It’s not a stretch to say that safety in the energy sector is of paramount importance. Workers in this industry are exposed to a range of potential hazards at different stages of production—whether they’re on the electric lines, using heavy equipment, or working around flammable gases. In an environment that can place workers at risk, it’s imperative to ensure that safety is not just about rules and preventative measures—it’s also a foundational value that is deeply embedded in an organization’s culture.
When safety is relegated to a check-the-box exercise, companies are more likely to experience stagnant or incremental safety improvements. Organizations that approach safety as a cultural value and a commitment to their people and their work can promote meaningful change that everyone across the organization can and should be a part of. To embed safety in the corporate culture, companies must engage stakeholders across the board, from employees to executive leadership, through open dialogue.
Major global oil and gas player Total sought to become recognized as a benchmark for safety in the energy industry. In 2014, company leadership tasked Bernadette Spinoy—then senior vice president of health, safety, and environment (HSE)—with leading a safety culture transformation, the goal of which was achieving zero fatalities. In this interview with McKinsey, Spinoy discusses how Total launched its innovative transformation program focused on safety culture.
McKinsey: What were the objectives of the safety transformation program?
Bernadette Spinoy: We had two main objectives: to ensure that all employees and contractors get home safely and to prevent the occurrence of major accidents by managing major risks.
To support these efforts, we began accelerating our path to achieve zero fatalities and reducing workplace accidents from 1.0 recordable injury per 1.0 million hours to less than 0.9 accidents per million hours.
McKinsey: How did you structure the program to support those goals, and how did you gain internal alignment?
Bernadette Spinoy: We began by interviewing leading industry players to get their perspectives on major safety challenges. These conversations helped narrow the focus of our efforts to three areas: technical reliability, management methods, and cultural factors.
To support our program, we created a working group that included both business-unit leaders and senior HSE management. We then asked the group for suggestions on how to improve safety within those three areas. Within a few months, the working group generated about 50 proposed initiatives to improve safety. The executive committee at Total selected and immediately implemented 20 of them, such as text-message alerts to leaders whenever an incident happens.
At the end of 2014, we rolled out a series of visible actions to create momentum and get people on board. When an accident with significant consequences happened in one of our departments, we made sure to address it immediately at multiple levels within the organization. First, all senior leaders would receive a text message with a description of what happened in the hours following the accident. Next, the description would be published on the company’s intranet and made available to everyone. We would also circulate a video within the company that gave an overview of all fatal accidents that occurred from 2013 to 2014. These collective-awareness efforts created momentum to reach our accident reduction goal and created an ongoing conversation around safety.
McKinsey: Which initiatives have had the greatest impact in improving safety?
Bernadette Spinoy: First, we realized the importance of influential human factors—the underlying reasons why someone makes a mistake—so we shifted our focus to learning and development when it comes to safety. For example, in incident analysis, we used to focus on the technical causes or simple failure of workers to follow rules. But we began to focus on understanding the organizational and personal context and how this relates to the occurrence of events. This shift in focus was a real challenge to overcome.
In response to our findings, we set up a specialist HSE team that could move in quickly following each incident and analyze these human and organizational factors to understand why a mistake was made. For example, someone might make a mistake while attempting to do the right thing, but someone might also cause an accident by willfully not following rules. We remain attentive to those near-misses, or “free” lessons, that allow us to learn more through in-depth analysis.
Personal liability is another important consideration in this learning process. How can we make sure people are comfortable talking openly about safety and accidents and yet still enforce necessary rules? We opted to separate the analysis of the causes from the consequences, which may involve sanctions. Now, obvious or repetitive cases are penalized, but overall, we prefer to focus on learning. We encourage individuals involved in an incident to record videos explaining their experiences and what they learned from them.
Creating an encouraging safety culture that emphasizes positive reinforcement for good, safety-oriented behaviors is another critical aspect of our transformation program. We’ve created a reward system whereby anyone in the office can nominate a colleague to be praised for safety. On average, we aim to distribute eight to ten rewards for every one sanction. Employees get visibility on the intranet for their safety initiative, congratulated by their leaders, or even a trophy or small prize.
Previously we were not as good at rewarding employees—it was done sporadically. So it made sense to introduce something more systematic. It is not easy, and we can still improve. For our Safety Day 2018, we focused on the theme of rewards and brought everyone together on site to talk about safety. We invited subcontractors, and the group’s managers were also present.
We also ensure that operational colleagues “own” their safety performance. For instance, local subsidiaries and sites are free to launch their own initiatives in line with one of our six HSE group road map themes.
Since 2016, safety has become a corporate value—the safety of our employees has always been a top priority at Total, but elevating safety to become part of the corporate culture sent an even stronger message from the top. By evolving from priority to value, safety has grown from something we were doing to a way of doing things. Today, safety permeates everything we do.
McKinsey: What role did the HSE department play in the overall safety program?
Bernadette Spinoy: We integrated our HSE function at the group level by bringing together HSE departments from across different divisions of the company’s four businesses.1 This new consolidated HSE function created a unique road map, bringing together each branch’s strengths and expertise for our safety program. The plan consists of the best suggestions from our working group and from each of those divisions, and it was adopted throughout the company.
The group road map is structured around six areas: prevention; integration involving the whole operating line; piloting—that is, leadership that includes role modeling, commitment, and rewards; learning by developing a learning organization and taking audits into account; cooperation by sharing and communicating with each other and outside firms, such as contractors; and unification—being stronger and more innovative together. Local subsidiaries were asked to ensure that their safety initiatives aligned with these areas. We believed that, to make progress, we had to clarify our vision and way forward rather than launching many initiatives without a clear framework.
McKinsey: How did you ensure a large-scale—and lasting—impact throughout the organization?
Bernadette Spinoy: It all started with the involvement from the top, and our CEO’s role was essential. Managers set the example and walk the talk—this is critical if we want our safety culture to permeate the organization. We also asked our leadership team to recognize good practices, positive results, and initiatives coming from their employees. Our goal was to experience safety as a value and create a company culture where people feel good about safety and have confidence in the organization.
We also support an open dialogue on safety between our top management and our contractors. Our contractors are required to have the same attitude toward safety as our employees. Once again, it is about setting an example. For instance, we introduced the “Stop Card,” which allows contractors to stop working as soon as they perceive a hazard. By flashing the card, they can stop a potentially dangerous situation and begin a conversation with the involved parties, regardless of their level in the organization, to resolve the issue. The same tool is used by our own employees. In 2018, our contractors achieved the same level of injury rate as our employees. We also refined what we call the 12 Golden Rules,2 with “dos” and “don’ts” to make them clearer and more easily implemented across the organization.
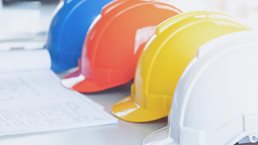
Overcoming limiting mind-sets to improve safety
Our subsidiaries with the best safety results are the top performers as measured by quality and cost management. We benchmark their performance on a regular basis. We also conduct employee satisfaction surveys every other year and distribute the results across the organization so managers can understand what’s happening on the front line and address issues if needed.
McKinsey: What role does HSE training play in building a strong safety foundation?
Bernadette Spinoy: All newcomers, regardless of their position, are trained in safety on day one, and these courses are led by the newcomers’ direct-line managers. The content of the courses varies depending on the position, geography, and function of new employees. The sessions can last from one to 15 days. This proactive approach helps us immerse employees in our safety culture from the start.
After the initial training, we have courses specific to each person’s role. Managers have mandatory training every two years, and operational employees receive training according to their work needs. At each level of training, we want people to talk about safety and about our culture through discussions and case studies.
McKinsey: How can companies recognize a good safety culture? What form does it take?
Bernadette Spinoy: At Total, every formal meeting starts with a safety moment: a one-minute contribution in which someone talks about safety or shares a thought or personal testimony. We also do regular on-site safety walks with everyone at every level of the company. These shared rituals help to spread safety thinking throughout the organization and incorporate it into shared beliefs and a shared mind-set.
People must believe that business performance and safety performance are inseparable. These objectives are based on the same managing principles and can be translated as excellence in operations. Everyone has a role to play, and everyone can help prevent accidents. It takes a collective body of knowledge as well as individual efforts to resolve issues.
We believe that success requires a certain set of behaviors—vigilance, attention to detail, and rigor. It is about having a collective mind-set at all levels and at all times: What is your behavior when no one is watching?
We must stand firm and believe that together, when everyone embraces the safety culture, we can achieve our goals. Yet we must also stay humble; achieving safety results is a never-ending journey.