In recent months, structural supply-chain fragility has been catapulted to the top of the news cycle as the ongoing repercussions of the COVID-19 pandemic echo around the world. Government-imposed orders to stay at home, international and domestic travel restrictions, and the need for physical distancing have stretched supply chains and laid bare the key bottlenecks in products’ value chains. Shortages have occurred in areas ranging from basic grocery items to electronic components.
The current pandemic is the type of event that is only likely to occur once in a lifetime. In recent years, however, supply-chain risk management has become more of a pressing issue for CEOs across industries. Vulnerabilities have been exposed by trade tensions, natural disasters, and other geo-economic disruptions.
The complexity of global industrial supply chains exponentially increases their risk. On average, an auto manufacturer has around 250 tier-one suppliers, but the number proliferates to 18,000 across the full value chain. Aerospace manufacturers have an average of 200 tier-one suppliers and 12,000 across all tiers. Finally, technology companies have an average of 125 suppliers in their tier-one group and more than 7,000 across all tiers.
Companies that cannot successfully manage those complex and, at times, opaque supply chains are at high risk, especially if they cannot mitigate the risk of increasing disruptions. Even a short disruption of 30 days or fewer can put 3 to 5 percent of EBITDA margin at stake. Recent research from the McKinsey Global Institute (MGI) has found that as much as 45 percent of one year’s EBITDA1 can be lost each decade because of disruptions.
While we cannot predict exactly when big shocks will occur, we can make a good assessment of their frequency, the severity of their impact, and the time that organizations will have to prepare for different category disruptions, including global crises, surprise catastrophes, anticipated disruptions, and idiosyncratic events (Exhibit 1).
Furthermore, we can prepare for disruptions. Now is the time for organizations to build resilience into their operating models so that they are better prepared for both minor and major disruptions in the future. There is an opportunity to build that resilience on three different fronts, if leaders are willing to take bold action and reimagine their value chain end to end. Opportunities include rethinking business models by shifting focus away from solely selling products and services, moving from a focus on vertical integration to securing control points, and building resilient and efficient industrial supply chains.
An analysis by MGI shows that some organizations are already attempting to improve resiliency, particularly with regard to dual sourcing and holding more inventory. In December 2019, 70 percent of respondents to a major MGI research survey expected to change their globalization and sourcing strategies, with 32 percent planning to move their operations closer to their consumers. In addition, 24 percent expected to diversify their supply chains across countries.
During the COVID-19 crisis, the need for action has elevated in priority. When MGI reconnected with its survey respondents in May 2020, it found that 93 percent of supply-chain leaders were planning to increase resilience and that 44 percent would increase resilience even at the expense of short-term savings.
That trade-off does not need to occur, however: the traditional wisdom that resilience can only be achieved at the cost of productivity and efficiency no longer holds true. Employing a range of digital and analytics solutions, including Industry 4.0 tools, can help achieve resilience balanced on the twin pillars of productivity and flexibility.
Rethink the business model
Companies can rethink their traditional business models to provide continuous or new sources of revenue. Some businesses, particularly those that are currently based on one-off asset sales, can offer subscription-based or pay-by-usage models for machinery and plants. The result? New payment options that turn capital expenditures into operating expenditures, creating a continual revenue stream. For example, a material-handling equipment, warehousing, and material-flow engineering company leveraged technology to expand beyond traditional equipment sales. For customers who preferred limited-term equipment use, a 12-month contract gave them access to equipment via a pay-by-usage model.
Business models based on intellectual-property rights can also provide a basis for new opportunities. Recurring revenue models can be found through either sourcing fees for data standards or using add-on services for primary products.
Would you like to learn more about our Advanced Electronics Practice?
A third option for new business models involves providing access to technology platforms (such as ecosystems for developers based on open systems) and to brokers’ platforms with industrial spot markets that connect third parties (such as those with excess production capacity and the ability to provide services). Data-driven models can use crowdsourced data for the direct monetization of collected data, as seen with a number of large tech players. Insights from collected data can also be indirectly monetized through microsegmentation for pricing and customization.
Secure value-chain competitiveness
Many sectors are seeing rapid disintermediation of their customer relationships. Large technology platforms, now boasting billions of monthly active users, attract businesses seeking to sell to those users—making the platforms even more attractive to the users, all in a virtuous cycle.
One effect of this tech-enabled transformation of customer access and experience is to make outbound supply chains more complex to manage. Another is the potential loss of direct customer connections. Organizations that fail to address key value-chain points often experience difficulties, as illustrated when proprietary data eventually became the de facto standard for entire categories of digital services.
But companies can also protect their customer relationships by taking end-to-end, clean-sheet views of their future value chains to secure competitiveness against potential disintermediation. Taking actions to improve customer access, implement proprietary technology platforms, help set new industry standards, and leverage domain know-how can provide crucial support. Recognizing the potential danger, other players have invested in securing algorithms that build on the same data as competitors, and use the experience curve so that page-rank algorithms can yield better search results. Recommendation engines that leverage scale provide another avenue for designing individual offerings.
Digitize
Another method of building supply-chain resilience is digitization. Several disruptive technologies are accelerating the process. For example, following Moore’s law, a 50 percent reduction every two years in the size of semiconductor process nodes brought them down to five nanometers in 2020 (the rate of reduction has slowed in recent years, however). The computational power used to train the largest artificial-intelligence models has increased twofold every 3.4 months since 2012. Industry 4.0 technologies are also driving big changes in all areas of operations (Exhibit 2).
The value of analytics, as well as the intelligence it provides, is also increasing. Similarly, the cost of Internet of Things nodes, such as security and temperature sensors, has declined dramatically—by 50 percent—and is expected to fall still further. The digitization of manufacturing processes is also providing increased interaction between humans and machines, with sixfold growth expected in the virtual-reality market, resulting in a compound annual growth rate of around 35 percent.
Additionally, there has been an improved digital-to-physical conversion thanks to the greater power of additive manufacturing, often referred to as 3D printing. That includes a 60 percent reduction in cost per part in 3D printing since 1990.
Companies can also rethink their future plant archetypes (Exhibit 3). Smart plants enabled by digitization and automation offer cost-efficient mass production, while customer-centric plants use digital to offer ultraresponsive, single-piece flow and allow for mass customization. Advanced-technology use and manufacturing excellence are underpinned by a digital backbone and agile, lean operations that offer increased flexibility, productivity, and collaboration.
Industry 4.0 technologies, including automation, can also enable new footprint decisions while achieving a similar—or even improved—cost position. The technologies can be applied to manufacturing processes, such as with automated testing and packaging.
Several mature economies show significant potential for the adoption of Industry 4.0 methods and technologies. With comparatively high levels of investment, innovation, and workforce capabilities in these locations, their capital-labor trade-off may look quite different once Industry 4.0 is taken into consideration.
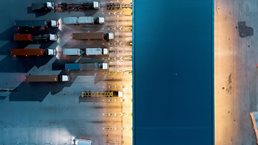
Why now is the time to stress-test your industrial supply chain
We estimate that as much as $4.6 trillion in trade flows may be rebalanced across geographies in the coming years, driven by economic factors such as capital intensity (share of capital compensation in total value), knowledge intensity (percentage of labor force with college degrees), product complexity, and trade-weighted distance (Exhibit 4). Noneconomic factors that influence trade flows may include increased interventions intended to further national security, national competitiveness, and self-sufficiency.
The regionalization of supply chains has already started and could create both risks and opportunities across regions. Changes enabled by Industry 4.0 can deliver results, such as an approximate 65 percent labor-efficiency increase, a 30 to 40 percent unit-cost reduction for manufacturing overhead, a more than 200 percent increase in output, and an approximate 50 percent reduction in quality issues.
Stress-test industrial supply chains—yesterday
Typically, industrial companies have vulnerabilities that are not obvious. Organizations can immediately undertake stress tests of their supply chains to reduce such issues. In a complex, fast-changing, and unpredictable environment, C-level engagement is critical for assessing and mitigating supply-chain vulnerabilities. Recent research on the subject emphasizes that a stress test is an important first step in developing a resilience blueprint.
A general stress test considers five factors: industry attractiveness, corporate resilience, supply-chain exposure, operations exposure, and customer exposure. Its holistic approach allows for comparison both within business units and with competitors. An in-depth look at the global industrial supply chain can identify vulnerabilities at both tier-one and other levels by considering a range of risk factors, such as the density of spend associated with suppliers and geographic locations. An examination of supplier interconnectivity and supply-chain depth can help leaders understand the often-vast expanse of subtier suppliers. For instance, companies may discover that some smaller subtier suppliers are likely to be at risk because of their size or their dependence on a single company. By analyzing the potential for shock exposure and sources of vulnerability, organizations can illuminate unexpected value-chain disruptions that can cause operational and financial impact, and they can understand where they can focus their efforts to reduce overall value-chain risk (Exhibit 5).
For organizations that act now, there is an opportunity to build resilient industrial supply chains. The first big step involves taking the time to understand where potential risks exist. Will your company be one of the first movers?