The COVID-19 pandemic has exposed the fragility of the world’s supply chains for medicines and medical products, food, energy, vehicles, telecom equipment, electronics, and countless other goods. Certain companies have begun to reconfigure their sourcing and manufacturing footprints for greater reliability and resilience, setting up more locations so that they don’t have to depend on just a few geographies. But some nations are not yet ready to take full advantage of these shifts.
India stands out as one such country: a potential manufacturing powerhouse that has yet to realize its promise. From fiscal year 2006 to fiscal year 2012, India’s manufacturing-sector GDP grew by an average of 9.5 percent per year. Then, over the next six years, growth declined to 7.4 percent. In fiscal year 2020, manufacturing generated 17.4 percent of India’s GDP, little more than the 15.3 percent it had contributed in 2000. (By comparison, Vietnam’s manufacturing sector more than doubled its share of GDP during the same interval.) And in the past 13 years, India’s manufacturing-sector share of employment increased by just one percentage point, compared with a five-point increase for the services sector.
As our colleagues argue in the McKinsey Global Institute report India’s turning point: An economic agenda to spur growth and jobs, developing globally competitive manufacturing hubs represents one of the biggest opportunities for India to spur economic growth and job creation this decade. This article offers a closer look at how to do that. We identify 11 manufacturing value chains with strong potential to operate in international markets, power growth, and provide long-term employment and skill pathways for millions. Their potential comes from several factors. First, these value chains are well positioned to capitalize on India’s advantages in raw materials, manufacturing skill, and entrepreneurship. Second, they can tap into four market opportunities: export growth, import localization, domestic demand, and contract manufacturing.
Lastly, the 11 value chains stand to benefit from a fresh, focused approach to industrial policy. This approach would not entail the sort of far-reaching bureaucratic reforms that can lower input costs and improve the ease of doing business across many sectors. (Such reforms could be valuable, but their slow pace to date has resulted in feeble gains for manufacturers.) Rather, the new reforms would specifically catalyze the growth of India’s manufacturing value chains by helping them lift their productivity, secure know-how and technology, and gain access to capital. With these reforms, and complementary actions by manufacturing companies, we estimate that the 11 value chains could more than double their GDP contribution to $500 billion in seven years, while powering extensive job creation at a time when the COVID-19 crisis has pushed millions below the poverty line.
A transformative opportunity: 11 manufacturing value chains, $300 billion of GDP potential
While some companies and sectors in India’s manufacturing industry have delivered strong returns on invested capital (ROIC), most have not. According to our analysis, nearly 700 of the top 1,000 manufacturers produced returns that were less than their cost of capital in 2018, thereby destroying value. By contrast, the sectors that generated healthier returns saw increases in invested capital during the four years from 2016 to 2019 (Exhibit 1).
Several conditions help explain why Indian manufacturers tend to create limited value. Some have to do with the costs of infrastructure and key inputs. Poor logistics causes delays and raises inventory costs; high prices for power and credit inflate operating expenses. Other conditions are inherent to the value chains. The small, fragmented companies that make up some value chains cannot operate productively, let alone at peak efficiency; cannot innovate quickly enough to keep up with competitors; and cannot command price premiums because they lack strong brands.
At the same time, many of India’s manufacturing value chains enjoy important advantages that could help power them to rapid growth. India’s natural resources (for example, iron ore, bauxite, high solar insolation, and cotton) and low-cost labor are a boon to makers of basic metals, textiles and apparel, renewable energy, and chemical products. The country’s large numbers of well-trained workers lend strength to skill-intensive value chains such as pharmaceutical formulations, capital goods, and automotive components. And many manufacturing value chains in India operate in close proximity to strong domestic markets. The makers of fast-selling technology products, for example, enjoy ready access to millions of Indian consumers.
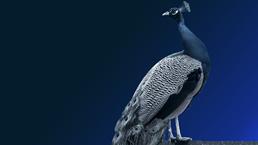
India’s turning point: An economic agenda to spur growth and jobs
Achieving new levels of competitiveness and scale
Although the advantages described above are helpful, they are not enough to propel India’s manufacturing value chains to global competitiveness. The value chains must develop further, at significant expense and effort, before they can become global champions. To identify manufacturing value chains with the best global prospects, it is helpful to define groups by their states of development and the types of support that would help them most (Exhibit 2).
- Mature value chains that must scale up. These value chains possess sophisticated capabilities and healthy supplier ecosystems, which contribute to higher productivity. They serve domestic demand and have proven their ability to compete in export markets, and they don’t rely on imported supplies. Their challenge is to increase both exports and domestic sales. Pharmaceutical formulations, automotive components and vehicles, and chemical products fit this description.
- Established but underweight value chains that must transform. Some of India’s manufacturing value chains produce goods mainly for domestic buyers. But troublesome shortcomings prevent them from competing outside the domestic market. In the food-processing value chain, for example, companies are neither large nor productive enough to make a product assortment that can compete on quality and cost in export markets. Another shortcoming, seen in India’s aerospace and defense (A&D) value chain, is a lack of technological sophistication, relative to peers in other countries. Larger manufacturers will need to strengthen their own capabilities as well as those of smaller suppliers.
- Emerging value chains that India must seed. Compared with other Asian countries, India has invested less in so-called “sunrise” sectors, such as semiconductors and solar, and now trails far behind. But India can still capture a sizable share of the global market for low-carbon technologies (such as energy storage, hydrogen equipment, carbon capture and sequestration, electric two-wheelers, drones, and lithium-ion cells). A practical approach is for large industrial-promoter groups to work with global OEMs on accessing the technology and capital needed to establish local manufacturing capacity that would first serve the large domestic market.
According to our analysis, these categories include 11 manufacturing value chains that can generate, within the next seven years, about $320 billion more in gross value added (GVA) than they do now. About 80 percent of that GVA potential resides in six value chains: chemical products and petrochemicals, agriculture and food processing, electronics and semiconductors, capital goods and machine tools, iron ore and steel, and automotive components and vehicles (Exhibit 3).
To realize this potential, the 11 value chains will need to pursue the following four opportunities:
- Growth of domestic sales ($180 billion of additional GVA). Indian manufacturers could tap into healthy consumer markets for products such as fast-moving consumer goods, consumer durables, food products that come from agri-processing, agrochemicals, marine products, automotive products, aluminium, and renewables. To capture this opportunity, manufacturers in these markets should consider focusing on moves like offering quality products in smaller formats and at different price points. Several of these consumer markets will grow as GDP per capita increases, provided that enabling factors such as consumer credit and attractive retail interest rates are in place.
- Export growth ($70 billion to $75 billion of additional GVA). Exports of manufactured goods could increase from 14 percent of manufacturing GDP to more than 25 percent. Much of that increase could come from sectors where Indian manufacturers are already competitive, such as generic pharmaceutical formulations, farm equipment, auto components, small cars, steel, textiles, and processed goods. To compete in foreign markets, manufacturers must achieve economies of scale, meet international quality standards, comply with foreign regulations, and sustain R&D investments.
- Import localization ($55 billion to $60 billion of additional GVA). India’s manufacturers could challenge foreign competitors for market share in a few strategic sectors, such as electronics, A&D, capital goods, active pharmaceutical ingredients (APIs), and petrochemical intermediates. Our analysis suggests an opportunity to reduce India’s spending on imports from 30 percent of all manufactured goods to 15 to 20 percent. To capture this opportunity, domestic manufacturers would need to upgrade the technology and quality of their offerings while lowering prices. Short-term trade protections might be necessary to help local value chains catch up with foreign ones.
- Contract manufacturing for global markets ($4 billion of additional GVA). Indian manufacturers are operating well below their maximum capacity, with utilization ranging from 60 to 70 percent across sectors, according to the Reserve Bank of India. In select value chains, such as light and heavy engineering, chemicals and APIs, farm equipment, machine tools, electrical goods and machinery, and automotive, Indian manufacturers could fulfill overseas orders in the near term through tolling (where one company provides the raw materials to a third party, which manufactures the product) or contract manufacturing (where the third-party company both sources the materials and provides the services to manufacture them). These arrangements would need to match underutilized assets with the right markets and companies.
Three priorities for supporting the growth of India’s manufacturing value chains
As India’s turning point makes clear, various reforms can help lift the competitiveness of India’s companies. These reforms include some that target particular sectors. In this section, we look more closely at three sets of policy interventions that could—if enacted in conjunction with actions that manufacturing companies themselves can take—accelerate the growth of manufacturing value chains specifically. (For an example of how such policy interventions and business actions can work together in an individual value chain, please see the sidebar, “Catalyzing growth in the agricultural and food value chain.”)
Raising productivity
To become globally competitive, India’s manufacturing value chains must lift their productivity—in GVA output per full-time-equivalent worker—closer to global standards. They have a long way to go in this regard: their labor productivity and capital productivity are both low. Compared with India, manufacturing productivity in Indonesia is twice as high; in China and South Korea, productivity is four times higher. (Especially wide disparities can be seen in certain sectors. For example, South Korea’s electronics manufacturing sector is 18 times more productive than India’s, and its chemicals manufacturing sector is an astonishing 30 times more productive.) While other developing economies such as China have managed to catch up with advanced economies in capital productivity, India’s capital is only about two-thirds as productive as China’s.
Improvements to key manufacturing processes could increase the productivity of Indian companies in the chosen value chains by a factor of five—with a tripling of labor productivity and a capital-productivity increase of one and a half to two times. By adopting Industry 4.0 and automation technologies and investing in analytics, reskilling, and upskilling, Indian manufacturers could accelerate the capture of many of these gains.
Policy reforms that help create better infrastructure and logistics could also help Indian manufacturing become more productive. Many of the country’s manufacturers particularly need ecosystems of nearby suppliers. For example, companies that make high-tech goods such as computers, electronic and electrical equipment, and telecommunications equipment must have reliable access to components. By providing incentives to suppliers that operate within port-proximate export-processing (or coastal economic) zones, policy makers can make a tremendous difference in favor of Indian manufacturers.
Other opportunities for Indian manufacturers to boost their productivity include offering more value-added goods, with higher product quality, better packaging, and stronger brands. Such enhancements would allow them to command higher prices, leading to one and a half to three times higher GVA (for example, in food processing, capital goods, steel, and steel products). Unlike other opportunities described in this section, this one can be captured without making major investments, which would improve companies’ ROIC. Improvements in ROIC could result in further benefits for Indian manufacturers. Better returns would help them attract more capital, and as their profits increase, they could reinvest their capital surpluses rather than seek outside investment.
Securing know-how and technology
While India’s established manufacturing value chains possess the technology and know-how they need to compete with overseas peers, the less-developed value chains do not. To be sure, manufacturers themselves must source technology through acquisitions and alliances. The government can also help. One approach: create a stable framework of time-bound and conditional localization incentives to entice global companies to set up operations in India, either independently or with a local partner. For example, leaders in India’s automotive industry generally believe that high import tariffs on finished vehicles allowed the industry to develop local product-development, supplier, and manufacturing capabilities. Over time, this manufacturing base grew stronger and more competitive, enabling exports of automotive components and finished vehicles to reach more than $25 billion even as these tariffs were progressively reduced.1
Such an approach would greatly help value chains such as A&D. The government has already raised the limit of foreign direct investment (FDI) to 74 percent to alleviate the concerns of global defense companies about the transfer of technology. The Indian government might capitalize on this by providing localization incentives and expediting awards of local A&D manufacturing contracts.
Additional support for high-technology and low-carbon value chains might come from viability-gap funding (VGF), in which the government provides some capital to make projects financially viable. For example, India imports nearly all of the LCD panels that go into electronic devices made in the country. The country lacks the technology to set up an LCD-panel factory, and the investment case for such a plant does not hold up in the current tariff regime. Combined with time-bound tariffs or incentives, VGF could help improve the returns from investments in such a factory to 10 to 12 percent of the invested capital.
Accessing capital
The availability of capital will be the single-biggest obstacle to increasing India’s manufacturing GDP. With an incremental capital-to-output ratio between 4.5 to 6.0 (which could become more favorable with productivity gains), India’s manufacturing sector would need investments totalling $1.0 trillion to $1.5 trillion over the next seven years to double its GDP in the same timeframe, provided that India also raises its GVA capture in these value chains by 25 percent.
Financial reforms would help stable, cash-generating manufacturers attract low-cost domestic capital from long-term savings pools, such as pension funds and insurance. However, these savings pools alone cannot supply as much capital as Indian manufacturing companies will need. They will also have to tap other sources. Many of the larger domestic manufacturing companies generate adequate returns and so are likely to attract investors. If India’s recent FDI growth continues and manufacturing doubles its share of FDI, then FDI could provide 25 to 30 percent of the capital that Indian manufacturers will need over the next seven years. Patient long-term investors, such as those in Japan, are strong candidates. India receives only 1.5 to 2.0 percent of its annual FDI from Japan but could collect several times more than this if it made an aggressive push.
India has an opportunity to raise its manufacturing competitiveness and become a supplier of choice not only for its large consuming class but also for global markets. The specialization approach that focuses on eliminating roadblocks in the chosen value chains holds great promise for bringing together manufacturers and, with government support, raising productivity, securing superior know-how, and generating higher returns on capital.