Regulators are tightening emissions rules for on-highway trucks in many of the world’s largest markets (Exhibit 1). From 2030 onward, regulators in Europe will require manufacturers to cut CO2 emissions for new on-highway trucks by 30 percent compared with 2019 levels.1
In the United States, the emissions-reduction target by 2027 is 46 percent lower than 2010 levels. Fifteen US states, led by California, have additional mandates in place that by 2030 will require 30 percent of trucks sold to be zero-emission.2 Similarly, Chinese regulators are requiring OEMs to reduce emissions for heavy-duty trucks by 24 percent from 2021 compared with 2012. Additional longer-term targets are likely, given that China recently joined the growing group of countries with net-zero emissions targets by or before 2060.
Off-highway trucks have traditionally been subject to less regulatory scrutiny; however, OEMs in the off-highway space are anticipating increasing decarbonization pressure from customers. Over the last two years, major mining companies have set ambitious decarbonization targets, aiming for Scope 1 and 23 CO2 neutrality. For instance, Anglo American and Fortescue announced their targets of Scope 1 and 2 carbon neutrality by 2040 in 2019 and 2020, respectively. BHP, Rio Tinto, Teck, and Vale aim to reach this milestone by 2050. Approximately 30 percent of a mine’s Scope 1 and 2 greenhouse-gas (GHG) emissions are caused by diesel engines, largely from mining vehicles such as dump trucks, haul trucks, loaders, dozers, and excavators. Cutting these emissions to zero will require a massive shift to zero-emissions vehicles in the mining sector.
While construction and agriculture players have been trailing miners, the pressure to develop zero-emissions solutions in these sectors is also growing. For construction vehicles, air-quality regulations at the city level are reinforcing decarbonization rules and steering customers to zero-emissions excavators, loaders, graders, and lift trucks. With growing societal concern about sustainability in the agriculture sector, consumer pressure may well prompt a swift shift to zero-emissions farm tractors and sprayers.
Four zero-emissions powertrain technologies are in play for heavy-duty on- and off-highway vehicles
There are four true zero-emissions technologies to power vehicles: battery electric vehicles (BEVs), hydrogen fuel-cell electric vehicles (FCEVs), hydrogen internal combustion engines (H2-ICEs), and biofuel or synfuel internal combustion engines (if a sustainable source of carbon is used). Hybrid and gas engines represent bridging technologies to reduce emissions in the medium term but cannot achieve zero emissions on their own.
The four zero-emissions technologies have different advantages and disadvantages, resulting in varying levels of suitability for different vehicle types (Exhibit 2).
CO2 emissions. While we refer to all four technologies as zero emissions, the CO2 emissions generated in the process of producing the electricity, hydrogen, or synfuel can vary significantly. Although BEVs are carbon neutral if charged solely with renewable power, their use currently leads to high carbon emissions when charged with grid electricity in most regions (given the high carbon intensity of the global grid mix). Carbon emissions from hydrogen production also vary widely but can be more easily controlled. For instance, “green” hydrogen can be produced from 100 percent solar and wind power in renewables-rich regions and delivered to any refueling station. The carbon intensity for biofuel and synfuel depends on the sourcing of biomass and carbon, respectively.
Air quality. While BEVs and FCEVs do not generate any emissions at the tailpipe, H2-ICEs still emit nitrogen oxides (NOx) that require aftertreatment analogous to that for diesel engines (biofuels and synfuels emit NOx and particulate matter). Some producers of H2-ICEs argue that the operating conditions of the engine allow much lower NOx generation than for diesel engines and can thus be considered zero impact. Whether these engines are viable for the urban context or for underground mining will depend on the exact emissions levels and the thresholds allowed by local air-pollution regulations.
Efficiency. Tank-to-wheel efficiencies range from 75 percent to 85 percent for BEVs to approximately 50 percent for FCEVs and some 40 percent to 45 percent for combustion engines.4 At the well-to-wheel level, the differences are even more pronounced: given the conversion losses in producing hydrogen from electricity and synfuels from hydrogen, efficiencies drop to some 35 percent for FCEVs, around 30 percent for H2-ICEs, and around 20 percent for synfuels. Well-to-wheel efficiencies for BEVs depend on where the renewable energy is produced (as longer transmission lines imply higher losses) and whether fast charging is used.
Overall, the efficiency numbers are only approximate and differ as a result of driving patterns: combustion engines become more efficient at higher loads (an incentive for engine downsizing in diesel vehicles), whereas FCEVs are most efficient at low loads (a motive for fuel-cell oversizing and hybridization).
Would you like to learn more about our Automotive & Assembly Practice?
Powertrain capex. Capital costs follow the reverse order of efficiencies: the high efficiency of BEVs entails expensive batteries, while less efficient hydrogen and biofuels/synfuels can be burned in simple combustion engines that are largely identical to today’s diesel engines—indeed, they may be even less expensive than diesel engines because of lower exhaust-treatment requirements (although further R&D is needed to develop the technology). Meanwhile, fuel cells once again land in-between. The optimal trade-off between up-front capital costs and ongoing fuel consumption—which minimizes total costs of ownership (TCO)—therefore differs significantly by vehicle type and use case. For instance, vehicle size and weight determine the required powertrain and the amount of fuel consumed. The driving pattern and route, such as the amount of time spent accelerating, determine the powertrain efficiency and required range. Of equal importance is how regional and local market conditions shape the TCO-optimization picture, including the availability and cost of electricity, hydrogen, and biofuels, and the corresponding recharging or refueling infrastructure required.
Other constraints. Alongside efficiency and capex, additional factors play a role in shaping the TCO performance of different powertrains: batteries require more time to recharge than any fuel, be it hydrogen (for fuel cells or combustion) or biofuels and synfuels. This can lead to reduced uptime, which can affect TCO in use cases that require around-the-clock operations. Batteries and hydrogen both require sacrifices on payload and/or space: batteries are heavy, and fuel cells and H2-ICEs require large tanks. Vehicles that are particularly constrained on payload or space may therefore be limited to more energy-dense biofuels or synfuels.
Consequently, H2-ICE can be a viable powertrain option in various settings, including mining dump trucks (Exhibit 3).
Hydrogen combustion is a nascent solution but could fill an important niche by harnessing established technologies and supply chains
Among the four zero-emissions technologies, hydrogen combustion is still in its infancy, despite a (patchy) history going back to the 1806 de Rivaz engine, which ran on a hydrogen–oxygen mixture. For a long time, hydrogen combustion engines were disregarded, as the very high costs of hydrogen made the powertrain uneconomical. Today, however, some automotive OEMs, component suppliers, and start-ups are reconsidering hydrogen combustion as an additional component of their future powertrain portfolios, alongside batteries and fuel cells.
Despite impressive developments, batteries and fuel-cell technology are not yet ready to meet the very high-power requirements needed for the harsh conditions to which many heavy-duty vehicles (especially in the off-highway segment) are exposed. Mining trucks, for instance, require several megawatts worth of power, run around the clock, and are exposed to extreme vibrations and heat development, as well as dirt in the air. Internal combustion engines have met these requirements for decades, and a switch from diesel to hydrogen could be a straightforward way to decarbonize these engines, with a relatively minor requirement for further technical innovation.
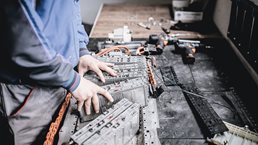
Improving battery-electric-vehicle profitability through reduced structural costs
Even where batteries and fuel cells are technically feasible, hydrogen combustion could carve out niches. Low capex requirements for combustion engines, decreasing hydrogen prices, and the relatively high efficiencies achieved by H2-ICEs at high loads create conditions in which hydrogen combustion can be a TCO-competitive solution (Exhibit 4). Moreover, since bi-fuel combustion engines can run on hydrogen, liquefied natural gas (LNG), or diesel (or hydrogen–gas blends), depending on availability, they can help decarbonize vehicle segments where hydrogen supply and infrastructure have not yet achieved full coverage.
Beyond these considerations, H2-ICEs offer other advantages for automotive OEMs and component suppliers: they make use of current engineering know-how and jobs, draw on existing supply chains and production capacities in the automotive industry, and do not create sustainability and integrity concerns around the supply and recycling of precious metals or rare earths.
Hydrogen combustion and hydrogen fuel cells are complementary, as they thrive in the same ecosystem
One concern about H2-ICEs is their perceived competition with hydrogen fuel cells. However, while there are some applications in which the two technologies could compete, it is more likely that both can help grow hydrogen’s share in the future powertrain mix and propel each other’s success.
For both powertrains, the availability of hydrogen refueling stations and the cost of hydrogen at the pump are the key factors that will determine success and are of greatest concern today. However, both powertrains require (largely) the same infrastructure5; thus, each H2-ICE vehicle will help to bring down the costs for hydrogen fuel cells, and vice versa. Similarly, both powertrains share the same hydrogen-tank technology—a significant share of overall powertrain costs. Allowing OEMs and tank suppliers to amortize R&D and capex over a larger number of vehicles will help bring down the cost curve for all hydrogen vehicles and support the competitiveness of both solutions. Finally, hybrid solutions with hydrogen combustion engines, fuel cells, and batteries are being actively developed by some players to maximize efficiencies for variable load profiles.
Achieving zero emissions across transportation segments globally is a tremendous challenge; nevertheless, H2-ICEs can play their part with multiple applications to provide complementary solutions to FCEVs and BEVs.
H2-ICE’s advantages include lower payload penalties and space requirements, faster refueling times compared to BEV trucks, lower costs, and higher tolerances for heat and vibrations. Various vehicle segments could benefit from these advantages, including these:
- light-duty vehicles, such as tow trucks
- medium-duty vehicles, such as medium-haul and fire trucks
- heavy-duty vehicles, such as concrete trucks
- mining and construction vehicles, such as crawler dozers, excavators, and dump trucks
- agricultural vehicles, such as harvesting machinery and tractors
Several players, including vehicle OEMs, engine suppliers, engineering-service companies, and H2-ICE start-ups, are already investigating hydrogen combustion as part of their on- and off-highway zero-emissions solution offerings. Importantly, they are weighing this potential against the additional R&D resources required to develop the technology around batteries and fuel cells. China, notably, is creating momentum in relation to H2-ICE. The future portfolio of powertrains will be complex, but adding hydrogen combustion vehicles to the mix may be well worth the effort.