Imagine a world where transmission and distribution (T&D) operators use the abundant data at their disposal to target maintenance activities to the needs and risks of individual assets; where they set priorities and organize schedules on the basis of highly accurate predictions rather than ad-hoc reporting after the event; and where they update network information and manage assets in close to real time.
Stay current on your favorite topics
That world is within operators’ reach, yet remarkably few have managed to grasp it. In principle, the process sounds simple: gather data, use it to predict the probability of asset failure, and then use those predictions to target maintenance activities to the assets that need them most. As an alternative to the routine or time-based preventive methods that most utilities still rely on, predictive maintenance holds out the promise of greater accuracy and reliability at lower cost.
And the savings are significant, especially in the context of a lean industry accustomed to annual gains of 1 to 2 percent in real terms, at best. We have seen operators reduce their costs by 10 percent in medium-voltage distribution grids, 15 percent in high- and medium-voltage overhead lines and underground cables, and 20 percent in high- and medium-voltage substations, while improving asset reliability. Even in an environment where tariffs are adjusted at the end of a regulatory period to account for industry cost performance, operators can benefit from a first-mover advantage, capturing higher returns on capital and a more likely repeat of outperformance in the following regulatory periods. Such improvements will become all the more critical in an industry where electric-vehicle connections, distributed generation, and other complex systems are proliferating.
Advanced analytics also provides significant other benefits when implemented as part of a broader performance-improvement program. These include smarter and faster data-driven decision making, improved capex and people management, increased safety, greater compliance with regulatory targets, and better regulatory-driven investments. In fact, using advanced analytics to reinvent asset management helps deliver impressive short-term impact while kick-starting analytics transformations in other parts of the business.
But as many operators have found, moving to analytics-powered asset-management approaches is easier said than done. Our estimates indicate that only 5 percent of maintenance activities in the electric-power industry are based on a data-driven predictive approach. All too often, gaps in data quality, IT architecture, advanced analytics capabilities, and maintenance strategies prevent operators from capturing this considerable opportunity. In this article, we reflect on our experience of helping T&D operators overcome these obstacles and use advanced analytics in asset management to reduce costs and risk, ensure regulatory compliance, and improve asset reliability.1
Some answers before you begin
We’ve found that operators often ask the same few questions as they embark on their advanced-analytics journey. Here are our answers:
Do we need to spend money installing sensors across our network to capture real-time data?
No. Sensors may be justified for critical equipment such as interconnectors, but the length of T&D networks and the very low probability of failure for most assets mean sensors are not warranted across the board.
Do we need big data?
No. Companies often assume they need massive amounts of data from anywhere they can get it. That’s not necessary to start. But you need all your available data, plus a few other types of data that you may not have readily available in house, such as weather forecasts.
Can we get a plug-and-play solution?
No. Each operator needs at least a semi-tailored approach that fits its starting position, performance level, and aspirations, while allowing for rapid and efficient implementation.
Can we do it gradually?
Yes. Most of the operators we’ve worked with started with a priority use case, whether it be low-voltage distribution poles or transformers, and moved on to explore other asset types or extend implementation from a pilot region across their entire geographic footprint.
What results can we expect?
It will depend on your specific circumstances, but other operators’ successes are encouraging. One transmission operator achieved a 10 to 15 percent saving on circuit-breaker maintenance by rescheduling inspection frequency; another reduced opex spending on inspections by 25 percent in HV overhead lines and 10 to 15 percent in HV underground cables. And one distribution operator both improved supply quality and saved 10 to 15 percent of its maintenance spending on distribution feeders by delaying inspections in areas with very low probability of failure.
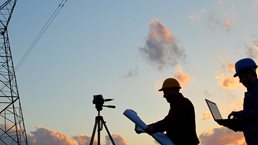
Would you like to learn more about Utilityx, an electric power advanced analytics solution?
How do we get started?
Having decided to proceed with a specific asset, an operator has three main steps to complete:
Step 1: Capture and clean up your data
The operator begins by capturing information about each of its assets. The level of detail varies by asset. As an example, transformers typically require data on about 200 variables.
Most operators tell us their data is scarce, patchy, or not even digitized. Getting it into good shape can seem an overwhelming task. Fortunately, advanced analytics can help. Data-validation algorithms raise alarms to enable anomalous data or trends to be corrected; heuristic algorithms can cover data holes; optical character- recognition techniques can be used to digitize documents even if they are in poor condition; and natural-language processing classifiers can help to capture data from free text. As part of this step, operators also use advanced analytics to reconstruct any networks where failures have occurred to identify the assets or elements affected. Some operators have this information stored in their supervisory control and data acquisition (SCADA) systems, but in any case, they will need to examine additional data such as work orders, previous anomalies, historical load, metereological information, asset age, and other structural properties. After assembling and correlating these elements, operators can then rank assets by probability of failure.
Step 2: Quantify your health and criticality levels
Determining the health and criticality of each asset is the starting point in determining overall risk levels and segmenting asset-management strategies and maintenance and replacement activities.
To determine the health or condition of an asset, an operator will need to assess multiple technical variables—probably somewhere between 10 and 40, depending on the asset type. It will also need to consider factors relevant to its specific situation, such as technical thresholds set by local regulatory authorities, and temperature if it operates in a region with an extreme climate. As an example, Exhibit 1 illustrates the parameters and factors used to determine the health of transformers.
To determine the criticality of an asset, an operator will need to assess not only its reliability, safety, and local environment, but also economic factors. The importance of specific factors varies widely across operators and regions. For instance, one operator we worked with in Asia–Pacific considers proximity to remote or disadvantaged locations and industrial hubs as a major factor, while for one US operator, proximity to forests and susceptibility to fire are key. Exhibit 2 illustrates typical variables used in assessing the criticality of substation assets.
The drivers of asset health are subject to technical judgment, engineering models, and individual experience. Even at the same operator, different people may have different opinions on the variables that matter most. To overcome subjectivity, operators should use engineering scoring models—predictive models based on electrical engineering science, institutional knowledge, and practical experience.
However powerful advanced analytics techniques may be, they can only be effective at optimizing maintenance if they compute the right data and logic. Senior leaders at one company were astonished to discover that one of the best predictors of a circuit breaker’s condition was the time it took to open a switcher—something that long-serving field technicians would have been able to tell them for years, if only they had been asked.
The use of advanced analytics enables operators to test technical knowledge and engineering logic rigorously and efficiently against failures or anomalies. The more data a model processes, the more accurate its estimates and predictions become. Computing power and mathematical knowledge converge to help operators frequently update and improve their methods for calculating the health of an asset. Mathematical and statistical techniques such as machine learning (including random forests, gradient boosting, and neural networks), fuzzy logic, and natural-language processing (including semantic analyzers and Bayesian classifiers) can be introduced, depending on the asset type. By combining insights into the health and criticality of each asset, an operator can determine its risk level, as shown in the example for distribution feeders in Exhibit 3. Having assessed the risk level for all of its assets, the operator can then move to the third and final step.
Step 3: Tailor your asset-management strategy
This step involves reviewing monitoring and inspection frequency, adjusting routine and scheduled maintenance practices, and considering corrective maintenance and replacement suggestions. Utilities looking to improve their system performance, reduce costs, or both, can adopt this segmented approach to achieve their objectives. They capture benefits from extending asset life, from grouping similar anomalies for resolution by the same crews, and from multiple other opportunities, such as the optimization of pruning costs based on the risk of vegetation failure.
One operator we worked with decided to replace some ailing assets earlier than expected because they were critical, while allowing others to fail before they were replaced so that resources were not wasted on maintaining less critical assets. The operator also increased the frequency of inspection for some relatively healthy assets because any failure would have had a disproportionate effect on its network. Even though activity levels rose for the most critical assets and those needing replacement, the operator managed to reduce its total expected costs by 10 percent.
T&D companies can apply the same logic to every component of their network from substations to customer connections. A few operators have gone further and consolidated their approach across multiple asset types. This has given them a holistic perspective that allows them to optimize opex and capex allocation across multiple asset classes based on the expected risk of supply, bringing incremental savings of 5 percent on top of the 15 percent savings captured in the asset class originally addressed.
Some leading-edge companies are starting to adopt powerful software tools that present critical data in an easy-to-understand visual format—often in tablet apps—and suggest the optimal maintenance or replacement action for a given asset at a given moment. A field engineer, technician, or manager can adopt or reject the suggestion with a single click. A “yes” decision automatically triggers the system to generate the necessary work orders and put crews and resources in place.
Capturing value beyond asset management
Operators that use advanced analytics methods to optimize maintenance also reap additional gains that extend beyond asset management.
First, by using an extract, transform, load (ETL) process, operators can take data that resides in multiple databases and is organized in different ways, pull it out, and place it in a single consistently categorized database. Having data in a format from which it can be easily accessed and used by any part of the organization provides a reliable base—a single source of truth—for all asset-management decisions, eliminating the ambiguity and contradictions that come from juggling data from many sources. After spending a month implementing this step, one operator confessed that even if its transformation program had stopped there, the value of getting its data crystal clear would have made the whole effort worthwhile.
Second, data can be integrated in apps that allow frontline management to optimize the routing of maintenance crews based on distance, traffic flows, weather conditions, and so on. One operator went a step further and developed an app that enabled technicians to use their observations on the ground to update information on network health in real time via their tablets.
Third, the granular information delivered by advanced analytics gives operators better insight into crew performance and enables them to manage contractors more effectively. One US utility was paying contractors hundreds of millions of dollars to prune branches and remove fallen trees close to its distribution power lines. After analyzing and modeling its data, the company was able to optimize scheduling and increase trim productivity by comparing and scoring crew performance and flagging variations to supervisors. This enabled it to improve its negotiations with contractors and save 25 percent of its contract spending, with 5 percent savings captured in the first year alone.
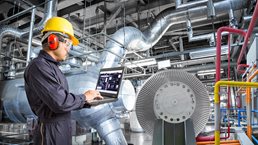
Accelerating digital transformations: A playbook for utilities
Fourth, the use of sophisticated analytics enables operators to be more prudent in their capex as distributed generation grows. This trend may drive some customers out of the grid system altogether, leaving remaining grid operators (and their customers) to pay for upgrades to power infrastructure and stranded assets.
Fifth, as regulatory frameworks such as totex2 and RIIO3 evolve, they increasingly acknowledge the need for operators to invest more, adopt new technologies, and improve reliability, energy efficiency, and other quality indicators. Introducing advanced analytics enables operators to ticks most of these boxes.
Ingredients for success
Having worked with many companies in electric power and other industries, we know from experience that integrating analytics into asset management is not easy. We’ve found, however, that most successful transformations have a number of foundation stones in common:
Having the business work hand in hand with analytics and IT to address opportunities in an agile manner. Analytics translates business needs into IT needs, and IT focuses on delivering the greatest value possible to all parts of the organization. At companies where IT or analytics leads the change, the business side can often be disengaged and skeptical, and vice versa. In our experience, real progress can only be made when IT, analytics, and the business are in close alignment, follow a collaborative and iterative approach, and respond quickly and flexibly to change.
Basing maintenance strategy entirely on asset health and criticality. Putting robust criticality and health indices for all components of the T&D network at the center of a reliability-focused approach will enable operators to cut costs without compromising reliability and open up opportunities to reallocate funds to where they are most needed. In our discussions with operators, many have seen this approach as a way of facilitating more risk-based discussions on capital allocation.
Ensuring IT systems are properly integrated and data is well structured. Data from relevant systems (ERP, SCADA, and so on) will need to be seamlessly combined in asset health and criticality assessments and decision models. Operators sometimes delegate some of these systems to technical partners, but they will need to develop a holistic perspective across all their systems to understand how they can help meet business objectives.
Fine-tuning organizational structures and processes. The key steps here include dismantling silos, moving decision-making authority from departments to senior leaders, and implementing processes that integrate business needs, technical knowledge, and analytical insights, as well as fostering continuous improvement. In our experience, the development of success stories for different asset types and regions will help to overcome any organizational resistance to these kinds of changes.
Building stakeholder (and especially regulatory) management skills. Regulators may be uncomfortable at first with new asset-management approaches, particularly where they involve reducing monitoring frequency for assets in good health or low criticality. One company that wanted to reduce monitoring frequency from every two years to every five had its plans blocked by the regulatory authorities. Concerns about the integrity of power networks will need to be addressed constructively and in a way that highlights the reliability of predictive maintenance and its benefits for customers as well as the operators themselves.
Ensuring leadership from the top. Introducing advanced analytics at the point where the core business intersects with IT and data systems is a complex undertaking, and utilities often struggle to achieve the results they expect. Securing a strong collaboration between IT and technical and engineering teams is key. To make the transformation a reality, top management needs to make digitization a priority and instill urgency across the organization.
After decades of sweating their assets, T&D operators are running out of options when it comes to managing costs and protecting margins. Adopting advanced analytics to power predictive maintenance offers a new avenue to improve performance while reducing asset-management costs by as much as 10 to 20 percent.