No industry is immune to the disruptions brought by digital technologies. While media, telecommunications, and banking have been among the first to feel the full brunt of these new technologies, manufacturing is now coming into the crosshairs. Globally, many manufacturers, especially those in advanced industries, have been looking for ways to exploit digital technologies. These efforts, generally dubbed “Industry 4.0,” are at a point where greater reliability and lower costs, largely attributable to improved storage and computing capacities, are fueling their rapid adoption over a variety of industry applications.
Industry 4.0 is the confluence of disruptive digital technologies that together carry the potential to change the manufacturing sector beyond recognition. The movement has gained critical momentum as a number of factors have come together: an astonishing rise in data volume, computing power, and connectivity; the emergence of advanced data-analytics and business-intelligence capabilities; new forms of human-machine interaction, such as touch interfaces and augmented-reality systems; and improvements in how digital outcomes are transferred to the physical world—for instance, through advanced robotics and 3-D printing.
Industry 4.0 is expected to drive productivity increases comparable to those generated by the introduction of the steam engine in the Industrial Revolution. Globally, it is expected to deliver between $1.2 trillion and $3.7 trillion in value (exhibit). The Association of Southeast Asian Nations (ASEAN), whose member economies have significant manufacturing components, has the potential to capture productivity gains worth $216 billion to $627 billion of this value.
In a recent McKinsey survey of more than 200 business leaders throughout ASEAN, the transformative potential of Industry 4.0 was clearly confirmed. Almost all of the respondents, 96 percent, believed Industry 4.0 will bring new business models to their industries and slightly less, 90 percent, said improved performance will be one of the main benefits from these new technologies. Additionally, in manufacturing-based economies like Indonesia, Thailand, and Vietnam, respondents were generally optimistic about prospects of Industry 4.0.
Would you like to learn more about our Operations Practice?
However, even as they acknowledged the potential of digital technologies, respondents showed slow adaptation. Only 13 percent said their companies had begun an Industry 4.0 transformation. ASEAN manufacturers cannot risk failing to capture the large opportunities made possible by these new technologies. By embracing Industry 4.0, ASEAN manufacturers can become the next leaders in their fields.
Despite the potential, few manufacturers truly appreciate the enormous long-term possibilities and implications of Industry 4.0 initiatives on their production systems. Too often, managers wrongfully dismiss Industry 4.0 as the latest buzzword. But, the technologies behind this trend will touch all aspects of the manufacturing process. And these technologies provide a clear opportunity for companies in ASEAN to improve their productivity and help the region reassert its status as a global manufacturing hub.
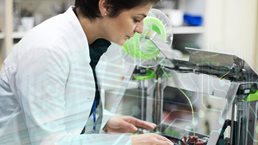
Industry 4.0 demystified—lean’s next level
Embracing Industry 4.0 technologies in ASEAN countries requires a clear understanding of the obstacles delaying its adoption, a shared vision of its potential benefits, and a policy and education environment that encourages implementation. Manufacturers in ASEAN may have had a slow start in the race toward these new technologies, but the marathon is young and there is ample track ahead to overtake the leaders.
Download the full report on which this article is based, Industry 4.0: Reinvigorating ASEAN manufacturing for the future (PDF–1MB).