongoing improvement plans.
Presenting information in new ways
In consumer sectors, increased processing power and advances in display technology have produced a user-interface revolution. High-resolution displays, 3D graphics, and motion-sensing technologies promise to bring a similar revolution in manufacturing.
Augmented-reality systems add digital information directly to an operator’s field of view, using wearable devices including smart glasses. In trials, these advances helped warehouse staff find and pick products faster and more accurately, boosting productivity by 25 percent. One industrial manufacturer is developing an augmented-reality system that can lead technicians through maintenance activities—guiding them through the steps for inspection and parts replacement, and even locating the necessary parts. Certain airlines are testing video-camera-equipped glasses that allow maintenance personnel to review live images of faults and engage in problem solving with colleagues thousands of miles away.
Capturing the benefits
As with so many promising new approaches, companies are challenged to move from experiments, pilot projects, and isolated success stories to a sustainable, organization-wide approach to total productivity improvement as part of their production system. To do that, they will need three enabling components: a strong technical infrastructure, the right skills and capabilities, and new thinking about organization and management methods.
Technical infrastructure
The technical foundations of the new approach will start with data. And the first challenge for many organizations will be ensuring they have sufficient access to data, either their own or what is available from outside resources. The makers of manufacturing machinery are likely to be every bit as interested in the data generated by their equipment as their customers are, for example. OEMs are already making access to their customers’ use and performance data part of their ongoing service-and-support agreements. Likewise, manufacturers weighing the short-term convenience of outsourcing will need to ensure they do not sacrifice access to valuable data and the improvements it can bring.
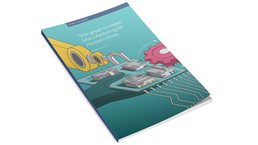
The great re-make: Manufacturing for modern times
The next challenge will be having the right systems and tools for storing, cleaning, organizing, and visualizing the data companies have. Today, data assets are typically widely distributed in different systems and formats. A total productivity approach requires greater integration so that all parts of the organization are operating on a single version of the truth. Creating a suitable architecture and the systems to handle it in large organizations will be a formidable challenge.
The development of a production infrastructure that supports this level of integration will call for new partnerships, too. Today, different (and sometimes proprietary) standards make it hard for companies to pull together inputs from all their equipment. Efforts to change this are under way. An example is the draft API (application programming interface) standard for onboard technology in mobile mining machinery, published by the Global Mining Standards and Guidelines Group, a consortium of operators, equipment manufacturers, and third parties.
Capabilities
Total productivity improvement will require new capabilities, too. The approach will demand all the traditional lean and process-improvement skills that manufacturing companies have worked so hard to develop over the years. It will also need new skills, especially in the areas of data management and advanced analytics.
Companies will need to create new roles for data scientists and IT specialists to work alongside their existing operations teams. But they will also have to invest in the development of cross-functional skills, with specific training in data-driven decision making for operations personnel. Managers will require new capabilities, too, as the ability to understand, interpret, and act upon data will become increasingly important to their roles. Care must be taken, however, to ensure that decisions are made at the proper level in the organization. A data-rich future will make it even easier for senior-level people to get lost in the weeds.
Organization and management
Manufacturing organizations will need to change in order to accommodate a larger, more tightly integrated IT function, together with more specialized data handling and analysis in support of production roles. But they will also need to redefine every role in the organization, from the operational front line to the CEO. Targets and key performance indicators will have to evolve, for example, to avoid creating incentives for suboptimal performance.
Companies will also need new ways to monitor progress, such as by measuring the rate at which staff are trained in new techniques, and their level of acceptance of new improvement tools and approaches. Technology will have a role to play here, too. Software tools can collect data on how and where they are used, for example, giving managers insight into the maturity of application use across the organization.
The engineers and managers running tomorrow’s manufacturing plants will face increasingly relentless pressure to improve performance. Their targets won’t just be more stringent, they’ll be more complex, too, with the need to balance a host of factors including quality, yield, energy consumption, and cost-effective asset life, all set against a background of rapidly changing demand from customers and the wider business. To meet these challenges, companies will need to systematically embrace, create, and evolve new technologies, methods, and analytical methods. We’ve described some of those in this article; others surely are yet to be invented.