This is the fourth article in our series on the application of digital approaches in heavy-industry manufacturing operations. Earlier parts of this series examined the digital opportunities available to heavy-industry players (Exhibit 1), discussed the need to design and execute a systematic digital journey in order to capture those opportunities, and described the critical enablers that companies should put in place to support that journey.
In this piece, we take a deeper dive into three elements that play an outsized role in determining the success or failure of a digital transformation. The first of those elements is a clear vision, outlining the company’s long-term ambition to reinvent its operations, or even its business model, with the aid of digital technologies and new capabilities. The second is a comprehensive diagnostic effort, so the organization really understands where the digital opportunities are, what they are worth, and what it will take to capture them. The third is a detailed roadmap that sets out the sequence and timing of the organization’s digital journey.
Building a vision
Two-thirds of companies are already pursuing, or planning to pursue, digital-manufacturing initiatives. Yet almost 70 percent of those companies say that they are struggling to move beyond the pilot stage into large-scale adoption of new digital approaches.
It doesn’t need to be this way. The first big step a company can take to avoid the pilot trap is establishing a clear, comprehensive, and compelling digital vision. A strong vision starts with the organization’s people. What will the digitally augmented way of working look like? How will technology make work more efficient, effective, and satisfying? How will the organization reinvent its operations and business models with the aid of technology?
The vision should be bold and far-reaching: looking forward 10 to 15 years. It should also be urgent, emphasizing the need for an agile approach, in which the foundations for future success are laid by the changes made today. Finally, it should be achievable: grounded in reality, with every technological aspiration linked to a real source of strategic value.
As they craft their vision, executives often find it tricky to strike the right balance between ambition and achievability. And in heavy-industry manufacturing, there is a strong tendency to err on the side of caution. To avoid that mistake, we always encourage business leaders to spend time understanding the limits of the possible. They can broaden their horizons in many ways: by talking to inspirational digital visionaries, by visiting “lighthouse” facilities (in their own sector and in others) to see the impact new approaches are delivering elsewhere, or by attending major conferences or trade fairs.
Some companies make the opposite mistake: They become so enamored with exciting new technologies that they lose sight of the real purpose of any digital effort: to add value to the business. Avoiding that trap requires a rigorous and dispassionate assessment of the business case behind their digital ambitions.
Until very recently, companies struggled to build digital business cases. The number of technological avenues to explore was large, and many approaches were so new that their value propositions were not always clear.
That situation is now changing. As more companies integrate digital approaches into their operations, others can learn from their successes. Emerging benchmarking approaches allow companies to take a top-down view of their operations to see where leaders in their own and related sectors have found most value from these new technologies.
Benchmarking is another way an organization can identify the gaps between its current state and the future state necessary to achieve its vision, looking not only at technology, but also at the process and organizational attributes that allow digitization to deliver its full potential (Exhibit 2).
Would you like to learn more about our Operations Practice?
The digital diagnostic
Once an organization has defined its digital vision, it is time to dive into detail. A digital diagnostic provides companies with a structured way to confirm the value of their chosen digital approaches. Many companies will be familiar with use of a diagnostic approach as a starting point for performance improvement initiatives using lean-management methodology.
A digital diagnostic shares many features with its lean predecessors. Indeed, a key goal of the diagnostic is to ensure that the organization has the right foundations in place. Those foundations include all the proven ingredients of operational excellence: an effective technical system to run the plant’s processes, a robust management system to monitor and improve those processes, and a people system that promotes the right mind-sets and behaviors across the organization.
There is no substitute for these fundamentals. Digital approaches deliver value only if the organization has the capabilities and structures in place to use them. Advanced digital dashboards can provide frontline teams with a granular, real-time view of operational performance, for example. But the company still needs the ability to apply root-cause problem solving and other longstanding tools to turn those insights into performance improvements.
Digital transformations also have their own specific requirements. The organization needs appropriate technology infrastructure, for example, a requirement that includes both the IT systems used by the wider business and the operational technology (OT) systems used to control and monitor manufacturing processes. And it needs people with specific digital skills to interpret data, build models, and modify processes based on those models.
Picking the right location for the diagnostic requires care. A suitable location has significant improvement potential, addressable using the organization’s chosen digital approaches. Ideally, the site is sufficiently similar to others so that the transfer of knowledge—and the scaling of solutions developed during the diagnostic—will be relatively simple. And because the real purpose of a diagnostic is to evaluate the potential of new digital solutions, an engaged management team who have mastered the basics of operational excellence is a prerequisite as well.
Evaluating the potential
A digital diagnostic aims not just to identify improvement opportunities, but also to demonstrate them. The problem addressed during the diagnostic should generally be something be real, urgent, and significant—yielding feasible, pragmatic solutions that the site can use to achieve meaningful performance improvement.
In heavy-industry manufacturing today, the most significant and accessible digital opportunities are often uncovered through the application of advanced analytics. Here, a diagnostic approach will typically proceed in phases.
First, the organization defines the transformation’s business objectives so that they are clear, meaningful, and measurable in financial terms. The company will then assemble a dedicated diagnostic team with expertise in digital and analytics approaches, in the organization’s manufacturing processes, and the business objectives. For the duration of the diagnostic, that team works together in one space, following a clear timeline for analysis, review, and debrief activities.
The team’s initial task is to establish the process’s financial and operational baseline. This includes the key metrics that the digital effort will aim to improve, and targets for those improvements. The team can also spend this time ensuring that participants have a good understanding of the basic characteristics of the process, such as the relevant chemistry and physics, as well as any recent or planned changes that might have an impact on process performance or business requirements.
The diagnostic team will then begin to capture data from existing sources, such as sensors, controllers, manufacturing planning and execution systems, or the quality-assurance lab. It will store that data in a suitable repository, either on-site or in the cloud. It will structure and clean the data in preparation for analysis.
Next the team will sketch out an initial list of improvement hypotheses. They will make an initial evaluation of their hypothesis through process observations and conversations with plant staff, in order to prepare for the analytical effort and identify potential gaps or problems with the available data. In parallel, the team will assess the current state of the site’s IT and OT infrastructure and its suitability for the most promising digital use cases on their list.
With the foundations in place, the analytical work of the diagnostic can begin in earnest. The cross-functional team of data analysts and domain experts will explore the data to identify critical parameters and value drivers. They will build predictive models, using insights derived from the data, and—critically—use the knowledge and experience of domain experts to refine those models. Then they will use their models to design improvement measures. Those measures might be one-time changes to processes or equipment configuration at the site, or they could be the introduction of a new, analytics-based approach to operational decision-making or process control.
The outcome of the diagnostic will be a set of impact opportunities, along with an estimate of their costs and potential, and the technical and human capabilities required for the deployment of each opportunity.
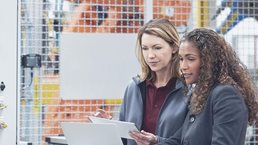
Enabling a digital and analytics transformation in heavy-industry manufacturing
Building the roadmap
Once an organization understands where its digital opportunities are, what they are worth, and what it needs in order to capture those opportunities, it can begin to plan the roadmap of its digital transformation.
To build an actionable roadmap, the company prioritizes its use cases, balancing impact with complexity of implementation. Some digital levers may require few changes to existing IT or OT infrastructure, for example, allowing them to be deployed early in the transformation. Others may require the introduction of new infrastructure, with the time and resources needed accounted for in the plan.
Likewise, digital skills can be a significant bottleneck to deployment at scale. The roadmap thus identifies the new capabilities that are required, and a plan for their acquisition. Personnel for some specialized roles may need to be sourced externally, but some advanced organizations have found that they can access most of the skills they need by systematically developing the capabilities of their existing workforce.
Rolling out new approaches across a multisite network also requires careful consideration. As we discussed in an earlier article, digital approaches diverge significantly after the diagnostic phase. Where a single uses case offers rapid, significant improvements at multiple sites in the network, the organization may choose the tactical-intervention approach, deploying the new method across its network in a fast-track series of digital projects.
Alternatively, the company may adopt a lighthouse approach, in which picks a single site, or one site per region, then implements a complete transformation of the lighthouse sites, aiming to capture more than 80 percent of the identified use cases’ value. Over time, those lighthouse sites become the benchmark for the transformation of other sites in their region, providing inspiration and direct to support for subsequent digital efforts.
Or the company may conduct a focused transformation using a hub-and-spoke approach. Here, a smaller subset of use cases is deployed in parallel across a group of sites within a region. That simplifies capability building efforts, and allows sites to share experience and best practices with their neighbors.
Deploying a digital transformation is a big learning experience for most organizations. As companies solve problems and uncover new opportunities during the rollout, they can revisit their roadmap, adapting it in an agile and iterative manner to incorporate emerging best practices.
The digital transformation of manufacturing operations in heavy industry presents the sector with significant opportunities to improve productivity, quality, and flexibility. Some of those opportunities are delivering real impact today, especially the application of advanced analytics to improve process performance and the adoption of digital work-management tools. Others, such as the use of advanced robotics systems, are still evolving.
Digitization will be a multiyear journey. The imperative for heavy-industry players right now is to get those journeys under way. That calls for a bold vision, a clear understanding of their current capabilities and limitations, and a roadmap defining the actions required to make change happen. It also requires an agile approach. Companies will need to identify, develop and deploy the digital tools and approaches that offer the most value to their business, and new ones are emerging all the time. Organizations that move earlier and adapt faster than their competitors are likely to reap the largest long term rewards.