The fundamentals of the pharma industry remain strong. A growing and aging population with significant unmet needs is creating high demand. New technologies are emerging; these could revolutionize the way new medicines and devices are developed, tested, and marketed, as well as the way pharma companies interact and build relationships with their customers.
But today’s industry also faces considerable headwinds. The outlook for pricing and volume expansion is becoming less attractive across all regions, given sustained pressure on drug pricing in Europe, the growing size and bargaining power of payors in the United States, the looming biologics patent cliff, and mounting competitive pressure in emerging markets. Meanwhile, advances in technology and analytics are opening up opportunities for powerful tech entrants to engage with patients and consumers in radically new ways and to launch innovative healthcare offerings in conjunction with payors and providers. These entrants threaten to disintermediate pharma companies as the primary owners of patient data and take control of their value story. Should that happen, it would have drastic repercussions for pharma’s R&D and commercial models.
Faced with these pressures, pharmaceutical companies have been striving to improve their productivity since the beginning of the new millennium. They scored early success by bringing down selling, general, and administrative (SG&A) expenses between 2004 and 2011, but more recent cost-reduction efforts have yet to reshape the structure of their P&L (Exhibit 1).
While some companies have bucked the trend by achieving more impressive productivity gains, pharma as a whole still has a long way to go to match the progress other industries have made in rethinking the way they operate to cut costs and contain staffing levels (see sidebar, “A tale of two industries”). This holds true regardless of subsector. Big pharma, smaller companies, healthcare conglomerates, and generics manufacturers may have different cost structures, but all have struggled to drive step-change productivity gains. As Exhibit 2 illustrates, the only companies that managed to reduce their average cost of goods sold (COGS) between 2011 and 2014 were those operating in the highly cost-sensitive generics sector. And over the same period, only midcap pharma was able to bring down its SG&A expenses.
Would you like to learn more about our Life Sciences Practice?
Firing up the productivity engine
As the need for higher productivity in pharmaceuticals becomes ever more acute, standard industry responses are losing their effectiveness. The main levers that companies have pulled over the past decade to increase productivity—reinvesting in R&D, reallocating resources to emerging markets, and improving COGS—will not be enough to deliver the scale of improvement that the industry needs to thrive in today’s challenging environment.
Reinvesting in R&D. Over the past five years, pharma companies have refreshed their innovation pipeline, improved their decision making, and reversed their decade-long decline in clinical success rates. A recent Nature article noted, “For the first time since we started analysing such data, cumulative success rates are up in the three years to 2014, compared with the previous three-year period.”1 However, companies will need to commit to significant further investment if this upward trend is to continue. Funding is needed in three areas in particular: developing new capabilities such as advanced analytics to improve R&D effectiveness, capturing the promise of new tools and technologies such as immuno-oncology and gene editing, and reshaping business development and licensing (BD&L) as deals with small start-ups and other external partners become an increasingly common route for accessing innovation.
Reallocating resources to emerging markets. The pharma industry has sought to benefit from faster market growth and lower operating costs by shifting frontline resources from developed to emerging markets, but this strategy has recently received a double blow. Growth rates are slowing, particularly in Brazil, Russia, India, and China, while labor-cost advantages are eroding quickly. In addition, local competitors are eating into market-share gains in many countries.
Improving COGS. Generics companies have led the industry in reducing COGS by optimizing their procurement and manufacturing processes. However, this gain has been offset by a shift to more expensive-to-produce drugs at other pharma companies, leaving COGS flat across the industry as a whole. Future improvements will be difficult to achieve, now that generics manufacturers have exhausted the easy gains. At the same time, originators in small molecules and biologics will come under increasing pressure to reduce costs as competition from biosimilars intensifies.
The recent surge in pharma M&A has also been prompted by the quest for higher productivity, as well as other factors such as increasing specialization. As a recent In Vivo article explained, “This [M&A] boom was fueled partly by the overcapacity that persists throughout the industry, particularly in support and commercial functions.”2 The article notes that the largest deals have declared significant cost synergies even if that was not their chief objective.
As these established levers become less and less effective, we believe the industry urgently needs to find new ways to bring about the next S-curve in pharma productivity.
Toward a systematic approach to productivity improvement
To equip their companies for a rapidly changing pharma landscape, executives need to seize every opportunity to embed productivity in their thinking and incorporate it into every change effort they undertake. As leaders consider their company’s path forward, any improvement program, whether limited and local or broad and far-reaching, should have productivity at its core.
Drawing on recent conversations with a number of pharma CEOs, we have identified six situations that make excellent triggers for executives to drive their productivity agenda (Exhibit 3). Each needs to be handled in a different way. Together the situations represent a full spectrum of possibilities, beginning with functionally focused initiatives at the narrow end of the spectrum and ending with whole-company transformation at the broad end. Our advice to any company facing one of these situations is to make productivity improvement a central plank of its response and to bear in mind lessons learned by other pharma companies as they plan and execute their transformations.
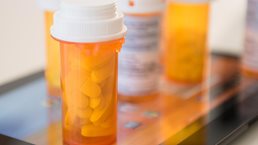
How pharma can win in a digital world
1. Surgical functional intervention
Sometimes companies need to reduce costs or improve productivity in an individual business function such as procurement, clinical operations, supply chain, finance, or HR, with a view to achieving rapid results in a matter of months. These are usually healthy organizations looking to capture incremental benefits from superior clinical operations or back-office functions. For instance, an innovator company may want to optimize its clinical-trial operations by improving its site selection or extending its outsourcing relationships.
To maximize productivity improvement in a functional strike, we recommend executives take several steps:
- Start by creating a clear picture of the function in question. What are its main activities? How does it create value? How does it connect with other functions? How do its practices compare with best practice in other sectors, such as consumer goods or advanced industries? One company we worked with decided to rewire its marketing function to take out 30 percent of the cost base. It started by defining key deliverables and reallocating roles and responsibilities between global, regional, and local marketing to reduce duplication between layers and cut any noncritical activities. The company exceeded its target savings and was able to reinvest in the marketing capabilities it needed for future success.
- Map out which activities are truly mission critical and should be kept in house and which can be outsourced. Similarly, identify which capabilities are needed to carry out these activities, and find ways to ring-fence them. After reorganizing, one company added so many reporting and controlling demands that it ended up with a finance function twice the size of its peers’. By challenging the scale and granularity of reporting and delegating preparatory work to a low-cost shared-services center, the company was able to improve productivity in the function by 30 to 40 percent.
- Ensure that the transformation is run by a capable and dedicated team and is visible enough to senior leadership that it doesn’t disappear into a functional silo. Successful pharma transformations strike a fine balance between making local line leaders accountable for results and providing support from the center. Senior leaders must have a clear view of performance and support local teams in finding the best path forward. The most successful transformation programs are those that focus on improving efficiency and effectiveness at the same time.
2. Business-unit turnaround
Sometimes a company has broadly successful operations but feels that one of its business units needs improvement. Perhaps its performance is weak in a certain therapeutic area, or its sales force needs to be more responsive to changing market needs. This kind of effort is usually confined to the business unit itself and has little or no effect on the rest of the business. It typically addresses one or two specific objectives over about six months to two years.
In our experience, a few efforts are important for companies tackling such a situation:
- Set ambitious productivity targets, and ensure they’re fully supported by the board or corporate center. For the best results, corporate leaders need to summon the courage to take radical steps. One deep cut is preferable to a long series of salami slices, because it allows the unit to complete its transition much more quickly.
- Lay out a vision for the future of the business unit to ensure it is not alienated from the rest of the business. One company separated a unit from the rest of the organization without explaining what would happen to it. Speculation spread that it was destined for a sell-off, and staff became disengaged. Even though the company did not actually sell the unit, the uncertainty and poor morale caused its performance to falter. That could have been avoided if the company had set out a clear vision for the unit from the start.
- Keep energy levels high, and minimize the drag on other parts of the business by ensuring the turnaround does not spill over into other business units that are performing well. The management team of the affected unit needs to own a big portion of its P&L, not just its cost centers. Locate full accountability with the unit, and charge its management with turning the business around and achieving a target for earnings before interest, taxes, depreciation, and amortization. Make it clear that any failure will have serious consequences, such as the sale of the unit.
3. ‘Good to great’ transformation
Every so often, we encounter a pharma company that is striving to move from good to a best-in-class standard. Unlike the companies in the previous examples, it isn’t trying to fix the basics—which are already in good shape—but instead seeks to improve its costs and revenues by using more sophisticated levers, such as advanced analytics to raise R&D productivity, or advanced segmentation to identify priority customers. This more ambitious type of transformation tends to take longer, perhaps one to three years.
Companies can best improve their productivity in this situation by doing a few things:
- Communicate the rationale for change to everyone in the organization, check that it is widely understood, and foster a sense of ownership for the effort. Building a solid fact base that identifies sources of waste and areas where productivity gains are needed—and realistically can be captured—will help to minimize disruption in the business and forestall any impression that leaders are pursuing change for its own sake.
- Compensate for the lack of a burning platform to motivate the organization by creating and articulating a clear vision based on how the industry is likely to develop and what the company’s new operating model will look like. The vision should include a carefully calibrated level of ambition to energize the organization. One pharma company we worked with explained to its staff that it was changing the way it operated not because its performance was lacking but because it sought to become a partner to the health system. Since many employees had joined the company because they wanted to create a better world, the introduction of a vision that was in tune with their aspirations deepened their sense of ownership and increased engagement throughout the organization.
- Build success stories early on, and share them widely in the organization. One large pharma company had a specialty business unit with a strong pipeline and great performance in general, but a mixed record for drug launches. To improve its capabilities, the company selected a handful of launches in different countries and used them to pilot innovative new approaches. By communicating the success stories and explaining how they could be scaled up, leaders were able to combat skepticism about the transformation and energize the organization.
4. Event-triggered transformation
Some transformations come about as the result of an external event, typically a merger or acquisition or the intervention of activist investors.
The recent boom in M&A in the pharma industry is partly the result of attempts to address short-term productivity challenges. An acquiring or merging company typically designs organization-wide integration programs to capture synergies, especially in costs. Such programs usually take up to three years to complete and deliver results.
Pharma has also seen a rise in shareholder activism in the past few years. Although companies often regard them as antagonists, activist investors can prompt positive action that brings benefits in both strategy and long-term value creation.
A couple of efforts can help companies make sure they capture the full scope of productivity improvements during integration programs:
- Develop a clear vision of what the merged entity should look like and what productivity gains can be achieved. In discussions with partners—whether newly merged entities or activist investors—they should address productivity issues with an open and collaborative mind-set. McKinsey analysis shows that reaching agreement with activists tends to lead to higher shareholder returns over a three-year time horizon.
- Use the merger or acquisition as an opportunity to capture efficiencies across the whole business. One pharma company that went through a very large merger found this out the hard way. Relying on overoptimistic growth synergies, it decided only to address back-office savings, not front-office opportunities. This left inefficiencies in place, and when increased austerity measures in Europe caused a market slowdown, the company had to go through a series of further restructurings to finish the job.
5. Digital transformation
Over the past decade, more and more companies have turned to digitization and automation to streamline and speed up their processes and to capture efficiency and productivity gains. These efforts generally cut across functions, involve rethinking entire processes from end to end, and deliver results quickly, within three months to a year. They are undertaken for a wide range of reasons, from reducing the cost base to improving agility or creating a superior customer experience.
Companies can take a few measures to gain the maximum benefits in these circumstances:
- Apply an agile, iterative test-and-learn approach, rather than running long and expensive development processes to concoct the perfect solution. One specialty-pharma company we worked with set up a stand-alone unit to develop digital solutions for patient engagement and new customer-interaction models. The unit was designed to have a start-up culture and an innovation process that took an idea to minimum viable product in no more than 100 days.
- Roll out the new process by incorporating it into existing business processes so that the company can start operating in the new way as soon as possible. The specialty-pharma company deliberately kept its new unit separate from the existing organization but located it in the same city so the two could be in regular contact. In addition, the company set up an advisory board that not only guides the start-up but also exposes company executives to new ideas.
- Set up business-led, customer-centric transformation teams staffed with A-grade talent. In reworking its customer-interaction model, the specialty-pharma company ensured that its idea-generation sessions were led not by IT (though the group was closely involved) but by sales, because this function had the deepest insight into what customers value. Later in the process, the fact that sales leaders took visible ownership of the new interaction model helped increase buy-in among frontline employees.
6. Extreme makeover
When a company commits to rethinking its strategic direction and embracing a new vision, culture, and way of doing business, improving productivity will usually be central to the effort. A total transformation is often undertaken in response to a crisis or financial distress—circumstances where the organization needs to act fast to improve its performance immediately. It will strive to achieve results in as little as three to six months so that it can demonstrate its ability to turn the situation around, save money to fund later stages of the transformation, and build momentum and conviction in the organization for broad, long-lasting change.
To keep productivity central to the effort, companies in this situation should home in on a few areas:
- Articulate a clear change story that does not focus exclusively on the immediate crisis but acknowledges the organization’s strengths. It is important to remind people of what unites them, what they can be proud of, and why they have what it takes to go through a difficult transformation.
- Set targets by taking an independent, clean-sheet approach to encourage more radical thinking. Leaders are often preoccupied with last year’s performance and confine their strategy to cutting back on the current model. Starting from scratch forces them to set a new level of ambition that goes beyond what seems possible today. Our experience supporting businesses with transformations indicates that such an approach typically identifies two or three times more potential impact than that suggested by an initial internal assessment.
- Never underestimate the importance of the “soft” skills. In interviews with industry leaders, we found that four practices in particular make a transformation more likely to succeed: communicating openly, leading by example, engaging employees, and fostering continuous improvement.
As the productivity imperative in pharmaceuticals looms ever larger, now is the time for companies to think through their strategic options. In particular, leaders facing any of the six situations described here should put productivity at the heart of any change program or improvement agenda they undertake.
The best practices outlined for these situations are intended not as a comprehensive checklist but as a starting point for discussion. To be sure, these are conversations worth having. A healthy, productive pharmaceuticals industry benefits the whole world.