Imagine if people could design and develop their dream homes simply by going online to find the solution that best suits their means and lifestyle. Imagine being able to pick from a menu of standard base designs and being able to customize fittings, furnishings, and smart equipment. Then imagine being able to use a digital interface to obtain quotes from vetted contractors for everything from surveying the plot to assembling the house. And the pieces of the house itself arrive in the form of prebuilt panels and modules in a container from a centralized robotic factory. This is what is meant by “industrialized delivery systems”—and these will play a crucial role in the future of the real-estate and construction sectors.
Stay current on your favorite topics
In reality, early versions of this future already exist, with several venture-funded home builders in the United States aspiring to channel the customer-experience revolution pioneered by consumer-goods companies into the residential-property space. We are likely to see the creation of standardized home-building platforms, with developers working with an ecosystem of companies providing an array of fittings, furnishings, and equipment solutions. The result is a seamless customer experience and a more sustainable end product.
Skeptics may argue that such industrialized delivery innovations will focus on the lower-priced segments of the market, while the construction of high-end real estate will remain unchanged. Early evidence suggests, however, that this will not be the case. Industrialized delivery systems are poised to disrupt the real-estate sector across all asset classes and price points.
There is little doubt that the construction process adopted today badly needs innovation, mainly to improve the speed of delivery and reduce the dependence on manual interventions. A key enabler for this transformation is modular design, geared for production and assembly rather than field-based on-site work.
Would you like to learn more about our Capital Projects & Infrastructure Practice ?
We are already seeing progress toward this future. Three technologies that already exist are of particular interest.
Virtual design and construction (VDC). Digital platforms, such as 5-D building-information modeling (BIM), enable the creation of a “virtual twin” of physical projects. This not only allows design optimization—in the form of more precise estimates, value engineering, constructability, and interface checks—but also provides transparency and project-management oversight over the life cycle of the project. Coupled with emerging industry trends, such as integrated project-delivery contracts, VDC is a powerful tool to help finish projects on budget, on time, and on spec.
To realize the full benefit of using 5-D BIM for projects, developers and contractors must fundamentally rewire their design, estimation, and project-management processes. That means contractors and clients must work closely together, backed up by clear contracts, to share both risks and gains.
Prefabricated, prefinished volumetric construction (PPVC). PPVC involves the factory construction of interlocking building modules, each equipped with internal finishes, fixtures, and fittings. These elements are then transported to the site for assembly and installation.
PPVC is slowly but steadily gaining popularity because it accelerates the construction process, with productivity gains of as much as 30 to 50 percent, according to case examples in Singapore. PPVC works particularly well for less-complicated and standardized designs. Other benefits include higher, more consistent quality; less waste; and better health, safety, and environmental performance because of the shift from chaotic field sites to a more controlled factory environment.
Singapore is one of the leaders in the use of PPVC. The city-state’s Building and Construction Authority encourages deployment of this approach—not just for hotels, hostels, dormitories, and industrial facilities but also for middle- to high-end residential developments. The technique can accommodate both concrete and dry walls. It is also corrosion free and fire safe. So far, it has been used in buildings as high as 25 stories.
Deploying PPVC implies changing design standards, assumptions, and processes to adopt the Design for Manufacturing and Assembly approach. It also requires better production-planning, supply-chain, and logistics-management capabilities, given that modules need to be produced remotely and regularly shipped from factories to sites. These are areas in which many contractors are lacking. Few in the sector have anticipated this shift from construction to production, let alone budgeted and provided resources for it.
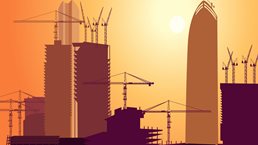
Imagining construction’s digital future
3-D printing. While 3-D printing has not yet been widely applied in construction, developers and contractors should keep an eye out for innovations here. 3-D printing will likely be an important part of the shift from the field to the factory. Experts believe that one core application of 3-D printing could be in realizing complex, iconic facades and architectural features previously thought too expensive or time consuming to produce.
3-D innovators are scaling up this technology, by developing printers and design methodologies to create building units up to 200 square meters in size in less than a day. Significant R&D efforts are also under way in universities to print individual structural components and architectural features.
Prepare for change
The construction industry is poised for big cultural and technological shifts as it embraces digitization across design and delivery processes. The real-estate industry is set to gain from these developments, not just as the result of efficiency and productivity gains but also by providing a richer and more satisfactory customer experience.
The larger benefits could be profound. By cutting costs, speeding up construction, and improving quality, industrialized delivery systems can also help provide the decent, affordable homes that families around the world need.