As the COVID-19 pandemic sweeps across the globe, manufacturing organizations face significant operational challenges. Some companies have temporarily shuttered factories in response to government restrictions or falling demand, but others are facing significant increases in demand for essential supplies.
Frontline manufacturing staff can’t take their work to the relative safety of their homes. Plant leaders are therefore looking for ways to operate through the immediate crisis—all while preparing for a potentially much longer period of heightened uncertainty regarding demand and supply, and a lasting need to maintain enhanced hygiene and physical distancing.
Three areas of focus can help plant leaders navigate the transition from initial crisis response to the “next normal”:
- Protect the workforce: Formalize and standardize operating procedures, processes, and tools that help keep staff safe. Build workforce confidence through effective, two-way communication that responds to employees’ concerns through flexible adaptation.
- Manage risks to ensure business continuity: Anticipate potential changes and model the way the plant should react well ahead of the fluctuations to enable rapid, fact-based actions.
- Drive productivity at a distance: Continue to effectively manage performance at the plant while physical distancing and remote working policies remain in place.
Protect the workforce
The most critical focus for every organization is to keep employees safe in an environment where repeated outbreaks are a persistent threat. To achieve this, companies can deploy a comprehensive set of policies and guidelines, including enhanced hygiene measures, provision of additional personal protective equipment (PPE) where necessary, physical distancing, and modifications to existing governance and behaviors. Protecting employees’ mental health has also emerged as a high priority, with companies in China (and elsewhere) providing counseling services to employees returning after prolonged quarantines. These measures, developed in the initial response to the crisis, can be integrated into an organization’s standard procedures as it makes the transition to next-normal operations.
Communication is key
Ramping up internal communications is vitally important, including regular sharing of information about the company’s evolving knowledge of the crisis and how it is using that knowledge to protect employees and the organization. Clarity, simplicity, and framing all matter—research from earlier epidemics shows that positive messages focused on best practices were more effective than negative messages designed to address misinformation. Frequency counts as well, as audiences need to hear a message repeatedly before fully absorbing it. And that implies consistent content, reflecting a single source of truth at the corporate center.
Finally, the best communication is two-way, with managers answering questions and engaging in an open dialogue with employees at all levels. One equipment maker, for example, asks supervisors to collect queries and concerns from frontline team members every morning. The company’s HR department then publishes an updated daily list of questions and answers, which are displayed on monitors around the factory. After the introduction of the new policy, absenteeism among shop-floor staff dropped significantly and productivity returned to pre-crisis levels. As an additional, unintended benefit, the approach uncovered a number of frontline concerns unrelated to the pandemic, allowing managers to take additional steps to boost productivity and improve workforce satisfaction.
Plant leaders are already telling us that their frontline personnel appreciate the increased frequency and clarity of two-way communication necessitated by the outbreak. Organizations can capitalize on these improvements by standardizing their enhanced communication approach, rather than letting things regress to pre-crisis norms as the situation stabilizes.
Enabling workplace physical distancing
To keep staff safe over the longer term, companies can retain and formalize appropriate parts of their emergency-response guidelines, so they become part of plants’ standard operating procedures. Such guidelines might include enhanced health surveillance, restrictions on the use of communal tools and areas, regular sanitization of equipment along with periodic deep cleans of whole workplaces, and HR policies that ensure workers can stay at home if they feel unwell. Regulatory changes also merit extra attention, as governments introduce new rules on mandatory sick pay, or requirements for employees to limit contact with products or one another.
At the onset of the crisis, some companies began to ask employees to take a digital survey before starting on-site work, confirming that they do not have any COVID-19 symptoms, sharing their travel history since their last shift, and verifying they understand new health and safety guidelines. This approach provided valuable data that could aid contact tracing (where consistent with local practices) in the event of a positive test at the plant. It also helps to reinforce the importance of following health policies and reminds employees to avoid the risk of getting others sick.
Would you like to learn more about our Operations Practice?
Minimizing the potential future impact of infections will require companies to alter team structures and working methods in order to limit contact across the workforce. One way this can be done is by establishing “pods” for all on-site personnel, organized for self-contained teams with clearly defined tasks and workspaces that can be physically and socially separated from each other as much as possible.
Organizational changes to support the introduction of pods include dedicating workers to a single production line and removing “floating” workers—for example, by making pod members responsible for collecting materials and for conducting their own routine quality checks and maintenance. Shift handover meetings can be conducted remotely, using videoconferencing technology, while the start, stop, and break times of different pods can be staggered to minimize contact in communal areas of the plant. Plants may even choose to modify shift patterns, so lines in close proximity to one another are staffed and run at different times.
Exhibit 1 shows how the pod approach might work on a packaging line. Before the changes, operators working on the line were responsible for multiple machines, supported by logistics, quality, and utility personnel who worked across multiple lines. Under the pod system, operators are assigned to fewer machines but responsible for more tasks within their work area, thereby minimizing contact with staff and equipment outside the pod.
Instead of multiple employees handling each pallet, for example, a single team member is responsible for its entire journey. Some tasks, such as quality assurance, are now conducted by remote specialists, aided by cameras and digital tools. New physical barriers guard against accidental contact between pod workers, while allowing the unimpeded movement of product.
Manage risks to ensure business continuity
The coronavirus crisis has dramatically increased risk for every business, with many experiencing shocks in both supply and demand. Manufacturing plants are at the center of that uncertainty, and their continued operation through the crisis and beyond will depend in large part on the organization’s ability to navigate these wider risks. We have written elsewhere about the necessary steps to build resilience into the wider supply chain, and plant leaders will play a central role in their organization’s response.
Plant leaders can also plan their own response to risks that could directly affect operations in their facility—starting with what to do if an employee anywhere in the plant tests positive for a COVID-19 infection. Responses can include—but would not be limited to—consulting with health authorities, quarantining the affected person (together with any other staff who were working in close proximity), and isolating and sanitizing exposed products, tools, and workspaces.
Facing higher levels of uncertainty over the medium term, plants will likely find it useful to ramp up their scenario planning, with a higher planning cadence and a wider range of potential scenarios included in their analysis. When closely tied to the organization’s wider response and recovery strategy, this accelerated planning helps the plant develop strategies to accommodate substitute materials, or produce hard-to-source parts in-house.
Some companies are using digital twins of their facilities to simulate operation under different staffing levels and production scenarios. This approach can support many aspects of operational planning, from evaluating the impact of changes to plant layout to determining the mix of skills that on-site teams will require.
The transition to the next normal in manufacturing plants will require both leaders and frontline teams to develop new capabilities. The introduction of pods on the production line, for example, may call for operators with a wider range of skills, so they can complete all the tasks required in their pod or cover for absent colleagues.
New digital approaches can accelerate the capability-building process and allow employees to develop new skills remotely. Such techniques include the remote delivery of training using e-learning systems or the use of virtual-reality technologies to familiarize operators with new tasks or plant layouts. Augmented-reality systems help shop-floor staff to receive training, advice, and support from remote colleagues. Specialist contractors can use such systems to guide shop-floor staff through machine maintenance or troubleshooting.
Drive productivity at a distance
For as long as virus transmission among employees remains a risk, companies will naturally want to minimize unnecessary contact between personnel. Anybody not absolutely required on-site, including managers and many support functions, can be encouraged to work remotely as much as possible to protect the health of their shop-floor colleagues. To minimize the risk that an entire leadership cohort would need to enter quarantine at the same time, leadership staff who do need to stay on-site can be separated into at least two teams, with no physical contact between them.
As they reconfigure their operations to keep employees safe and respond to changes in the wider value chain, companies still need to maintain manufacturing performance. In many plants, leaders have long managed performance face to face, using daily shift briefings, visual management, and regular “gemba walks”—observant walk-throughs of the shop floor and wherever else the “real work” is being done. Physical-distancing and remote-working policies will make these established approaches more difficult, compelling companies to find new ways to manage shop-floor performance.
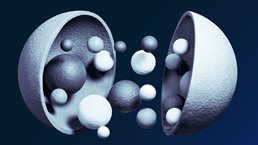
COVID-19: Implications for business
The technology necessary to support these changes doesn’t need to be expensive. Staff working off-site can use secure remote-access programs from their personal devices to handle shift handover meetings and similar activities. Some plants have equipped operators with two-way radios, assigning channels to specific teams or functional groups. This approach can actually increase the speed at which issues are communicated and resolved.
Now is a good time for companies to revisit the suites of metrics they use to track manufacturing performance. To make up for reduced in-person access to the shop floor, some factory-management teams are already beginning to identify and track leading key performance indicators (KPIs) in addition to the standard first- and second-level KPIs they usually rely upon.
Exhibit 2 illustrates this approach with a simplified cascade of KPIs from a high-speed production line. Each of the top-level performance KPIs on the left of the chart sits over a number of second-level KPIs that describe the major sources of losses experienced on the line. The leading KPIs in the third column track previously agreed-on actions designed to minimize those losses.
Monitoring how often frontline teams are cleaning, checking, and adjusting critical parts of the equipment—perhaps using sensors, if available—can give team leaders and plant managers a useful early warning of potential problems before they weaken operational performance. Historically, senior managers would rely on line leaders to review these activities in person, but with only remote monitoring possible, these data points can fill critical information gaps for managers. For example, if the number of times the infeed rails are cleaned starts to fall on a filler line, managers can follow up with the operators rather than wait for jams to reduce the line’s overall equipment effectiveness—the standard KPI that leadership teams usually follow.
Absenteeism rates are another important area of focus. Understandably, employees concerned about COVID-19 exposure could be reluctant to come to work, while others may be prevented from doing so by sickness or by quarantine rules. Some companies are proactively reaching out to employees the day before and the morning of their shifts to ask if they are planning to come to work, while others are offering hazard pay or soliciting volunteers to be “on call” for overtime, depending on vacancies. With advance notice of absenteeism and clear production priorities, plant teams stand a better chance of developing and executing efficient production plans.
Managers can use a skills matrix (Exhibit 3) to identify potential shortages of critical capabilities on a day-to-day tactical basis and, together with scenario modeling, guide decisions about staff training or recruitment requirements. Even a simple spreadsheet can quickly highlight problems and identify opportunities for reskilling or upskilling to improve workforce resilience.
In the longer term, the organization’s response to COVID-19 should accelerate the digital transformation that is already under way in many manufacturing environments. For teams working remotely or under physical-distancing guidelines, real-time data collection and advanced-analytics technologies can provide a more detailed, accurate, and up-to-date picture of plant operations.
Handheld cameras and smart glasses can give remote staff a virtual shop-floor presence, allowing them to assist frontline teams with troubleshooting tasks or even participate in gemba walks to support line supervisors and operators. Digital standard operating procedures (SOPs) and problem-solving guides can support frontline teams when managers or more experienced colleagues are not on hand. Online learning technologies can help staff develop new skills quickly, creating a more flexible, more technology-savvy workforce at every level of the organization (Exhibit 4).
The next normal is also likely to drive a change in the metrics and targets companies use to optimize manufacturing performance. Management systems that typically emphasize productivity and quality will expand to include a greater focus on flexibility (for example, the number of staff cross-trained to perform multiple tasks on the line) and resilience (the number of component shortages due to supply-chain or quality issues, or the skills that are in short supply because only a small number of employees have the necessary training or experience). Companies can reinforce those changes by adjusting targets and incentives for individual employees, such as by emphasizing adherence to health and safety guidelines. Staff could be rewarded for developing broader skill sets, reducing reliance on external contractors and increasing the overall resilience of the workforce.
The coronavirus will have long-lasting—perhaps permanent—effects on manufacturing organizations, forcing companies to restructure their operations to maintain production while protecting their workers. The coming weeks and months will remain extremely challenging for plant leaders, but the crisis also creates an opportunity to reimagine the way work is done. By accelerating the adoption of new digital technologies and by drawing on the flexibility and creativity of their frontline staff, companies have the opportunity to emerge from the crisis with manufacturing operations that are safer, more productive, and more resilient.