Most product-development tasks are complex optimization problems. Design teams approach them iteratively, refining an initial best guess through rounds of engineering analysis, interpretation, and refinement. But each such iteration takes time and money, and teams may achieve only a handful of iterations within the development timeline. Because teams rarely have the opportunity to explore alternative solutions that depart significantly from their base-case assumptions, too often the final design is suboptimal.
Stay current on your favorite topics
Today’s technology offers an alternative. Digital simulation and analysis are now so fast that designs can be evaluated in seconds—or even less. Algorithms can automatically adjust the geometry of a part between simulations, with no manual refinement required. Using artificial-intelligence techniques, these new generative design systems can explore a much larger universe of possible solutions, comparing the results of thousands of simulations to close in on a design that delivers the most favorable combination of attributes.
For some types of engineering problems, generative algorithms already outperform human engineering teams. Furthermore, they can produce non-intuitive solutions that may never have been found using traditional processes.
The most common use for generative design algorithms today is structural optimization: creating parts that provide sufficient strength, stiffness, and fatigue resistance with the minimum of material. Such applications are common wherever weight is a primary consideration, such as in the design of internal structural parts for handheld tools (to improve ergonomics), sports equipment (to enhance performance), vehicles and aircraft (to reduce fuel consumption or increase payload), or any product where shipping weight is a significant cost driver. When material is a primary cost driver, greater structural efficiency can lead to substantial savings both from a cost and a sustainability perspective.
Across industries ranging from automotive to aerospace to sporting goods, generative algorithms have reduced part cost by 6 to 20 percent, part weight by 10 to 50 percent, and development time by 30 to 50 percent (exhibit). A power-tool manufacturer, for example, reduced a die-cast support bracket’s part weight by 26 percent and its cost by 8 percent, without affecting the interface between the part and the larger assembly. For a large, die-forged component, generative optimization yielded a weight reduction of around 40 percent—subtracting a full kilo from the finished product.
Would you like to learn more about our Operations Practice?
How generative design can flex
Generative design and additive manufacturing (AM) technologies are often seen as natural partners, since AM machines cope well with the complex, organic shapes that often emerge from such algorithms. Yet AM is hardly a requirement in implementing generative design: the latest generative systems can be configured to account for limitations in manufacturing processes. That flexibility expands the range of parts that generative design can target, while making it easier for design teams to evaluate alternative manufacturing techniques.
Moreover, generative algorithms are not limited to structural-design tasks. The approach is already being applied to other engineering domains, such as electrical and thermal design, fluid-flow optimization, optics, and acoustics. Architects and urban planners are even adopting generative techniques to optimize the layouts of buildings and city spaces. Similar algorithms are being applied to complex optimization problems arising entirely outside the product-design space (see sidebar, “Generative algorithms in procurement”).
Generative design’s role in end-to-end product development
Like other novel digital methodologies, generative-design techniques have already shown that they can boost performance significantly in real-world applications. Their full potential will not be reached, however, until companies apply these concepts at scale, making them an integral part of product-development processes.
Acquiring the right software tools is only part of that of the solution. Engineers and other stakeholders also need to know how to use the new tools effectively, fully understanding their capabilities and limitations. Good design discipline will still matter, too: although generative-design methods can produce creative, non-intuitive solutions, engineers must still validate the output through testing or analysis—and must ensure the design can be manufactured using the intended process. This human–machine interaction will continue to evolve as algorithms get smarter and engineers learn how to fully utilize these new tools across a wide range of applications.
Companies will need to ensure they apply generative-design approaches across the entire commercialization process as well. Generative algorithms can offer value at multiple points in the journey of a product from concept to market:
- Initial concept. Testing new shapes and geometries, translating innovative ideas from the designer’s mind into a tangible product.
- Detailed design and engineering. Achieving new levels of product performance while minimizing cost.
- Manufacturing. Assessing candidate geometries for manufacturability and, where applicable, enabling and accelerating the use of additive-manufacturing processes.
- Product improvement. Supporting design-to-cost, -value, and -weight efforts, unlocking additional value and margin improvement.
- Procurement. Structuring complex tender processes to improve tradeoffs among pricing, technical capabilities, traceability, risk, sustainability, and other factors.
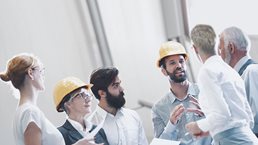
Making cost engineering count
Challenges, opportunities, and enablers
For today’s product-development leaders, generative-design technologies present a number of significant cultural, organizational, and competitive challenges.
One of the first barriers is likely to be stakeholder acceptance of the resulting parts and products: generative algorithms produce designs that may be radically different from their human-designed predecessors. Some observers even find them “alien” or disturbing. That can hinder the acceptance of generative solutions by internal stakeholders, even when the proposed designs are technically superior. Using generative design for customer-facing parts creates similar acceptance challenges, although some companies are already capitalizing on the approach to create products with a unique and highly differentiated appearance.
A second major challenge is cultural. The large-scale adoption of generative approaches could change a company’s requirements for talent, knowhow, and resources in the product-development function. For example, generative solutions may involve less time from experienced engineers and designers, which may enable shorter product-development cycles. That raises questions about organizational design and resource allocation for established players, and potentially lowers the barriers to entry for new competitors.
The third set of issues concern process integration. Companies need to think through how generative approaches will mesh into existing engineering processes, data platforms, and toolchains. The rapid development pace of generative-design technologies means companies will likely need more flexibility to use different tools from different vendors, with the ability to exchange and upgrade their design tools as technology evolves. That requires open, adaptable systems and a high level of agility in both the product-development and IT functions.
In the coming years, generative algorithms will continue to evolve, becoming more powerful, more widely applicable, and easier to use. As additional computing power becomes available, it will be possible to extend the approach beyond the part level to permit the optimization of assemblies and, ultimately, complete products.
Several leading companies are already taking generative design beyond the pilot phase and applying it across their organizations. That requires investment in tools, education, and cultural change. But for those willing to commit, the positive effects on time to market, cost, and product performance are likely to be significant.