For decades, many of the world’s best companies have used their production systems as a source of sustainable competitive advantage (see sidebar “What is a production system?”). But such a system isn’t just about doing things well, with fast, efficient manufacturing processes and consistently high quality. What differentiates benchmark organizations like Danaher or Toyota is their ability to improve those operations continually, at a pace their competitors struggle to match.
Strong production systems have other powerful benefits too. They give companies a clear, precise picture of their own performance, allowing direct comparisons among plants, for example, and encouraging internal competition. They provide a common culture, vocabulary, and tool set that facilitates the sharing of best practices while minimizing confusion and misunderstanding. And by developing the skills of existing staff and creating an attractive environment for talented new hires, they help people contribute to the best of their ability.
The best production systems are simple and structured, and built around a company’s specific strengths and challenges. That requires a good deal of self-knowledge. A company must not only understand what it wants to achieve but also identify the methods, resources, and capabilities it will need to get there. Ultimately, a good production system is a unique, bespoke management approach that’s difficult for competitors to copy.
Today, even the highest-performing companies can boost their performance still further. That technology-driven opportunity comes from data—specifically, the huge volumes of data on processes and performance generated by new generations of network-connected devices: the Internet of Things (IoT). To capture the opportunity, companies must revisit and reassess many of the processes and principles that have been so successful for them in the past.
Four dimensions of the IoT’s impact
The advent of IoT technologies—and the more general move to digital tools that support operations, communication, analysis, and decision making in every part of the modern organization—won’t change the fundamental purpose of production systems. It will, however, transform the way they are built and run, offering improvements across four main dimensions:
- connectivity
- speed
- accessibility
- “anchoring”
Connectivity
Traditional production systems embody a collection of separate tools bound together loosely by the rules governing their application. Usually, these rules are at best defined only on a paper document or a corporate intranet site. In the future, such links will be much tighter and more automated, and fast digital connections will allow the whole system to operate as a seamless, cohesive whole.
Integration will change production systems in two ways. First, performance measurement and management will be based on precise data. Sensors will monitor the entire production process, from the inspection of incoming materials through manufacturing to final inspection and shipping. Companies will store the output of those sensors in a single, central data lake, together with a host of additional data from other internal sources, as well as external ones (supplier specifications, quality indicators, weather and market trends). All these strands of data will combine to set the production system’s targets and measure its performance continually, so the staff will be able to see, at a glance, if the system is performing as it should.
Would you like to learn more about our Operations Practice?
Second, connectivity will support better fact-based decision making. Access to comprehensive, up-to-date production information, together with a complete historical picture, will take the guesswork out of changes and improvement activities. As the collection and reporting of data are increasingly automated, frontline operators and managers will play a larger role in solving problems and improving processes. Root-cause problem solving will be easier: aided by advanced analytical techniques, staff will be able to identify the changed operating conditions that precede quality issues or equipment failures. Furthermore, stored information about similar issues solved elsewhere will help identify appropriate solutions.
Speed
Today’s production systems are necessarily retrospective. While they aim to maximize responsiveness by emphasizing discipline, standards, and right-first-time practices), the reality falls short. Manual measurement and management mean that most opportunities for improvement cannot be identified until a shift ends and the numbers come in.
With the introduction of comprehensive, real-time data collection and analysis, production systems can become dramatically more responsive. Deviations from standards can immediately be flagged for action. The root causes of those deviations can therefore be identified more quickly, as will potential countermeasures. The entire improvement cycle will accelerate.
It isn’t just the management of day-to-day operations that will get faster. Capability building will, too, thanks to focused, online training packages customized to the specific needs of individual employees. Finally, IoT technologies will speed improvements in the production system itself—for instance, by automatically identifying performance gaps among plants or updating processes throughout the company whenever new best practices are identified (see sidebar “The production-system transformation of the future”).
Accessibility
Back-end data storage isn’t the only thing that will be unified in the production systems of the future. So will access. Staff at every level of the organization will get the tools and data they need through a single application or portal (see sidebar “The human factor”). That portal will be the organization’s window into the system’s dynamic elements—especially minute-by-minute performance data—as well as more static parts, such as standards, improvement tools, and historical data.
These portals—with responsive, customized interfaces ensuring that the right employees get access to the right information and tools at the right time—will simplify and accelerate the operation of the production system. If it identifies a deviation on a production line, for example, it will be able to alert the team leader, show current and historical data on that specific process, and offer appropriate root-cause problem-solving tools, together with a library of solutions applied elsewhere.
Using secure and tightly controlled interfaces, the production-system portal will also be accessible beyond the organization’s boundaries: it will allow suppliers to track consumption and quality issues in materials, for example, or external experts to review current and historical performance to find improvement opportunities. Using online support and predictive analytical tools, manufacturers of equipment will increasingly operate, monitor, and maintain it remotely. The portal will even allow companies to benchmark their own performance automatically against that of others.
Anchoring
One of the most powerful effects of IoT and digital technologies, we foresee, will be to anchor the production system in the organization’s psyche. This will overcome the most critical challenge many companies struggle with today: sustaining change, so that the organization improves continually.
That anchoring effect will be achieved in several ways. First, the unified data, interface, and tool set will not only help enforce the adoption of standards but also ensure that the right way of doing things is the easiest way. Staff won’t need to improvise production plans or override machine settings if the optimum settings are just a button click away.
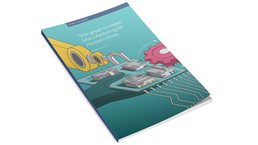
The great re-make: Manufacturing for modern times
Second, future production systems will help the organization to collaborate more effectively. An end-to-end view of performance will break down barriers among functions and ensure that decisions reflect the interests of the business as a whole. The communication and sharing of information will be greatly enhanced, since a central knowledge hub and social-media tools will let staff in one area access support, ideas, and expertise from another.
Finally, future production systems will make performance far more visible: when the whole leadership can see the direct link between operational performance and profitability, for example, the production system will no longer be considered the concern solely of the COO. Digital dashboards on computers, mobile devices, and even smartwatches will show staff in every function and at every level exactly how the organization is performing, as well as the precise value of the contribution of their businesses, plants, or production cells. The result will be genuine transparency—not just about where the value is being created, but also about how.
Adopting IoT: Early wins
Although the fully integrated digital production systems described in this article don’t yet exist, many of the building blocks are already in place. The oil-and-gas industry, for instance, is rolling out industrial-automation systems that can monitor the health of expensive capital assets in remote locations. These systems facilitate timely preventative maintenance by using sensor data to generate real-time performance information and provide an early warning of potential problems. Automakers already have production lines where hundreds of assembly-line robots are integrated with a central controller, business applications, and back-end systems. This technology helps companies to maximize uptime, improve productivity, and build multiple models (in any sequence) without interrupting production.
The next challenge for manufacturing companies is to complete the integration process. This will mean taking the tools and capabilities that now work on individual production lines or assets and extending them to the entire enterprise and then its entire supply chain. For companies that succeed, the reward will be greater efficiency, rich new insights, and dramatic, continual improvement in performance.