At automotive OEMs, industrial robots are welding and painting cars. Within warehouses, they are putting stock on shelves, picking out items for orders, transporting goods from docks to shipping areas, and packaging them for transport. At semiconductor plants, robots move delicate wafers without damaging any components. Elsewhere, they’re assisting with gluing, assembling, cutting, grinding, and other routine yet critical tasks.
Stay current on your favorite topics
The growing prevalence of these robots is not surprising, because industrial operations, both mundane and complex, are increasingly automated. Cost is a factor in their rise, since the average selling price for a robot has fallen by more than half over the past 30 years. Emerging markets have an additional imperative for automation: the need to improve product quality to compete effectively in the export market.
Manufacturers of robotic components are benefiting from rising automation, including those that produce end effectors—devices mounted at the end of robotic arms and other automated machines that perform specific tasks. This category includes grippers, which hold and manipulate objects, and end-of-arm tools (EOATs), which are complex systems of grippers designed to handle large or delicate components. These two subsegments have experienced strong growth because they enable so many innovative applications. Together, they account for about $2.4 billion in annual sales, with further gains expected as the robotic installed base increases. (This figure does not include sales for weld guns’ dispensing nozzles, another subsegment of end effectors.)
Despite the rising demand for grippers and EOATs, little research is available on this critical market segment. To gain more insight into this evolving market, we analyzed trends within industrial robotics to determine how they would affect demand for end effectors. We also examined customer preferences to identify the factors behind purchase decisions for grippers and EOATs. Here are our major findings.
The thriving industrial-robotics industry
The industrial-robotics sector has been on the upswing for the past few years. Between 2012 and 2017, the worldwide installed base of operational industrial robots increased by an average of 10 percent annually.1 Worldwide annual shipments of robots soared to around 381,000 in 2017, more than double the approximately 159,000 shipped in 2012.2 Many of the most oppressive and routine workplace chores—those that are dirty, dull, or dangerous—are now entirely within the robot realm. But thanks to recent technologic advances, robots are also handling more complex operations that require extreme precision. For example, robots with laser-vision systems can fit doors precisely to car bodies. These improvements, combined with several economic forces, are prompting companies to consider industrial robots more seriously.
Would you like to learn more about our Advanced Electronics Practice?
In 2017, there were a little more than two million industrial robots operating on factory floors and other commercial locations.3 With 14 percent annual growth expected under favorable economic conditions over the next five years, the installed base could reach about 4.4 million units by 2023 (Exhibit 1). As the installed base of industrial robotic arms grows, manufacturers of end effectors stand to gain. By 2023, grippers and EOATs will reach an estimated market size of about $5 billion—more than twice the 2017 amount.
New opportunities within the robotics ecosystem for providers of grippers and EOATs
Today’s gripper and EOAT market is fragmented. Manufacturers often specialize in creating tools in one or more of the basic formats for these devices (primarily mechanical, vacuum, or magnet). Others create custom grippers and EOATs, including those that handle specific materials. For instance, the German manufacturer Schunk is known for creating grippers for handling metals, and Piab is recognized for vacuum products. In addition to companies that supply complete grippers and EOATs, some suppliers focus on providing subcomponents, such as the actuators that provide the energy required for clamping in a gripper.
Geographic and industry-specific demand patterns
Beyond general trends related to end-effector demand, interesting growth patterns and market dynamics have emerged at both the geographic and industrial levels.
At the country level, China takes the lead
The robotic installed base will see strong global growth, but emerging markets will account for the greatest increase. China, in particular, will see automation surge, partly in response to the government’s Made in China 2025 plan. Introduced in 2015, the plan aims to transform the country into the world’s top manufacturing powerhouse by improving product quality through greater automation. To achieve this goal, the plan calls for the local production of robots to increase from about 150,000 in 2020 to 400,000 by 2030. China has already made considerable progress, with robotic density—the number of robots per 10,000 manufacturing employees—increasing from 15 in 2010 to 97 in 2017. Much work remains, however, since China’s robotic density is still much lower than that reported by developed markets, such as Germany, Japan, South Korea, and the United States (Exhibit 2). A review of trends does suggest that China has made greater strides in increasing robot density over the past few years than other emerging markets, such as India and Mexico, however (Exhibit 3). As China works to catch up with its global peers, the robotics market could see strong growth for many years to come.
As China builds its robotic installed base, it will see a 25 percent annual increase in demand for end effectors from 2018 through 2023. That figure represents about 45 percent of the total market growth expected over those years, and it’s more than the combined contribution of Europe and North America. Of the $5.1 billion in market value for grippers and EOATs in 2023, more than $1 billion will come from China.
Strong demand within the automotive and electronics industries
A similar dynamic emerged when looking at industry-specific patterns, with some segments showing much greater growth potential than others. Automotive had the largest installed base for robotics, followed by the electronics industry, and these sectors will continue to be the greatest sources of demand. In 2017, robot sales to the automotive industry rose by 22 percent to reach a new peak of around 125,700 units; sales to the electronic industry rose by 33 percent in the same year, reaching a new peak of around 121,300 units.4 With the automotive and electronics sectors expected to remain leaders in automation, they will account for most industry-specific demand for end effectors.
Purchasing decisions for end effectors, including grippers and EOATs
Companies typically purchase end effectors when they automate a new production line or when they decide to convert or overhaul their existing production equipment, including robotic arms. Likewise, companies may purchase grippers and EOATs when they must retool their production lines to support the introduction of new or updated products or when they introduce a variant, such as a hybrid version of a car. Although companies also purchase robotic components because of general wear and tear, this isn’t a substantial source of revenue for suppliers of end effectors, since most parts are covered under long warranties. End effectors also tend to last for much longer than the expected lifetime defined in their specifications.
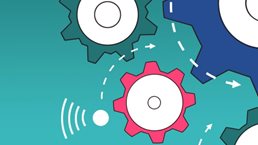
Automation, robotics, and the factory of the future
When it comes to purchase considerations, component price is generally not a top concern when companies are buying end effectors. This is especially true for automotive OEMs that will incur high interruption costs if their production lines are down. For the same reason, reliability is a top priority. Since grippers and EOATs account for around 3 percent of the total cost of automation, the selection of a high-priced supplier will have relatively little impact on a company’s production-line costs.
The future is exciting. Innovators have created robots that mimic the movements of dogs, cats, insects, and humans with eerie precision. In industrial settings, these advances are letting companies transfer some of the most difficult, dangerous, and time-consuming tasks from workers to robots. As this trend accelerates, both investors and robotic-component manufacturers are in strong positions to access profit pools. Of course, major technologic advances could disrupt the robotic-component industry, as they have done in other sectors, and shift demand in unexpected directions. It’s hard to predict whether such disruptions will materialize—or anticipate the time frame over which they might occur—but industry stakeholders will need to monitor all technologic developments closely.