The COVID-19 crisis couldn’t have come at a worse time for Second Harvest Heartland, Minnesota’s largest food bank.
When the virus first began to spread in the state, Second Harvest Heartland was weeks away from moving into a new warehouse in suburban Minneapolis. In anticipation of the move, the food bank had purposely drawn down its inventory, so there wouldn’t be as much to haul from one place to another.
Demand exploded virtually overnight. As the virus spread, businesses closed, and workers were furloughed or laid off. The number of people in danger of not having enough to eat spiked. At the same time, food donations from local wholesalers dried up, as those businesses experienced the same virus-induced supply-chain disruptions that cleared grocery stores of essentials like toilet paper, disinfectants, and soup. When restaurants closed to comply with mandatory shutdowns, it cut into the supply of food that Second Harvest Heartland normally could expect to rescue. Recognizing the public health risks to themselves and others, many volunteers reduced hours or stopped showing up to the nearly 350 food pantries, shelters, and soup kitchens that Second Harvest Heartland partners with. Moreover, as a precautionary measure, the food bank now had to pre-assemble food boxes before distributing to partners, adding time and cost.
As a stop-gap measure, Second Harvest Heartland dipped into donated funds to pay for the boxes and other food. But the food bank couldn’t afford to do that for long without serious financial consequences. With the crisis showing no sign of stopping, the food bank’s operations and inventory management leaders had to figure out how many more people might need help, and for how long, in order to calculate how much food was required and where to get it.
For that, they turned to data.
We developed a way to communicate about what was coming our way that created a calmness and confidence that we could do it.
Food banks such as Second Harvest Heartland have traditionally been supply-focused, distributing whatever food they are given. Forecasting tended to be limited to yearly reviews using historical, backward-facing data. The COVID-19 crisis changed that. By necessity, food banks needed to act more strategically to identify the specific requirements of the communities they serve—and to use data analytics to take guesswork out of the equation.
For Second Harvest Heartland, digging into the data revealed a potentially disastrous shortfall. In a worst-case scenario, the food bank would need 26 million more pounds of food than it normally distributes in a year, according to Julie Vanhove, Second Harvest Heartland’s supply and demand planning director.
Fortunately, the need has not yet reached that point. But by developing a plan backed by data for this worst-case scenario, the team felt reassured. “We developed a way to communicate about what was coming our way that created a calmness and confidence that we could do it,” said Thierry Ibri, the food bank’s chief operations and programs officer.
Turning to data
The COVID-19 crisis has forced food banks to address other challenges. Some have upgraded warehouse practices to manage a substantial increase in food supplies. Others have improved planning by segmenting food sources and distribution channels by type. Some have begun to work with new community partners to tackle the root problems that contribute to food insecurity, including housing, healthcare, and job skills.
The changes come as food banks grapple with assisting up to 54 million Americans in danger of being food insecure and not having enough to eat.
Better data are at the heart of many new processes. Food banks’ operations have always depended on data to track how much food is donated, purchased, and received through government programs; or rescued from restaurants, coffee shops, and grocery stores. Food banks also use data to calculate how many food boxes or supplies for meal programs need to go out.
But because COVID-19 created an unprecedented surge in demand, food banks couldn’t depend solely on what they did in the past to calculate future needs. For that, they had to take planning to the next level. That was the situation for Second Harvest Heartland. Based on the flurry of requests when the pandemic hit, it became clear that “historical data weren’t going to provide an accurate forecast of what was coming,” Ibri said.
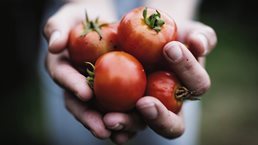
Food security
Second Harvest Heartland needed better insights into the needs of its service area, which includes 41 counties in Minnesota and 18 more across the state line in western Wisconsin. Since the crisis, an additional 275,000 Minnesotans—including 112,000 children—became at risk of going hungry, an increase of nearly 60 percent from 2019, according to Second Harvest Heartland’s estimates. At the same time, the food bank needed to adopt procedures to avoid a virus breakout at its new 230,000-square-foot warehouse in Brooklyn Park, north of Minneapolis. “With 75 percent of the food distributed by food pantries in our service area coming from us, it would have been disastrous to shut down,” Ibri said.
Second Harvest Heartland partnered with McKinsey to develop a demand model to forecast the supply that it would need, based on various scenarios of future demand. One critical component of the model was a formula developed by Feeding America, a non-profit network of 200 US food banks including Second Harvest Heartland, and 60,000 partner food pantries and meal programs. The Feeding America formula maps the connection between food insecurity and variables, like poverty and unemployment.
The food bank project team combined information from the Feeding America formula with projections from Oxford Economics for how the COVID-19 crisis could affect unemployment and poverty in the region. This allowed the team to come up with best-case and worst-case scenarios for how food demand could vary from May to December for each county in their service area (Exhibit 1).
Planning for the worst
The model helped Second Harvest Heartland’s staff to determine that demand could increase 30 percent to 66 percent by the end of the year, depending on the effect of the crisis on the state’s economy, but likely peaking in early fall when federal relief funds were due to run out. If the worst-case scenario came to pass, the food bank would need 91 million pounds of food to meet the projected need for the year—26 million pounds more than usual, or the equivalent of roughly 31.2 million meals.
Armed with that information, the food bank’s leadership secured additional state funds, which they used to purchase food and increase orders from local growers. In turn, that helped offset the decline in donated goods. Vanhove, who handles purchasing, said having more accurate forecasts gave her the confidence to take delivery of large orders—such as buying “a third truckload of corn”—that might have seemed questionable without such visibility.
Having concrete data also provided information the food bank could share with staff to show how well things were going, and for the food bank’s fundraising team to show prospective donors. “It gave them a script to go out and talk to donors with some certainty about the food that we would need and why we were asking for money,” noted Ibri.
The reaction from food pantries and the public has been unanimously positive. “We received really good feedback about our ability to respond to and evolve as needs arose,” Vanhove said.
Since April, Second Harvest Heartland has updated the forecasting model every month, and adjusted planning based on how the virus and the economy are playing out. As of late September, the food bank’s estimates show demand running about 30 percent higher than average (Exhibit 2). “The good news is the model is month by month, so we didn’t have to source 26 million pounds of food,” she said. “We could ratchet down the plan to be in sync and have the supply plan match the demand.”
Forecasting models for other purposes
A beneficial byproduct of developing the model was getting a better read on the amount of inventory coming in and going out of Second Harvest Heartland’s new warehouse. The food bank also used it to inform staffing and warehouse capacity—and not a moment too soon. “The warehouse we just built and moved into was supposed to cover us for ten years. But by July, it was already at 95 percent capacity,” Vanhove said.
The application also shows where the agency might run into bottlenecks with refrigerator, freezer, and dry-storage space. This information is now being collected to develop future capacity-planning forecasts, she said.
Second Harvest Heartland doesn’t expect to use the COVID-19 forecasting model beyond next year. But it may serve as the basis for other planning models that the food bank’s supply- and demand-planning staff expect to create in the future. “It informed us of what a dashboard would look like, and what the components are that we should look at from a planning perspective,” Vanhove said.
Based on the food bank’s experience, it’s clear that using data-driven models can make a difference. It’s also clear that modeling works best when leaders are willing to embrace it and trade instinct for evidence, and use the data they collect to implement new decision-making processes that inform supply-chain planning from sourcing to delivery.