With most of the world committed to limiting global warming to 1.5°C, many companies have set individual decarbonization targets for 2030 and even 2025. As we approach the end of 2023, we have only six years left to implement many decarbonization levers. But industrial companies are often uncertain about the right technical path to immediately reduce emissions. Technologies that are net present value (NPV) positive and quick to implement, such as various types of energy efficiency measures, can help companies achieve their decarbonization goals.
Recovering waste heat is a potential avenue to effectively reducing emissions. Every year, the world consumes over 418 exajoules (EJ)—or 116,000 terawatt-hours (TWh)—of final energy, mainly by burning fossil fuels and generating heat.1 Part of this generated heat is harnessed for useful purposes, such as producing electricity or driving chemical reactions, but most is unused. This unused “waste heat” is given off to the surrounding environment in the form of exhausts or effluents at different temperature levels. Recovering this waste heat can greatly reduce the use of primary fuels and, therefore, emissions.
Recovered waste heat could also make the energy transition easier and more economical. Recovered heat can be used for industrial process heating purposes, city grid heating, or converted to electricity (determined by local energy demand patterns as well as prices of fuels and electricity). Depending on whether waste heat is used for heat or electricity, the annual global saving could reach up to €140 billion—comparable to the worth of all natural gas imported by the European Union (Exhibit 1).2
While waste heat has been used in industrial companies for decades (to generate electricity through steam turbines or to provide process heating, for example), this potential remains largely untapped. Despite the benefits and possibilities of waste heat recovery, at least 3,100 thermal terawatt-hours (TWhth) of feasible waste heat is currently not being captured (Exhibit 2).
In this article, we explore how the stage has been set to access waste heat recovery across sectors, and what industrial companies can do to grasp this opportunity.
Would you like to learn more about our Sustainability Practice?
Technological advancements and price developments unlock the potential of waste heat
Over the past decade, gas, electricity, and CO2 prices have been low, and there has been limited incentive to push waste heat recovery to the limits. For one, the payback time of waste heat recovery was long, and industry would typically only consider projects with a payback within one to two years. And, importantly, there wasn’t immediate pressure to act on decarbonization targets to drive action in waste heat recovery, so companies deprioritized energy efficiency in favor of projects with much higher returns. For example, it was financially more attractive to build another production line and burn more gas to run it than to save energy on an existing line—especially if companies were constrained in terms of capital expenditure (capex).
Historically, industry was focused on heat cascading (reusing heat) as the cheapest and simplest option of heat delivery (Exhibit 3). Heat pumps were expensive and not capable of delivering temperatures above 100°C, and conversion of low-grade heat into electricity did not make economic sense when energy prices were low. But times have changed: both in terms of technological developments and incentives.
New developments in recent years can now use high-temperature heat pumps or chemical technologies to increase the temperature of waste heat and generate low- and medium-pressure steam. Heat-to-power technologies have advanced too, such as an organic Rankine cycle (ORC) that can recover waste heat from lower temperature sources and convert it into electricity more affordably. Much of the reduction in the cost of waste heat recovery is due to the modularization of equipment and standardization of design, with further reductions when technologies scale up.3
In the buildings sector, better insulation and the combination of floor heating or heat pumps, or both, have led to lower temperature city grid heating. New, fifth-generation, district heating systems work well with low temperatures of about 40°C (compared to older systems that required higher temperatures closer to 100°C).4 Since industry has a lot of heat available at 40°C and above, industrial waste heat is well suited to be a heat source for district heating.5
At the same time, energy prices have soared. For example, in Europe, electricity prices ranged between €25 and €80 per megawatt-hour (MWh) in 2018 and 2019, but prices are often now above €100 to €150. Similarly, gas prices have doubled since 2018 to between €20 and €40 per thermal megawatt-hour (MWhth), and CO2 has seen a five to ten times increase to reach around €100 per tonne (or €20 per MWhth of natural gas consumed). The economics are now generally more favorable for heat pumps, as heat pumps (which are electrically driven) thrive when heat is expensive.6
Waste heat recapture presents attractive savings opportunities in industries
Heat has become expensive for much of the world—and it does not appear likely that it will become cheap again, at least in the short term. The combination of technology and price developments makes waste heat recovery an opportunity for industrial companies, like refineries and cement manufacturers, to gain a competitive edge.
For example, a refinery can employ heat recovery from stripper overhead condensers from various units, such as vacuum gas oil (VGO) hydrotreaters or diesel hydrotreaters. These sources would usually have temperature ranges of 120°C to 250°C, and duty of five to 25 MWth for a typical refinery. If that heat was used to make medium pressure steam at five barg, then an average ten MW duty equipment would get about seven to eight tonnes of steam per hour—worth anywhere between €0.8 million and €3.5 million per year (Exhibit 4).
Sectors that have a limited need for low- or medium-pressure steam may not have a good use of waste heat energy for heat purposes and could instead feed the heat back into district heating. Alternatively, some sectors may still have a need for electricity, such as the cement industry, and could recover the heat for electricity savings. For instance, in cement, there is typically 120 thermal kilowatt-hours per tonne (kWhth/t) of recoverable waste heat available from a preheater tower and 100 kWhth/t from a clinker cooler.7 If that energy was recovered by an ORC system for a one million tonnes per annum (MTPA) plant at 10 percent efficiency, there would be an annual electricity savings of around 22 GWh—worth between €0.7 million to €3.1 million.
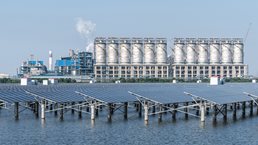
Outsprinting the energy crisis
Waste heat recovery options consistently yield a positive net present value, regardless of the sector
Waste heat recovery is not limited to cement or refining—virtually any industry would find some heat that can be recovered. Exhibit 5 shows a typical industrial abatement curve with options for emission reduction.
The NPV-positive options on the left-hand side of the curve, which often make up 10 to 30 percent of the total abatement potential, are almost exclusively from energy efficiency initiatives (typically various heat recovery options). These options require minimal effort and can be implemented quickly (although payback is often still too long to be accepted by industry). They can be categorized in three segments:
Incremental improvements, such as adding a heat exchanger or installing and optimizing advances process controls.
Novel technologies, including heat pumps, mechanical vapor recompression, Q-pinch, thermal energy storage, direct electrification, and waste heat to power.
Process redesign, such as a set point change, additional reboiler, dryer redesign, new reactor design to recover waste heat instead of cooling, and the replacement of condensing turbines by electrical drives.
Three ways to capture the untapped potential
To fully realize the potential of waste heat recovery, industrial companies can extend the scope beyond a single plant and encompass the entire site, crossing business units and company boundaries. This requires going past the standard list of levers, such as adding a heat exchanger, and delving deeper into the process, challenging all preconceived notions. There are three actions industrial companies can take to capture waste heat recovery potential.
- Develop and implement a comprehensive waste heat recovery program that includes regular monitoring and evaluation of the program's effectiveness. This program can also include ongoing training and education for employees to ensure they are aware of the benefits of waste heat recovery and how to implement it effectively.
- Assess advanced heat recovery technologies and explore opportunities for heat integration at the plant and site levels. Partnering with industry experts, utility companies, and technology providers can help ensure companies are using the most advanced and effective waste heat recovery technologies and strategies.
- Explore new business models; for example, energy-as-a-service model, where customers pay for an energy service (such as waste heat recovery) without making an upfront capital investment. Instead, the energy service company provides access to the equipment and service in exchange for an agreed fee or through a savings-sharing agreement.
As the world strives toward net zero, companies are setting decarbonization goals and implementing technologies like waste heat recovery to reduce emissions, support the energy transition, and reap economic rewards.
As surging energy prices bolster the need for waste heat recovery, and technological developments open the door, now is the time for industrial companies to capture the potential of waste heat recovery and stay competitive.