Globally, the demand for BEVs is strong, prompting fierce competition among many companies for cost and technology leadership. If they can improve battery cells and packs, which account for up to 35 to 50 percent of vehicle cost, they could significantly increase potential profits.
This article examines the Chinese battery market, taking a closer look at cell chemistry, cell design, and battery packs to help market players understand the recent developments and emerging opportunities.
The Chinese BEV battery-pack market
The Chinese BEV market has been growing by about 80 percent annually since 2014. It’s still the world’s largest market, accounting for 1.1 million BEV sales in 2020, compared with 800,000 in Europe. China’s global market share has dipped from 57 percent in 2019 to slightly below 50 percent in 2020 as a result of a recent rise of BEV sales in Europe. Nevertheless, China is expected to remain the leader in BEV sales, with an estimated 9.0 million units sold in 2030, compared with about 5.5 million for Europe, according to our McKinsey Electrification Model.
In addition to being a global sales leader, China is also largely self-sufficient when it comes to BEV production. The country’s local supplier ecosystem can produce all tier-1 and tier-2 parts, such as battery cells, battery-pack components, and drivetrain modules. The top five Chinese companies accounted for 45 percent of the global cell market in 2019. Smaller local suppliers, including those for raw materials and pack components, are scaling rapidly and are becoming large enough to serve both domestic and global markets.
Chinese BEVs offer very competitive cost-to-range ratios compared with their international counterparts, partly because of recent leaps in battery technology. In 2017, for instance, Chinese OEMs were already using LFP technology for low-performing vehicles and NMC-based cells for high-performing ones. Most were also creating vehicles with second-generation NMC-based cells (that is, NMC532). By contrast, Western OEMs, with one exception, were still experimenting with the first generation of NMC-based cells and lithium manganese oxide-based cells.
Although most OEMs now use NMC-based battery cells, China still has an advantage. Two Chinese OEMs introduced NMC811, the latest-generation technology, to the domestic market in early 2019, years earlier than this type of cell hit the Western market. Similarly, one Chinese OEM has already introduced cell-to-pack technology in a BEV model that is already on the road. This technology directly integrates cells into the battery pack without battery modules.
We expect Chinese OEMs to hold their position as battery-technology leaders. The next leap will involve cell-to-chassis technology, in which battery cells are directly integrated into the chassis, without battery packs.
Battery technologies and performance-improvement opportunities
To explore the solutions and products adopted in different vehicles, we looked at the ten BEV models from the benchmark with a start-of-production date from 2015 to 2020. In each one, we tore down battery packs and analyzed the cells down to the chemistry of the main components. Our assessment included an electrical analysis, a particle-size porosity analysis, an electrolyte analysis, weight and dimension measures, and an exploration of active material composition and absorbance (Exhibit 1).
Cell chemistry: NMC811 is expected to be further commodified while LFP presents a cost advantage for economical cars
The battery chemistry breakdown for vehicles in our sample was as follows:
- 1 LFP
- 5 NMC532
- 2 NMC622
- 2 NMC811
NMC811, which was the most advanced cell chemistry in our sample, has the highest energy density.
The most popular chemistry in our benchmark models, NMC532, now has a cost advantage.
In 2018 and 2019 and, to a lesser extent, in 2020, NMC811 cathode active material and NMC811-based cells commanded a high market price relative to the cost of their raw materials. This premium can be largely attributed to the limited availability of NMC811 and its high performance, but higher production costs are also a factor. The added expenses result from the need for greater humidity control and a different lithium source.
While NMC811 is now more expensive than NMC532, its raw-material costs are actually lower. We expect that the high price premium on its raw-material costs, which can be as much as 80 percent, will diminish until it reaches about 50 percent—the premium now paid for NMC532 raw materials (Exhibit 2).1
The lower cost of NMC811, combined with its improved energy density and potentially higher mileage, will make it difficult for NMC532-based cells to remain competitive. In many cases, BEV manufacturers will likely switch to NMC811-based cells to gain cost and performance benefits.
Compared with NMC cells, LFP-based cells have slightly lower raw-material cost per kWh. The cathode active material (CAM) composition in these cells is very close to that of the phosphates used as food additives, and since purity requirements are also similar to food industry standards and don’t require the humidity controls that NMC does, the raw-material costs per kilogram (kg) for LFP are lower than those for NMCs. Moreover, LFP cell production technology is more established than that for NMCs, driving down the price premium on raw materials to 35 percent (much lower than the 50 percent for NMC532). The more established production technology also leads to a lower price per kWh for LFP batteries, even when considering their lower voltage and capacity.
OEMs can either upgrade from NMC532 to NMC811, as described above, or save costs by switching to LFP. The switch from NMC532 to LFP doesn’t significantly change weight per kWh at pack level, so driving range remains similar while costs decrease. When comparing two of the vehicles we analyzed—one with LFP and one with NMC532—we found that switching from NMC532 to LFP would increase battery-pack weight by only 4 percent but reduce costs by about 20 percent (Exhibit 3).
The LFP-based cells in our benchmark analysis are the smallest prismatic cells among the set of batteries we looked at. Their small size increases the cost of the cell’s inactive raw materials per kWh—for instance, those for cell containers and valves—but it also helps better dissipate the heat generated during operation.
The switch from NMC to LFP allows for a simplified pack architecture and additional cost savings. In the model we tore down, the upper pack shell, as well as the module packaging, was made of plastic. In most other BEVs, these components are made of aluminum, which increases both cost and weight. Moreover, this particular battery model has lower performance specifications for charging speed and a smaller cell. These features allow OEMs to reduce the size of the thermal-management system, since the battery can mostly rely on passive cooling and resistive heating.
Would you like to learn more about the McKinsey Center for Future Mobility?
Some OEMs in Western markets also plan to (or already) use LFP cells in their entry models because of the lower cost. Thereby they tend to use simplified packs rather than NMC ones, leveraging LFP’s intrinsically higher safety: the temperature generated by a failure of an LFP cell is normally lower than that for NMC, and this might avoid or limit the hazard of a thermal runaway. As in many cases, the simplification of the pack—for example, by lowering the complexity and power of the cooling system—comes at the expense of the charge and discharge rates, which need to be kept low.
Cell design: Even within the same technologies, there is room for improvement for cell producers and OEMs
When we examined differences in design and chemistry within the same battery technology, we found opportunities for both cell producers and OEMs to improve product performance.
Differences in NMC811-based cells. Among the benchmarked vehicles, two OEMs used NMC811, but they relied on different suppliers. Both cells were prismatic, but energy density was 244 Wh/kg for one and 227 Wh/kg for the second. The difference in energy density resulted from variations in chemistry and cell design.
Analysis of cell construction revealed that the cell with the higher energy density—which we termed the best-performing cell—weighed 2.7 kg, compared with 0.9 kg for the second. This led to a better volume-to-surface ratio and lower packaging costs for the cell with higher energy density.
We found that the manufacturer of the best-performing cell focused its design on energy rather than power, and it could load more material than its competitor. Using electrode thickness as a proxy, we found that it had an average of 57 µm for the cathode and 81 µm for the anodic layer. These values for the lower-performing cell were 50 µm and 69 µm, respectively.
Similarly, the best-performing cell used the most advanced 6 µm copper foil. The lower-performing cell used an 8 µm foil and required slightly more of it, leading to a 33 percent increase in its copper content. Looking at chemistry, the CAM in the best-performing cell had a higher nickel and cobalt content of 4 percent in the transitional metal components.
Overall, these differences explain why energy density in one NMC811 cell was 7 percent higher than that of its competitor’s cell (Exhibit 4).
Pack design: Smart pack design can compensate for less advanced cell chemistry
Our benchmark analysis revealed that a well-designed battery pack is of the utmost importance to cell performance.
Streamlined battery-pack design. Half of the BEV models in our benchmark analysis used NMC532-based cells from the same producer. Their pack designs differed, however, leading to a variance of about 5 percent in pack cost and about 8 percent in pack energy density (Exhibit 5). The models with the lowest cost, A and B, benefitted from their streamlined skateboard design. While model B had a weight advantage because its shell is made entirely of aluminum, its cost is slightly higher than that of model A.
In general, batteries with less capacity have a higher cost per kWh and lower energy-density ratios because many components, including pumps and packaging, don’t scale directly with battery capacity. For example, the battery in model D has a significantly higher cost per kWh and lower energy density compared with those in other models because of its low pack capacity of 35 kWh and a suboptimal pack design that includes a gap in the middle to accommodate the feet of rear passengers. The battery of model C has a high capacity of 70 kWh in a flat skateboard, but these advantages are offset by a massive housing structure that increases crash safety but adds to cost and weight.
Material and manufacturing choice. As noted above, our benchmark analysis included two models with NMC622 and two with NMC811. The benefits of optimal pack design became even more apparent when we compared the model with the more efficient NMC622-based cells, which we term model E, with the two models that used NMC811-based cells. We refer to the model with lower-performing NMC811-based cells as model F and the model with best-performing NMC811-based cells as model G (Exhibit 6).
Housing material. Comparing the battery-pack designs of model E and model F, the main difference involved the choice of housing material. While model F used steel for the pack housing, model E uses a mix of aluminum and plastic.
These material choices have major repercussions, since the decreased weight of aluminum and plastic compensates for the advantage of the higher energy density of the NMC811-based cells. While the NMC811-based cells have an energy density that is roughly 4 percent higher than that of NMC622-based cells, the energy density of the battery pack of model F itself is 3 percent lower than that of model E.
Looking at cost, model E benefits by having a battery-pack capacity that is about 30 percent larger than that of model F. As described above, the manufacturer of model E can spread the cost of all components that don’t scale with the capacity, thereby reducing total cost per kWh. This advantage, along with the fact that NMC622-based cells are often less expensive, offsets the cost savings model F achieves by using steel as housing material. In sum, the pack cost for the model E was 5 percent lower than that of model F. The comparison illustrates the importance of pack design, since model E has a higher energy density at lower cost than model F despite having less-advanced cell chemistry.
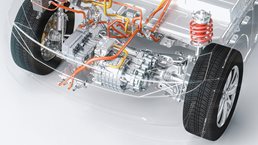
How to drive winning battery-electric-vehicle design: Lessons from benchmarking ten Chinese models
Native BEV platform. Comparing models E and G, the main difference in pack design leads back to the manufacturing platform. Model E sports a skateboard-design battery pack typical of native BEVs, making pack design highly optimized for production. It also has its battery modules in row layout, which creates additional savings for the internal wiring harness. In contrast, model G has an internal combustion engine (ICE) carryover pack, meaning that the vehicle was designed for an ICE powertrain, and the space created by removing the engine and the gearbox is filled with the batteries. Several first-generation BEVs use this architecture because it minimizes the capital expenditures required to launch a new vehicle. But the architecture also leads to a more complex pack shape and higher costs because it is not optimized for BEVs. In consequence, the cost of the battery pack for model G is 3 percent higher than that of model E. That said, the sleeker design of model E can’t offset the chemical advantage of NMC811-based cells. The energy density for model G is thus still 11 to 12 percent higher on both the cell and pack levels than that of model E.
Devising a best-of-benchmark battery
An ideal battery combines high performance, such as better energy density, with an appealing price point. Based on the technological features observed in the teardown of the batteries, the following features are critical:
- Cell chemistry and design. The best-performing NMC811-based cell with the energy density of 244 Wh/kg might often be the best choice for batteries, especially given its relatively low raw-material cost. The cell’s current price premium is expected to drop further, making the cell cost competitive soon. For entry and volume segments, the NMC811-based cell could be exchanged with LFP as cathode to decrease costs further, but energy density would be lower.
- Pack design. As noted earlier, a sleek pack design can improve costs per kWh. Therefore, the model with NMC622-based cells, previously referred to as model E, sets the bar. Also, the thermal-management requirements of the NMC811-based cells can be addressed with a design similar to that of this model, making it the benchmark when it comes to optimized battery packaging.
Combining these design choices, we conclude that significant improvements can be achieved with technology already on the roads today. Compared with the average over the benchmarked vehicles and their batteries, we expect improvements in cost of as much as approximately 15 percent and energy-density increases of as much as approximately 20 percent. This is in addition to expected improvements in battery cells and packaging advances expected down the road.
Our benchmark analysis revealed the large variance in technical design of BEV batteries in China, as well as the strategies for their procurement, revealing that the market is very dynamic. Overall, the Chinese market is producing many champions and will continue to do so, giving local producers a strong chance to compete globally. Based on our insights on cell chemistry, we expect NMC532 cells to lose market share to NMC811 and LFP. This shift has already started in China, where some OEMs started using LFP for entry models and NMC811 for their more expensive, longer-range models. Despite the expected rise of NMC811 and LFP, players with less advanced cell chemistry can still outperform others, provided that they have a strong pack design that incorporates a streamlined, skateboard-like shape, as opposed to more complex shapes.
Further battery developments that are expected to expand down the road will include the following:
- cell-to-pack and cell-to-chassis technology
- innovation in anode chemistry, with silicon and lithium metal entering the market over the next two to five years
- solid-state electrolyte, potentially coupled with a complete redesign of the battery packs