Energy-storage companies, get ready. Even with continued declines in storage-system costs, the decade ahead could be more difficult than you think. The outlook should be encouraging in certain respects. As our colleagues have written, some commercial uses for energy storage are already economical. Still more uses will become attractive for utilities, industrial customers, and households, because lower system costs, combined with developments such as the rollback of solar incentives, will make it financially sensible to store power rather than export it to the grid.
The more the cost of an average system goes down, though, the less room storage developers will have to undercut competitors, which will force them to squeeze every dollar of savings out of processes like customer acquisition, engineering, permitting, system integration, and installation. This is essentially what happened in the solar photovoltaic (PV) business from 2005 to 2015, when a 75 percent drop in the cost of PV modules compelled solar developers to focus on operational efficiency, triggered a major restructuring among module manufacturers (including several bankruptcies), and compressed profit margins.
As the market evolves, we expect a relatively small set of energy-storage companies to win big, taking share away from less cost-effective rivals. In this article, we look at how the cost profile of energy-storage systems is changing and what companies in the sector can do to boost their chances of success.
Going down: Battery and balance-of-system costs
During the past five years, several factors have caused the costs of energy-storage systems to drop across the board. Global demand for consumer electronics and electric vehicles spurred investments in battery-pack manufacturing that brought down the unit cost of each pack. Meanwhile, other hardware such as inverters, containers, and climate-control equipment also became cheaper, thanks to design advances and efficiency gains in manufacturing and supply-chain management. And “soft” costs (customer acquisition, permitting, and interconnection, among others), as well as engineering, procurement, and construction (EPC) costs, declined as companies gained experience and streamlined their processes.
Would you like to learn more about our Electric Power & Natural Gas Practice?
From 2012 to 2017, battery costs fell more than 15 percent per year, for a total five-year drop of more than 50 percent. In aggregate, balance-of-system (BOS) costs—other hardware, soft costs, and EPC—declined even faster: more than 25 percent per year. Overall, the decline in BOS costs contributed more than three times the savings that the decline in battery costs did (Exhibit 1).
Our component-by-component analysis of further cost-improvement opportunities suggests that the costs of energy-storage systems will continue their rapid decline, with some variations by type of system (see sidebar, “How costs compare by type of system”). This decline could, however, be held up for several reasons. For example, utility and power-market regulators might enact rules or policies such as those governing permitting and interconnection that make storage systems costly and time-consuming to install. Investments in manufacturing might produce smaller improvements in efficiency than they did in the solar PV market. Tariffs could boost the cost of imported batteries and BOS hardware from low-cost manufacturing locations. Having assessed the potential for these developments, we think it is unlikely that they will materially impede cost reductions for energy-storage systems, and so we have not accounted for them in the two scenarios described below.
In our base case, the installed per-kilowatt-hour cost of an energy-storage system would decrease roughly 55 percent by 2025, thanks to continued advances in manufacturing scale and technology as well as improvements in storage-system engineering and design. There is also a plausible best-in-class scenario in which market-leading energy-storage manufacturers and developers deliver a step change in cost improvement: additional process-efficiency gains and hardware innovations could reduce the cost of an installed system by more than 70 percent (Exhibit 2). At that point, each kilowatt-hour of storage capacity would cost about $170 in 2025—less than one-tenth of what it did in 2012. In this scenario, battery packs could break through the $100 per-kilowatt-hour mark by 2020.
Below, we explain how these developments might play out in the four main categories of system costs (Exhibit 3):
- Battery-pack costs decline by more than 50 percent by 2025 in the base case as global competition intensifies, leading to larger-scale manufacturing, consolidation, improvements in manufacturing processes and technology, and commoditization of products. The best-in-class scenario envisions that battery makers will incorporate multiple chemistries and formats (for example, reduced cobalt cathodes and solid-state batteries), gain more efficiencies from automation and added scale, integrate their supply chains, and even move some operations like electrode manufacturing in-house. All these advances can be financed inexpensively as the cost of capital comes down.
- BOS hardware costs drop by more than 50 percent in the base case. Design improvements remove unnecessary costs and complexity from inverters, wiring, containerization, climate controls, and other components. Further competition from incumbents and new low-cost manufacturers will also pressure pricing for storage hardware. In the best-in-class scenario, the use of new materials and technologies (such as silicon carbide for inverters), the accelerated growth of low-cost manufacturers, and innovations in design (such as the development of prefabricated, modular components) enable additional cost savings.
- Soft costs drop 60 percent in the base case. As utilities optimize the use of battery storage, they streamline their procurement processes and require less time and effort from developers. The additional cost reductions expected under the best-in-class scenario stem from developers’ efforts to digitize tendering and the emergence of standard approaches to permitting and interconnection.
- EPC costs fall in the base case because efficient, experienced EPC firms achieve economies of scale and reduce on-site labor by pursuing standardization in design and construction. Alliances with committed developers also provide EPCs with the confidence to invest in capabilities and resources that improve efficiency. The best-in-class scenario accounts for larger-scale EPC enterprises, the development of hardware and software with plug-and-play compatibility, and prefabricated components that reduce manual installation steps on-site.
Staying ahead: Opportunities for energy-storage players
The low-cost future of the energy-storage market will make for a tough competitive environment—but a rewarding one for players that make big improvements in performance. Here is how companies along the value chain can achieve the cost reductions they’ll need to attract and win customers:
BOS hardware manufacturers will likely need to pursue aggressive increases in scale. Low-cost manufacturers have not yet turned their full attention to the storage market. But that situation should change as utilities spend more on energy storage. (A similar dynamic played out in the solar-inverter market over the past five years or so, when new Asian manufacturers arose to challenge incumbents.) To counter the low-cost threat, existing manufacturers may have no choice but to pursue economies of scale and perhaps expand into other product segments. Few companies now manufacture both storage components and solar inverters, but combining operations could be beneficial because the underlying technologies are similar. Component makers can also reduce costs by adopting new technologies such as three-phase inverters by replacing inverter hardware with software and by switching to lighter materials like silicon carbide.
EPC companies can adopt more efficient practices, such as lean construction (for example, optimizing crew sizes and eliminating downtime and wasted effort), prefabrication of major system elements, simplified bidding, and streamlined interconnection processes. Some of these practices will take hold naturally, as companies gain experience. Purchasing components in higher volumes will reduce per-unit costs. Alliance-contracting relationships can enable companies to work with sophisticated, low-cost installation partners across many projects. There is also ample opportunity to save time and effort with better design. Standardizing certain aspects of storage systems (for example, container and climate-control specifications) will lessen the need for expensive custom engineering. EPC companies should learn to match their designs closely to customers’ requirements and thereby avoid including components that are more expensive than necessary. Modular hardware, along with hardware and software that are made to be compatible, will also eliminate manual installation steps.
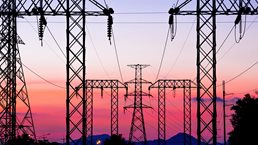
Battery storage: The next disruptive technology in the power sector
Storage-project developers used to have to teach new customers about storage technology, system design, project economics, and available incentives. All this effort made customer acquisition more expensive. Now that customers are better informed, selling a project costs a good deal less. Technology can make customer acquisition even more efficient. Advanced analytics can help developers identify prospective customers and target them with attractive offers. Digital tools for engaging customers and facilitating sales, which are already in use, can be improved with automated capabilities for estimating savings and developing preliminary system designs (for example, simulating customer loads to help with system sizing, or using images from satellites and drones to lay out sites). For utility-scale projects, developing storage along with renewable-energy generation will make projects more profitable by spreading out customer-acquisition costs, making more efficient use of land and site infrastructure, and improving the ability to optimize intermittent renewable generation (for example, time-shifting generation).
Storage developers and system integrators will also need more flexible approaches to procurement so they can take advantage of rapidly declining battery and BOS hardware costs. Like their peers in the solar market, some storage developers struck forward-pricing agreements with battery and component makers in the hope of achieving certainty over their costs—and came to regret these agreements as costs fell. Storage developers should be mindful of the same risk.
The cost projections we have described suggest that the market for battery storage will expand. While we are still assessing the potential for energy storage to open a new frontier for renewable power generation, energy storage should become a significant feature of the energy landscape in most geographies and customer segments. As battery packs grow cheaper, energy-storage companies will have to manage BOS and soft costs well to stay competitive. Opportunities to do this, some of which we have outlined in this article, are plentiful—and real. Seizing them will require innovation and investment across the storage value chain, particularly in the next one to three years, when early-mover advantages will be there for the taking.