The transportation industry is under pressure to rapidly decarbonize. Regulatory changes, as well as B2B and B2C customers’ demands for greener transportation value chains, are prompting the industry to adapt. In short-haul freight, battery electric vehicles (BEVs)—namely trucks and vans—are already reaching total cost of ownership (TCO) parity in the first use cases, helping simplify the transition for fleets. This is enabled by both rapidly declining battery costs and the launch of new vehicles, including purpose-built battery electric delivery vans.
However, the picture is quite different for long-haul trucking. Long distances, unpredictable routes, high uptime requirements, strict driving-time regulations, and the importance of high payloads have made this sector particularly hard to decarbonize. With current energy densities, batteries are too heavy, charging speeds are too slow, and infrastructure is not yet available to directly electrify trucks on particularly challenging routes.
As a result, long-haul trucking has focused on hydrogen-powered fuel and hydrogen combustion, which are attractive for two reasons. For one, faster refueling and greater range can increase the uptime potential for trucks; furthermore, their lower weight compared with batteries can increase payload capacity. Together, these factors improve hydrogen trucks’ TCO, which is the KPI that the highly competitive transportation industry needs to manage.
The hydrogen opportunity
Hydrogen is the required link and a leading opportunity to decarbonize hard-to-abate sectors. As an example, some industrial sectors (such as steel, cement, or refineries) are hard to abate directly with electricity due to practical technological reasons, while others (such as marine, aviation, rail, or mining) consume energy in quantities that exceed what batteries can provide. These factors will drive adoption of hydrogen irrespective of the transport industry and will ensure that clean hydrogen is readily available.
With this in mind, hydrogen is available in the near term for the right use cases, such as for fleets with their own depots or in Switzerland, where fuel cell trucks are already successfully deployed. There are also clear benefits for both vehicles and underlying infrastructure.
Over the coming years, we expect to see a significant increase in the number of hydrogen-powered vehicles on the road. Although passenger cars will also contribute to hydrogen consumption and have previously been the focus segment, in the future, around 95 percent of demand by volume will come from commercial vehicles. Exceptions include Japan and South Korea, where hydrogen for passenger cars is receiving strong support and where domestic OEMs are at the forefront of the development of fuel cell electric vehicles (FCEVs). By 2035, as many as 850,000 hydrogen-fueled medium- and heavy-duty trucks (MDTs/HDTs) could be on the road in Europe. Between them, they would consume 6,900 metric kilotons of hydrogen per year and require up to 4,800 hydrogen refueling stations (HRS) (Exhibit 1).
Would you like to learn more about our Global Infrastructure Initiative?
Ramping up hydrogen infrastructure
In the coming years, there will be a significant increase in hydrogen-powered vehicles on the road, including fuel cell trucks. Unlike batteries, which directly store electrons to power electric motors, fuel cell trucks use tanks to store energy in the form of molecules in gaseous or liquid form. In fuel cell trucks, hydrogen is converted into electrons and water, with the electrons powering the truck’s electric motors. In hydrogen combustion trucks, hydrogen is burned in combustion engines, similar to diesel. The required hydrogen can be created in different ways—either by reforming natural gas and capturing CO2 or through electrolysis, which is the process of using electricity to separate hydrogen from oxygen.
The technology required for these trucks and to generate hydrogen is already well developed and being deployed. Instead, hydrogen infrastructure is often considered the major bottleneck to adoption. And it is true: hydrogen refueling stations are not ubiquitous today. Each station requires considerable investment, and a value chain supplying hydrogen is also required.
However, besides the vehicle benefits, hydrogen also benefits the infrastructure side. Hydrogen is already taking off in other industries irrespective of transport, leading to the derisking of investments in hydrogen production and transport. At scale, the infrastructure is less costly to create than e-truck charging infrastructure because it does not require grid upgrades and has a smaller carbon footprint. The faster refueling speed means the hydrogen infrastructure can be used by many more trucks than charging infrastructure.
As such, the business case for hydrogen infrastructure is becoming increasingly attractive as hydrogen sourcing costs decline and vehicle demand increases. Our research shows that operators of HRS could reach break-even by as early as 2025 when serving a small fleet of trucks. Specifically, a medium-size HRS with a daily capacity of 500 kilograms (kg) could reach break-even prices at 55 percent utilization, depending on the hydrogen sourcing costs and sales prices (Exhibit 2). In this case, seven long-haul HDTs would be sufficient to provide the required demand for this station.
Compared with storing energy in batteries, hydrogen-fueled trucks can refuel faster and carry a lower weight penalty because tanks weigh considerably less than batteries. Operationally, hydrogen trucks can therefore be deployed on a similar scale with diesel trucks but with the benefit of producing no emissions. This means that they will be cheaper to operate in the long term than diesel trucks. By 2030, the TCO to operate an HDT traveling 500 kilometers per day in Europe is estimated to reach €1.13 per kilometer for diesel, €1.03 for battery electric trucks, and €1.02 for fuel cell trucks.
That said, a number of challenges must be overcome before hydrogen refueling infrastructure can reach scale. To begin, there is limited perspective on the cost development for hydrogen trucking overall and for infrastructure specifically. The timing for ramping up the infrastructure to support long-haul hydrogen trucking is not yet fully clear, and business models need to be developed to support this ramp-up. Infrastructure providers and operators also need to decide whether to concentrate on truck-focused infrastructure or to plan for dual use with passenger cars. Finally, liquid and gaseous hydrogen require partly different infrastructure, resulting in competition between the two.
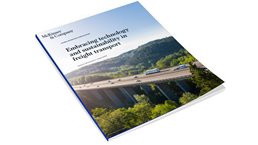
Voices on Infrastructure: Embracing technology & sustainability in freight transport
Building the hydrogen ecosystem
To address these challenges and derisk infrastructure investments, hydrogen infrastructure operators should build an ecosystem that secures supply and demand. That said, accessing funding can be challenging because of the unique nature of investments in hydrogen refueling infrastructure. When compared with traditional mobility infrastructure investments, such as roads, the returns are less certain. And compared with other higher-risk investments in new technologies, the returns are likely lower and will take longer to materialize given the initial capital expenditure to create the infrastructure.
The following example illustrates what this ecosystem could look like for a fleet with 50 FCEV HDTs at three depots, as well as which partners would be required to develop and operate the system:
- A fleet to ensure offtake. This requires the operator to commit to purchasing trucks. In this case, we assume the fleet will operate 50 FCEVs.
- An OEM or retrofitter to provide vehicles. Today, Hyundai is the only OEM providing hydrogen trucks at scale, with retrofitters providing an alternative route by replacing vehicles’ diesel powertrains with e-powertrains and fuel cells, or hydrogen combustion engines.
- A hydrogen producer to ensure provision of low-carbon fuel. This requires further electrolysis capacity to be built. Assuming the trucks run an average of 500 kilometers per day, consuming around eight kg per 100 kilometers, the fleet would require 2,000 kg of hydrogen per day, with slightly higher total production to offset losses during transport, storage, and dispensing.
- HRS infrastructure providers to build refueling stations. In this case, the fleet would likely operate two 1,000 kg HRS at their main depots and one 500 kg HRS at their smaller depot, thereby providing a gross capacity of 2,500 kg per day.
- A financing player to provide capital for expansion. The total cost for 50 FCEVs and three HRS would be between €10 million and €15 million at 2030 prices.
- Governments and regulators to create a stable legal framework and subsidies. This includes targeted support for capital expenditures and operational expenditures for vehicles and infrastructure.
Given the potential benefits and hydrogen’s expected growth, the transport industry should prepare for a hydrogen-powered future. As vehicle production and demand increase— especially from 2025 onward, when more vehicles become available—so, too, will the demand for hydrogen production and refueling infrastructure.
This article is part of Global Infrastructure Initiative’s Voices on Infrastructure.