Worldwide mining operations are as much as 28 percent less productive today than a decade ago, according to new McKinsey research. The results from McKinsey’s new MineLens Productivity Index (MPI), which adjusts for declining ore grades and mine cost inflation, show that the pronounced decline in productivity is evident across different commodities and is seen in most mining players and geographies.
Compared with industries such as automotive, which obsessively focus on productivity gains, the numbers seem astonishing. Nevertheless, the decline may be less surprising when we take into account the fact that the industry has just ridden a demand supercycle and has succeeded in expanding production of certain major commodities by 50 percent or more over the past decade.
What is clear is that with the collapse in mining profitability over the past three years, the industry is seeking once more to raise productivity. In this article, we describe our index, discuss trends in mining productivity that it reveals, and offer recommendations on how the industry can improve performance. Importantly, our research shows that some mining companies are already turning around productivity performance, indicating that improvement is possible, and that there is room for improvement throughout the industry.
Wanted: A better measure of productivity performance in mining
The surge in demand for metals and minerals in the early 2000s quickly translated into much higher prices and, with it, much increased miners’ profitability. Boosting production volumes became the industry’s top priority. Mining companies worldwide largely lost sight of productivity goals that had underpinned operating discipline in the lean years of the 1980s and 1990s, when parts of the industry had set a healthy record in productivity improvement (Exhibit 1). As the demand boom gathered pace, cost increases related to expanding production got badly out of control.
The industry’s circumstances have now changed. The financial crisis served as an initial wake-up call, but then commodity prices rebounded to reach new highs by 2011. Today, the industry finds itself in new territory, following the slowdown in demand growth over the past four years and consequent fall in prices and mining profits.
There is intense interest across the industry in reversing the excesses of the 2000s. Miners are seeking to cut costs incurred to produce mining output, or to increase output at no additional cost—in other words, to raise productivity. CEOs have been acknowledging to investors that poor productivity performance must be addressed. Meantime, governments in big mining countries are also trying to understand the productivity challenge, with publicly funded research institutions studying the issue closely.
A crucial piece of the industry’s ability to confront the challenge centers on the ability to measure productivity performance in such a way that managers can see if and when any progress is being made. Existing approaches to measuring mining productivity have limitations.
Industry managers have focused on labor productivity, typically measured in terms of the final product output—not the total material moved—per person employed. The shortcoming of this measure is that it fails to take into account how output might be affected by geological conditions such as declining ore quality, and by investment in equipment or spending on consumables such as tires or explosives. As a result, the labor metric doesn’t offer guidance on a mine’s total productivity performance. Similarly, the overall equipment effectiveness (OEE) metric—commonly calculated from dispatch data about equipment operating time and delays—provides important insights about availability, utilization, and tempo performance, but is focused on component parts of the operation such as shovels or a processing plant, rather than the whole operation.
Economists have also applied more advanced metrics such as total factor productivity (TFP). But the TFP approach measures output in terms of value added, and so is handicapped in two important areas: it is influenced by changes in geological conditions such as ore-grade quality, and it is affected by commodity prices, which are constantly moving. Mining companies cannot control these two areas, so changes in TFP performance do not fully reflect operational performance and productivity.
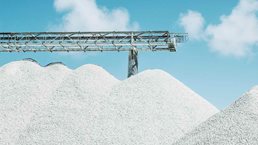
Would you like to learn more about our Metals & Mining practice?
A new way to measure productivity in mining operations
Put simply, the industry needs a methodology to help managers understand whether or not they are improving their performance at breaking and moving rock. To that end, we have developed a metric—the MineLens Productivity Index (MPI)—that enables mining managers to measure the aspects of productivity that are within their control.
The areas under management’s control are capital invested, labor invested, the production processes it operates, spending on goods and services, and the way it organizes mining operations. These measures exclude factors that have a significant impact on productivity. Probably the most important are the variable nature of ore grades and the depth of the ore body. These worsen and deepen as a mine is exploited, leading to rising extraction costs and falling output. Given that mining companies typically measure the output of the actual ore being mined, rather than the total material moved, productivity measured in this way tends to be constantly in decline. Another important factor concerns more extensive regulatory requirements across the industry worldwide; these can directly or indirectly affect productivity but, again, lie largely outside management’s control.
Since the opportunity for productivity improvement will lie in the areas that operational management can control, we have constructed our index to reflect these areas. Accordingly, MPI focuses on capital, labor, and nonlabor operating expenditure. We have deliberately excluded ore grade from the calculation. The three elements are then linked with a measure of physical mine output, which is not affected by changes in the ore grade and stripping ratio. The basis for MPI is the well-established Cobb-Douglas production-function equation used to measure productivity in national economies, which we have modified in such a way that it can measure the productivity of mining operations (see sidebar “Introducing the MineLens Productivity Index”).
Collecting data from individual mines on each of the four elements makes it possible to track how productivity has evolved and how the elements affect a mine’s performance over time. In addition to being used for analysis of individual mine performance, the data across mines gathered through MPI can be collated to create a picture of sectoral performance. It is also possible to apply the same MPI analysis to identify trends in productivity across a whole country’s mining sector (see sidebar “Case study of Australia’s productivity trend”).
Time to face the facts!
What do the data show? In brief, that the industry has paid a high price in terms of lower productivity for volume gains during the demand boom—but that there are signs the industry may be starting to turn its productivity performance around.
Over the past decade, mining productivity as measured by MPI has declined 3.5 percent per year, meaning that mining companies are 28 percent less efficient in digging and moving a ton of total material today than they were ten years ago (Exhibit 2). The pronounced decline in productivity is evident across different commodities, including copper, iron ore, coal, and platinum group metals (Exhibit 3). It is also in evidence across most mining players and all the major mining geographies (Exhibit 4). This decline stands after adjusting for external factors such as deteriorating ore grades and mine cost inflation, including escalations in the prices of mine inputs such as fuel and explosives. It is important to note that the productivity decline would be even more pronounced if no adjustment had been made for ore-grade deterioration.
Somewhat more encouraging signs start to emerge, however, when the MPI trend is separated into the two distinct phases of the mining industry’s recent history—before and after 2009—as is also shown in Exhibit 2. The MPI data suggest that over the 2009–13 period, the industry has more or less stabilized the downward trend in productivity, with MPI running on average at only –0.4 percent a year. The productivity data also registered a rebound in some commodities in the 2012–13 period.
Which factors that make up the MPI have had the greatest impact on productivity trends? Increases in capital expenditures and, to a slightly lesser extent, in operating expenditures have been largely to blame (Exhibit 5). Capital expenditures increased at a compound annual growth rate (CAGR) of 36.8 percent from 2004 to 2013, and operating expenditures at a CAGR of 18.1 percent in the same period. The number of workers also has risen, at a CAGR of 6.6 percent over the full period. In the population of mines that we have included in MPI, output has grown at a CAGR of 14.8 percent.
Evaluating individual mine performance
For individual mines, productivity performance as shown by the MPI data can also provide useful insights. Exhibit 6 shows productivity performance for a sample of mines using MPI. The four quadrants represent the evolution of performance (from a base in 2008) in terms of unit costs and output, with the green quadrant representing the most desirable outcome—lower unit costs and higher output per employee. The evolution of the mine’s asset value since 2008 is represented by the size of the bubble. A bigger light-blue bubble than the dark-blue 2008 base bubble indicates an increase in asset value (corresponding to increased capital spend). A smaller bubble indicates lower capital spend.
A mine that has improved in all four elements of productivity that underpin MPI—labor, capital expenditure, nonlabor operating costs, and production volumes—will move from its starting position (as shown by the dark-blue bubble) into the green quadrant, and the bubble size will be the same size or smaller than in 2008. Such a mine will have reduced unit costs and raised output per employee without increasing its capital expenditures. This has represented a difficult challenge for mines since 2008: none of the mines in the sample studied have succeeded in moving into this quadrant.
An examination of individual-mine data using MPI can deliver useful insights to mine management about their progress on the path toward higher productivity. A South American copper mine made significant capital expenditures to boost its production and saw output rise 3.9 percent per year (Exhibit 7). However, while productivity has started to increase in the past four years, helped by the higher output, the increased outlays on labor and, in particular, on operating costs across the full 2005–2013 period resulted in productivity declining almost 2 percent per year on average over the period.
Addressing the industry’s productivity challenge
What is the way forward? To address the challenge of productivity improvement, miners will need to make moves on two levels: first to achieve short-term gains, and second to set their operations on the right course for higher long-run productivity performance.
On the first level, the way forward is clear. Our research identifies that capital expenditures and nonlabor operating expenditures have been the main drivers of the productivity decline. Clearly, the industry has already started to work on this, with many companies already reining in capital expenditures and making moves to obtain more value-adding output from their asset base. Work also needs to continue on lowering nonlabor operating expenditures, notably by improving procurement performance. Indeed, the improvements that are already starting to be seen in the MPI data point the way, with an upturn in productivity performance in some regions where capital expenditures have been reduced dramatically and where a number of large assets have come online and boosted output, while major efforts have been undertaken to drive costs out in operations.
Discover how MineLens can provide data and insights to optimize mining productivity
Moving to the second level of actions, we see three important areas of focus to address the root causes of productivity decline.
Embed effective management operating systems at mines. Doing this will create greater transparency on operations performance. The operating systems should also free up people and resources to prioritize productivity and operational excellence, and support effective performance management. This approach will help resolve an important challenge that the industry has struggled with: making productivity performance (and its measurement) a priority. There has typically been a focus on improving one or two of the variables, such as reducing cost, lowering capital intensity, or increasing throughput. But a holistic focus on the drivers of productivity that is shared at multiple levels is rare in mining organizations.
Prioritize operational excellence and capabilities development. Operational excellence implies a continuous focus on improvement and enables ongoing cost reduction and throughput improvement. To do this requires a determined focus on eliminating all forms of waste, reducing variability, and improving productivity of assets through advanced reliability and maintenance approaches, together with increased flexibility about changing conditions. Many mining companies struggle with capabilities constraints and need to address them: building up the capabilities of individuals and of the organization is a necessity for companies to be able to deliver on all the levers involved in productivity improvement.
Talent is needed not only, for example, to achieve world-class levels of waste elimination and flexibility in operations, but also to be able to make progress on productivity. Many mining companies still consider operational productivity improvement to be the domain of a “continuous improvement” department or a handful of Lean experts or Six Sigma black belts, but do not yet regard it as a core competence.
Focus on innovation. It is perhaps understandable for an industry that has been asked to break production records year after year in the past decade to prefer to stay with what has always worked, rather than risk an interruption in output, but the industry’s rate of innovation and adoption of breakthrough technologies was generally slow even before the supercycle. For example, the potential to implement advanced dispatching processes in underground mining operations is clear, but it has still not been adopted at scale. With a few notable exceptions, it’s also unclear who is mandated to drive innovation in many mining companies. And, in many cases, new capital projects are executed without integrating new technologies into the mine design.
Mining-company management should encourage openness to trying new approaches and to adopting new technologies. At the same time, mining companies should use advanced analytics to harness the potential of the vast amounts of data generated in typical modern mining operations in order to boost productivity-improvement initiatives. To make this happen will require a broadening of the expectations of what operations leaders are responsible for, and tighter integration with other corporate functions. It will also necessitate looking beyond the boundaries of the mining industry to seek inspiration from other industries’ successes. Partnering between mining companies and equipment and technology providers should also increase, so innovation in mining can succeed more broadly.
Mining commodity prices are volatile, and investors are currently unenthusiastic about the industry’s prospects. Nevertheless, we think the long-term supply-demand fundamentals of many important mining commodities suggest that companies that can cost-effectively raise their output will be rewarded. This means that the companies able to succeed in the race to achieve higher productivity will be among the biggest winners. The initiatives described here are important enablers of those productivity improvements. Combined with a commitment to monitor productivity performance, they will be an important factor in that race.