While the word “automation” may conjure images of robots taking over jobs, the reality is much more nuanced. In construction, for instance, automation is less likely to diminish employment opportunities than it is to increase productivity. Indeed, automation—alongside the global need for new and updated infrastructure and better and more affordable housing—can help shape the direction of the industry. The key will be anticipating and preparing for the shift, in part by developing new skills in the current and future workforce.
Stay current on your favorite topics
Big picture: What does automation mean for construction?
In years past, productivity in construction increased slowly at best.1 In the United States, for instance, from 1947 to 2010, productivity in construction barely changed at all. Meanwhile, productivity increased by more than a factor of eight in manufacturing and by more than a factor of 16 in agriculture2—both industries that have embraced automation. So, one major benefit of automation in construction is the potential for quite a large uptick in productivity.
There are three primary opportunities for automation in construction. The first is automation of what are considered traditional physical tasks on-site—for instance, robots laying bricks and machines paving roads. The second opportunity comes from the automation of modular construction—or rather production—in factories, including 3-D printing of components such as facades. And the third centers on digitization and the subsequent automation of design, planning, and management procedures, as well as the vast efficiencies those can create on-site. For example, building information modeling—which essentially brings together the designs of planners and general contractors to identify issues before they move to the site—makes the planning process more efficient. But more importantly, it makes the on-site execution more efficient, allowing project teams to eliminate mistakes and better coordinate the workforce.
Would you like to learn more about our Capital Projects & Infrastructure Practice?
What impact will automation have on work for builders?
A substantial shift to modular construction off-site could have a significant impact on the construction workforce, but the transition will take decades. Producing individual components, or modules, in factories lends itself to much more machine use than what can be done on-site. Some companies, such as Katerra, are already building such modules. A lot of the construction in these factories is still done manually, but over time, as scale increases, the process will become more automated. We estimate that about 15 to 20 percent of new building construction will be modular in the United States and Europe by 2030. So, while it’s an increasing share and a big market, it’s a slow process, and a lot of activities will remain on-site and relatively unpredictable for some time to come.
For those activities that do remain on-site, it’s unlikely that a company will fire a carpenter and bring in the latest robot to do everything the carpenter did. Rather, machines will take over individual activities within a role. What that means is workers will need to learn to work side by side—or in a hybrid role—with machines. For example, even the average construction worker will be expected to use a tablet to access building plans or operate a drone in place of doing a physical site walkthrough.
Will there be enough work in the future?
While there are substantial automation opportunities across industries, employment in construction will probably suffer less than in industries where activities are more repetitive, such as manufacturing. The easiest tasks to automate are repetitive, physical activities in predictable environments—but construction’s environment is usually unpredictable, except when modular-construction techniques are used. The unpredictability is twofold: not only do pieces move around but each construction site and project is tailored to specific customer demands, architectural designs, and geographical and site requirements.
We expect the overall number of jobs in construction to grow rather than shrink, with up to 200 million additional jobs by 2030 if countries fill global infrastructure gaps and boost affordable housing supply.3 Automating more of the construction process could also help deliver infrastructure and buildings faster—without needing to reduce headcount. Furthermore, there is a substantial need for infrastructure and housing in parts of Asia and Africa. This means there will be demand for construction work—and workers—for a long time to come.
Any slowdown in global growth, which would lower demand for infrastructure investment, might counter some of that upside. But, generally, there is—and we expect there to continue to be—enough work to do.
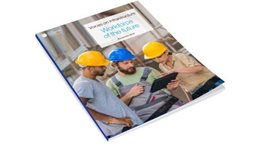
Voices on Infrastructure: Workforce of the future
How will automation affect construction wages?
Despite everyone having enough work to do, we expect a larger spread in wages. In the long term, automation is likely to increase productivity and allow wages to rise for workers with advanced skills. At least during the transition time—which can take a decade or longer—those with advanced skills will command higher wages because they will be in higher demand, while those more exposed to predictable, repetitive tasks will be in less demand and may see a slowdown in their wage growth.
Overall, construction jobs tend to be in the middle-wage range, at least in the United States, and are not straightforward to automate. Therefore, the industry might contribute to filling in what otherwise looks likely to be a continued hollowing out of the middle class.
How can the industry manage the upcoming workforce skills transition?
As in all industries, automation will create an increasing skill mismatch in construction. Workers will still need a fair amount of physical skills: even if robots do the physical work of laying bricks, workers will still need to drive and maneuver heavy equipment. But they will need to pair this work with more technological skills.
But where will they acquire those skills? Adjusting to automation in construction will require efforts from the public sector, the private sector, and industry associations to support workers in developing the skills to make the transition.
Historically, the public sector has had a predominant role in supplying baseline education and skills, and it will likely continue to do so. But curricula must shift to meet current and future needs, particularly for technological and socioemotional skills. There will also be a growing need to reskill and upskill workers who left formal schooling decades ago, requiring an evolution of the education system to provide lifelong learning opportunities.
The private sector, meanwhile, has a responsibility to address the more specialized skills needs of the workforce—and across sectors, a majority of executives recognize they have a strong role to play.4 But historically, construction has invested much less than other industries do in employees’ skills. This is partially a result of the predominance of subcontractors and high shares of temporary labor. But as all firms face the same skills shift, it will become increasingly difficult to find qualified people on the market. Institutions must preempt the need and provide access to skill-development opportunities, investing in their current workforce so they are prepared for the job ahead.
Finally, collaborative efforts also abound. For instance, Germany’s Technical University of Munich organizes a platform of industry players that trains participants in digital construction through boot camps, hackathons, immersion days, and peer exchanges. In the United Kingdom, Homes England, a nondepartmental government body, is working to launch a research program on modular construction that will monitor and report on a couple dozen sites. The goal is to compare these projects with traditional build approaches, thus providing the industry with data on emerging technologies.5
The outlook for automation in construction is bright. That’s not to say there won’t be work to do across industries to prepare the workforce for shifting needs. But overall the industry will likely improve its productivity, see an increase in wages, and be better suited to meet the growing demand for infrastructure and real estate.