The semiconductor supply chain stretches from fabs to back-end factories, with the intricate process of chip manufacturing sometimes requiring four to six months to complete. At the end of the line, some of the world’s leading companies are waiting for the semiconductors required to launch their latest innovations. Any delays could alienate distributors and end customers, placing a semiconductor company on an unofficial blacklist. So why are late shipments so common?
Stay current on your favorite topics
Most players can’t answer this question. Although they’re aware that their supply chains are suboptimal, they generally look at different outcomes in isolation, including the portion of on-time deliveries (OTDs), overall cycle times, fill rates, excessive days of inventory, or the number of orders canceled because of delays. The reasons behind their poor performance receive much less scrutiny, partly because it’s difficult to pinpoint when and where problems occurred along the lengthy and complex supply chain. And that means the same mistakes get repeated each time a company gets a new order.
A new and comprehensive metric can provide detailed insights into the end-to-end performance of the supply chain. For each order, it asks several questions: Were demand forecasts accurate, allowing companies to deliver the right product (RP)? Did execution occur on schedule, allowing all tasks to be completed at the right time (RT)? Was inventory staged along the supply chain at the right locations (RL)? This metric—abbreviated as RPRTRL—is calculated based on hard data, resulting in an objective assessment of supply-chain performance. With the insights that the RPRTRL measurement provides, companies can, for the first time, identify all root causes behind performance issues, develop an improvement plan, and quantify their progress.
On-time delivery—a priority for customers
When it comes to customer retention, supply-chain performance matters. That much became clear when we asked managers at six major semiconductor customers and distributors to rate the factors that influenced their purchase decisions on a scale of one to ten, with ten being the most influential. Product specifications, which include quality and features, ranked first at 9.7, but OTD tied price for second, at 8.2 (Exhibit 1).
Interview subjects frequently noted that they gave preference to semiconductor companies with a strong OTD record. One said, “For suppliers with good delivery performance, we invest more, as we feel more comfortable that we can deliver the products to our own customers.” Another remarked, “If a supplier consistently can’t meet delivery dates, we will stock them in reaction to customer orders but not actively push their sales.”
Our analysis of one semiconductor company revealed the dire consequences of late deliveries. For customers at which its OTD rate was between 0 percent and 40 percent, the semiconductor company’s revenue dropped 28 percent within one year. When the semiconductor company’s OTD rate was 80 percent or higher, its revenue declined only 2 percent over the same period. These findings suggest that supply-chain inefficiencies are a major cause of customer churn.
What’s behind the low OTD rates? The root causes are as complex as the supply chain itself. When semiconductor companies receive an order, they have chips at every stage of the supply chain, with some undergoing front-end processing, others in die-bank or back-end processing, and the remainder sitting in warehouses as finished goods. Likewise, the lead times for orders may vary, with some customers expecting quick shipments and others requesting deliveries along a more relaxed timeline. All too often, however, semiconductor companies discover that the requested lead time is shorter than the cycle time needed to fulfill the order.
Would you like to learn more about our Semiconductors Practice?
Most missteps that lead to late deliveries relate to one of three areas: forecasting, execution, and inventory (Exhibit 2). For instance, if the order lead time is shorter than the three to four weeks required for back-end processing, a semiconductor company must have sufficient finished-goods inventory to meet the target delivery date. But many players inaccurately forecast future demand and don’t have enough finished goods in stock when such requests arrive.
A comprehensive metric for assessing supply-chain performance
The three elements of the RPRTRL metric allow companies to quantify their performance in forecasting, execution, and inventory management (Exhibit 3). Companies must evaluate these elements for every product ordered, to ensure that the overall metric reflects the most up-to-date information.
Right product
If companies can’t predict when products will be needed, it doesn’t matter whether the rest of their supply chain is efficient. They simply won’t be able to fulfill orders, or they’ll have excessive inventory because they make more products than they need. The right-product component of RPRTRL measures how companies perform in this area by calculating the extent of a company’s forecasting bias (the arithmetic mean of a forecasting error) and the magnitude of the forecasting error (the sum of mistakes on all orders).
Companies that score low on the right-product component will need to reexamine their forecasting methods to determine if they are making decisions based on insufficient or flawed information. For instance, companies may only look at past-order data to forecast demand, even if they have other information that provides important clues about future trends, such as customer financial statements, the number of web-page views for certain product parts, and data-sheet downloads for different products on their website. Some companies also encounter problems because they use the same forecasting model for all SKUs, which can lead to inaccuracies. If a product has intermittent spikes in demand, it needs a different model than does a product with low but steady demand.
Right time
The right-time component focuses on how well companies execute orders once they are received—basically, it evaluates whether a company is completing all tasks, including those related to fab operations, sorting, assembly, and testing, within the expected time frame. The right-time score is computed by determining the volume-weighted percentage of individual tasks for which the actual cycle time was shorter than or equal to the planned cycle time, in both back-end and front-end processing. This calculation provides more insights than current methods for measuring execution performance, which typically involve looking at overall cycle times and determining the percentage of orders with delays.
If companies score low on the right-time component, they should review their production-management processes, including those related to vendors. For instance, foundry and back-end-process partners may not provide daily updates on progress, so semiconductor companies don’t learn about delays until it’s too late to address them. In other cases, companies may not use all available vendor capacity or may fail to manage their priorities. As one example, companies might not accelerate production for “hot lots”—those that need to enter production quickly because timelines will be tight.
Right location
Are inventory levels sufficient at all locations along the supply chain, including die banks and warehouses for finished goods? Many companies can’t answer this question because their current inventory systems haven’t been properly tested or implemented. All too often, they just consider average supply and demand, rather than examining the factors that might change these variables.
Companies could gain better insights about inventory by calculating their right-location score, which measures the percentage of orders for which they had enough inventory to satisfy demand, weighted by volume, for each part. All orders are grouped into buckets based on lead time. For instance, a company might receive an order for which the lead time is shorter than the back-end cycle time. In this case, the right-location score would be determined by calculating whether there was enough finished-goods inventory for the order. If the lead time was longer than the back-end cycle time but shorter than the full cycle time, the right-location score would be based on whether the company had sufficient inventory in the die bank.
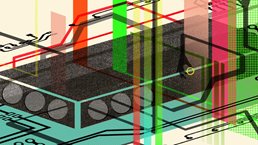
Reimagining fabs: Advanced analytics in semiconductor manufacturing
Companies may score low on this component if they stage inventory at the wrong locations or their finished-goods inventories are too low to fill the orders that have short lead times. In addition to delaying OTD, incorrect staging can create a surplus at the finished-goods and die-bank stages, resulting in higher inventory costs.
In many cases, a right-location analysis will reveal that inventory requirements vary significantly by stage. For instance, one semiconductor company received many orders for which lead times were shorter than back-end cycle times. It could only achieve an OTD rate of more than 80 percent (a best-practice figure) when it had enough finished-goods inventory to satisfy projected demand for at least 91 to 120 days (Exhibit 4). When the order lead time was longer than or equal to the back-end cycle time, the company could draw on its die-bank inventory to satisfy the order. In such cases, it achieved an OTD rate of more than 80 percent only when it had enough die-bank inventory to satisfy projected demand for the next 16 to 30 days. Unfortunately, the company seldom had die-bank or finished-goods inventory at that level.
Calculating RPRTRL scores
To compute the RPRTRL metric, companies calculate separate scores for each component: right product, right time, and right location (Exhibit 5). These scores are then multiplied to determine the total RPRTRL score. For the initial computation, companies typically use anywhere from one to two years’ worth of data. To measure progress, they should recalculate RPRTRL at monthly or weekly intervals (when they have sufficient data).
The total RPRTRL score will range from zero to one. In our benchmark analysis of semiconductor companies, the best-in-class players had an RPRTRL score in the range of 0.6 to 0.7. The average semiconductor company scores 0.3. The key question for all semiconductor executives is this: Do you know your RPRTRL score?
Calculating an RPRTRL score provides valuable insights, but it’s just the first step in any supply-chain transformation. Companies must then assess the costs and benefits of addressing each problem before developing appropriate solutions. Since supply-chain issues will vary, companies must develop customized strategies for improving forecasting accuracy, execution, and inventory management. Some might get the most benefit from improved vendor management, for instance, while others gain by adopting new predictive data sets that decrease forecasting errors. But in all cases, the RPRTRL metric will provide a common view of the supply chain that helps all groups deploy a coordinated response. That alone will provide invaluable assistance.