The global mining industry, both underground and open-pit, is struggling to raise its asset productivity. Data from MineLens, McKinsey’s proprietary analysis tool, shows that mining productivity fell by one-third between 2004 and 2009, even after controlling for external factors like site age and geological degradation.
Since then, mining operations have evolved significantly, with companies investing in fleet-management tools and other technologies that allow them to collect more data and gain new insights into the drivers of operational performance. So far, however, these insights have not translated into significant productivity improvements for all players. Productivity has risen only modestly since the beginning of the current decade (Exhibit 1). What is holding these companies back from capitalizing on new innovations?
There’s evidence that some mining companies have paid less attention to the human side of their operations. For example, in another McKinsey benchmark, the Organizational Health Index (OHI), one company in the sector dropped from the third to the fourth quartile between 2013 and 2016.
Could it be that organizational health—which is a result of the mindsets and behaviors of a company’s personnel—is the missing link that would turn the technical advances made over the past few years into a productivity recovery?
Stay current on your favorite topics
Healthier, safer, more productive
The link between organizational health and performance is well-established. Healthier companies deliver a higher return to shareholders, and recently completed research on energy and materials companies suggests that OHI results are also linked to safety performance. The mechanisms that link health and performance are complex, however, making it difficult to pin down simple cause-and-effect relationships.
The mining industry provides a unique opportunity to explore those relationships in detail. The MineLens benchmark database now includes detailed operational data from more than 250 mine sites around the world, and 20 of those sites also participated in the OHI at around the same time. By combining the two data sets, we can see for the first time how “hard” operational performance indicators vary between sites that perform differently in measures of organizational health.
The indicators we chose were truck availability—a measure of maintenance performance—and truck utilized equipment effectiveness (UEE), a measure that combines maintenance effectiveness with operational performance. The productivity of truck operations is particularly important at many mine sites, where material hauling can be a production bottleneck with a major effect on cost.
Would you like to learn more about our Operations Practice?
Comparing standardized truck availability and UEE scores with health metrics revealed a number of significant relationships, which together suggest that how companies manage their people changes the way those people manage their equipment and, ultimately, the productivity of those assets. Healthy mining organizations, it seems, maintain and use their assets more effectively than their unhealthy peers. Notably, the relationship is non-linear: it isn’t until companies achieve top quartile scores in the OHI that operational performance benefits become apparent.
Specifically, companies that with scores in the top quartile of the OHI had truck availability that was 8 percent higher than companies in the bottom quartile, and 6 percent higher than average OHI performers (Exhibit 2). For mines where hauling is a bottleneck, that 8 percent difference could translate into a production increase of around 5 percent, or a decrease in operations costs of about 2 percent.
When we dug deeper into the OHI data, we found a handful of drivers that seem to have particularly strong relationships with operational performance. The OHI benchmark measures both “practices,” which are actions companies put in place to improve their health, and “outcomes,” or attributes of employee mind-sets and culture that healthy organizations exhibit. We found relationships to operational performance in both sets of measures. For instance, companies that achieved top quartile results in “Accountability” and “Operational discipline” achieved 16 percent higher UEE than those in the bottom quartile (Exhibit 3).
Other significant attributes from the OHI survey included motivation (defined in the survey as a company’s ability to “develop employee loyalty and enthusiasm, and inspire people to exert extraordinary effort to perform at their very best”) and consultative leadership (“involve and empower employees through communication, consultation and delegation”). Companies that achieved top-quartile scores in consultative leadership achieved 9 percent higher truck availability than those in the bottom quartile.
Engage your employees
These findings confirm our view that organizational health is linked to strong operational performance. More intriguingly, they shine a light on the specific factors that appear to be helping healthy organizations achieve higher operational performance than their competitors.
Most of those factors are related to employee engagement. For example, maintainers are more motivated in an accountable work environment. For example: “I have a clear understanding of my role, I know what is expected of me, results are transparent, and I know what happens if I deliver, or not.” Similarly, staff respond well when they experience styles of leadership that are both consultative (the leader asks how the maintainer will solve a problem) and supportive (the leader asks what help the maintainer needs).
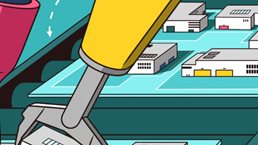
Optimizing production in the age of the machine
Describing the approach adopted at his organization, mining company provides a compelling illustration of the link between management approach and operational performance.
“The maintenance personnel I work with are very experienced people who know how to do their jobs. I see my role as helping bring a systematic approach to maintenance that ensures a high level of consistency and discipline in execution through coaching and guidance, not orders. I am there to empower my team by helping remove roadblocks, gathering the necessary resources, and providing timely input when needed; not by telling people what to do.”
The maintenance group, he continues, strives to create a “client service” culture, where maintainers see themselves as accountable to their manager, to production and to the owners of the business.
“The one idea I aim to communicate to my maintenance group every day is that we need to demonstrate to our customers (operations) that we are maintenance professionals. That comes from taking our work, and each other, seriously, no matter what member of the team. That way when we put in a recommendation, it’s respected and followed because we are confident with our plans and credible in the eyes of operations.”
A recent failure in a critical plant asset provides a telling example of the impact of that credibility. With the next scheduled shutdown still six months away, the maintenance team had to make a difficult decision: continue to patch up the equipment until then or stop production to do the complete repair. Convinced that the full repair was in the best interest of overall site performance, the maintenance team approached the site general manager to request the production stop. “Our credibility gave the GM confidence to support our plan, which allowed us to make what I believe was the best business decision and meant a lot to us as a maintenance group,” the manager says.
Our analysis suggests that the way maintenance and operations managers lead has an influence on the productivity of mining assets. And contrary to popular belief, getting the most out of your assets isn’t all about discipline and authority; it’s also about engaging those who operate and maintain them.
The key takeaway for operations leaders: the health of your organization affects the health of your assets, which means it should be part and parcel of every major operational improvement initiative.