Today’s power-generation sector is facing disruption on an unprecedented scale. Renewables are becoming more competitive and produced more power than coal did in the United States for the first time in April 2019. The cost of energy storage is falling, electric vehicles are proliferating, distributed power generation is gaining traction, smart grids are spreading, regulators are rethinking their stance, and customer preferences are evolving.
In spite of the headwinds they face, gas- and coal-powered plants are likely to remain central to the global energy supply for at least the next decade—and they need to improve their fuel efficiency and performance to remain competitive. In the United States, 1,800 gas plants and 300 coal plants provided three-quarters of generation capacity in 2017 (720 gigawatts (GW), approximately 460 GW of gas and 260 GW of coal, out of approximately 1,100 GW of net summer capacity). McKinsey forecasts indicate that the United States will still use approximately 725 GW of fossil-based generation: approximately 550 GW of gas and 175 GW of coal in 2030.1 The players that will be a part of this generation capacity will operate the most efficient fossil-fuel plants in the world.
To achieve the requisite step change in performance, fossil-fuel plants should embark on a transformation that combines digitization and advanced analytics with classic lean operations. Although investing large capital sums in transformation may seem daunting in what appears to be a declining sector, as discussed above, many assets will continue to operate in the medium to long term. Through a carefully targeted deployment of technology-enabled lean operations, such as work-flow optimization, condition-based maintenance, process digitization, and agile working, utilities can increase plant efficiency (heat rate) by up to 3 percent, reduce the average all-in cost of generation (excluding fuel) by 10 to 20 percent for coal and 5 to 15 percent for gas, all while improving safety (Exhibit 1). A full lean transformation supported by technology solutions could also unlock significant value in incremental earnings.
Digital solutions bring a wide range of benefits. They can enable utilities to quickly ramp production up or down in a highly variable environment and support the adoption of agile by working in small, efficient, cross-functional teams. They can also help utilities reimagine work flows across the value chain and equip staff with transferable skills as fossil assets approach retirement. In this article, we explore where digitally enabled lean operations can unlock the most value and outline a proven approach for implementing them in a power plant.
Where can digitization unlock value?
Drawing on our experience of transforming power-plant operations and driving digital transformations across heavy industries, we have identified the following areas where digital solutions can have the greatest impact: namely safety, heat rate and efficiency, and maintenance and reliability.
Safety
In a sector where employees work with large, complex equipment and assets and an incident could have disastrous consequences, safety is of paramount importance. Factors such as workers’ experience in their role and how many hours they have worked in the past 24 hours are widely recognized as drivers of workplace injuries, but many other, less obvious variables can also come into play. By subjecting operational data, safety records, and data from external sources to advanced statistical analysis, operators can broaden their understanding of risk, identify the factors that increase it disproportionately, measure the expected impact, and rank risks by predicted impact to inform prevention planning (Exhibit 2).
Most operators tend to use root-cause analysis after an injury has occurred, focusing on mitigation strategies. However, developing a better understanding of risk drivers enables plant managers to translate insights into practical preventive measures, such as automated alert systems. For example, if a plant worker enters a high-risk area with suspended loads at the end of a long shift, when he or she may be tired, the system could immediately send a supervisor an alert. Such practices give plants a better chance of minimizing or eliminating injuries before they happen.
Efficiency and heat-rate improvements
Heat rate is the key measure of a power plant’s energy efficiency. When heat rate is improved, less fuel is needed, saving costs, reducing emissions, and shifting the plant’s position on the dispatch curve and regional generation profile.
Utilities can unlock and sustain heat-rate improvements through direct investment in plant equipment. In our analyses of heat-rate trends across dozens of plants, we see significant variability under the same load conditions within the same season, indicating that different operators achieve different outcomes under the same circumstances. If an operator with average heat-rate performance could make the shift to top-quartile performance, it would improve heat rate by 1.0 to 2.5 percent and save $1 million to $3 million per 1,000 megawatts, depending on fuel type, fuel costs, current performance, and variability.
However, such an improvement rests on a granular understanding of a plant’s heat-rate performance that few operators possess. They typically rely on aggregated data in the form of monthly averages or annual cycles. Top performers draw on data every few minutes throughout a shift to derive much richer insights. Recognizing the potential, leading companies are introducing digital tools to power dynamic dashboards that provide granular information in real time.
The introduction of digital tools and advanced analytics methods can help operators understand the causes of variability, identify how to act on them, and subsequently monitor improvements.
Understanding heat-rate variability. One combined cycle gas turbine (CCGT) plant analyzed a previous year’s production data at five-second intervals across 1,600 variables. It found that well-understood sources of heat-rate variability such as unit output, ambient temperature, relative humidity, and duct-burner operation explained only 25 percent of the variability observed (Exhibit 3). The remaining 75 percent was explained by an array of factors including cooling-tower set point, inlet gas temperature, and MVAr (megavolt amps reactive) set point.
Identifying levers to lower heat rate. By adopting an approach based on advanced analytics, an operator’s visibility into levers affecting heat rate is significantly enhanced, thus enabling it to generate insights—sometimes counterintuitive ones—to improve heat-rate performance. At the CCGT plant mentioned above, a transformation team structured, cleaned, and aggregated 120 gigabytes of data. Data scientists then worked iteratively with plant operations to analyze the data, identify key controllable variables, and determine their relative importance. Finally, the plant operator used these insights to define operational changes that reduced fuel costs by 1 percent, saving $1 million a year. In another example, a generator managed to improve its heat rate by 1 percent by reducing temperature differences in its boiler. The generator began by installing sensors in the boiler to monitor process variables, and then cleaned, structured, and analyzed data from the sensors using adaptive models that simulated temperature differences. By acting on insights from this analysis, the operator was able to optimize key operating parameters to reduce temperature differences and maximize energy efficiency.
Monitoring heat-rate improvement over time. Through the use of advanced analytics, operators can not only monitor heat-rate variability but also compare outcomes under the same or similar conditions from one year to another. For regulated utilities, this represents a valuable way to demonstrate improvements to a regulator.
Maintenance
In our experience, generators put a lot of effort into planning for outages but spend relatively little time on planning and executing day-to-day maintenance. This gap can have material consequences for plant performance. If, for instance, a scheduler planning a particular job fails to confirm that all the requisite parts and tools are available, the maintenance crew may lose time tracking down missing items before it can start work. Similarly, if it isn’t clear which tools and parts are needed, time can be wasted in a back-and-forth between the warehouse and the scheduler’s office. And if the job has not been properly scheduled, the maintenance crew may experience “tag out” or “lock out”—being ready to begin work but having to wait for the operations team to obtain the necessary permits.
Another common issue with maintenance derives from the industry-wide talent shortage. Often a maintenance crew has insufficient experience to complete a task and relies on guidance from the scheduler or senior crew members. As a result, “wrench time”—the time the crew spends executing the job—suffers.
Utilities can prevent such issues by introducing analytical tools and dashboards, and by equipping plant personnel with tablets that track end-to-end work flows and provide a platform for sharing best practices. Such real-time visual tools create transparency throughout planning, scheduling, and execution. They enable operators to reduce or eliminate waiting times for tools and equipment, prevent delays due to lock out, and minimize unproductive standby time between work orders.
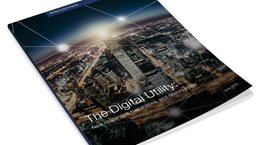
The Digital Utility
Finally, when plant teams rely on personal experience or fixed cycles to determine the timing of maintenance activities, unplanned maintenance is often higher than it should be. Utilities can achieve substantial improvements by installing sensors in critical components of plant equipment to allow real-time tracking and enable a shift from time-based to condition-based maintenance. The data captured by these sensors is analyzed to generate insights that are used to inform preventive-maintenance programs. These programs reduce the frequency of unplanned maintenance, minimize unnecessary maintenance, and save costs.
One coal-fired power station cut downtime by half by creating a machine-learning model that drew on multiple existing databases—control systems, enterprise management, coal logs, shift rosters—to predict which equipment might fail and when. The model achieved a success rate of 75 percent in predicting failures three months in advance. The plant operator revamped its maintenance strategy, developed a new user interface to promote early planning, and changed its operating procedures to extend the life of equipment.
Other improvement opportunities
The areas where a digital-enabled operations transformation can have an impact go beyond safety, efficiency and heat rate, and maintenance and reliability.
Once a utility embarks upon a digital-enabled operations transformation, it can employ advanced analytics to help increase plant flexibility by improving minimum and maximum loads and optimizing ramp rates so that generation can be varied in a timely manner. Similarly, a utility can improve environmental compliance by introducing sensors to constantly monitor emission levels, along with automated controls to adjust catalyst input. In addition, digitally enabled lean operations can help the utility improve outage planning and work management, optimize third-party spend on purchasing and logistics, and enhance water-treatment and air-quality control.
The broad array of digital applications that could be found in the power plant of the future is illustrated in Exhibit 4.
Making a start
Digital tools and technology do not create value on their own. To ensure that new solutions are adopted and don’t gather dust because the plant team doesn’t trust or value them, solutions need to be codesigned with the front line rather than tossed over a fence for them to use. Value is unlocked as a result of fundamentally changing how work gets done by reimagining existing processes and designing solutions that empower and augment employees.
In our experience with digital initiatives in traditional heavy industries, truly transformational change is achieved only by efforts that add real value by creating new ways of working that build on existing processes. These efforts provide a unique opportunity to “walk the talk” on agile, design thinking, and scrum, by adapting them to unique operational conditions and diverse talent profiles.
Specifically, for power plants, we recommend keeping the following success factors in the frame as you design your transformation programs:
Keep safety and reliability front and center. Ensure that operating-model changes maintain employee and public safety and high reliability, and do not erode a well-established culture of excellence.
Make ‘agile’ your own. Translate conventional agile methods to your environment. Test new ideas and technologies quickly without compromising safety and reliability. Work iteratively through sprints instead of defaulting to familiar “waterfall” approaches.
Know your users and let them lead. Every initiative needs to be grounded in how work actually gets done. That means developing a deep ethnographic understanding of operators, maintenance planners, buyers, material handlers, and other power-plant staff. Armed with this understanding, map out user journeys, identify pain points, and work collaboratively across functions to develop and prioritize improvements.
Transform end-to-end work flows, not just units of work. Point solutions may be helpful, but they are not transformative; every digital initiative should be accompanied by several analog changes to processes, policies, and job descriptions.
Ensure business cases are pragmatic and can scale. “Build, buy, or collaborate” decisions require rapid estimation and a bold commitment to testing early and failing fast. Have a perspective not just for the impact from the minimum viable product but also for where and how the solution might scale across the enterprise.