With myriad digital technologies offering the potential to boost operational performance at incumbent companies in every sector, leaders can find it difficult to decide where to place their bets. For manufacturers, one area of investment is clear: the Industrial Internet of Things. Also known as IIoT and Industry 4.0, this technology holds the key to unlocking drastic reductions in downtimes, new business models, and a better customer experience.
The COVID-19 pandemic has highlighted how IIoT can also enhance organizational resilience in the face of catastrophic events. Digital management tools and connectivity, for example, have enabled companies to react to market changes faster and more efficiently by allowing quick adjustments to production capacity while also supporting remote operations when access to a facility is hindered.
Many manufacturing organizations are already piloting digital initiatives in IIoT. Yet, despite tailwinds from declining compute power costs and improvements in IIoT integration, connectivity, and platform usability and management, few manufacturers have successfully scaled up their IIoT-enabled use cases in a way that achieves significant operational or financial benefits.
A combination of technical and organizational challenges are often to blame. On the technical side, many organizations are still dealing with age-old problems, such as how to wrangle with heterogeneous systems and application landscapes or how to determine which functions (for example, supply-chain management, manufacturing operations management, plant maintenance, or asset management) should be supported by which applications and technical systems (for example, enterprise resource planning or IIoT platforms). There is also the question of where those systems should be deployed—on the edge, at the manufacturing site, or in the cloud—a question that is rooted in the governance between IT and operational technology (OT), plants, and corporate functions.
On the organizational side, companies often fail to modify business processes or optimize IIoT solutions to enable broader application, leaving significant value on the table. People and processes must shift to capture the benefits of the data-driven insights IIoT can generate and maximize the technology’s value. This requires the commitment of leadership to ensure that IIoT is not simply an IT or OT initiative but, rather, an organization-wide effort.
To understand the key enablers behind IIoT-based value capture at scale, we drew on our field work and extensive research of those companies successfully scaling IIoT to offer manufacturers ready-to-use guidance on strategically orienting their business, organization, and technology toward IIoT success.
The resulting report, Leveraging Industrial IoT and advanced technologies for digital transformation in manufacturing, offers detailed road maps for seven enablers in three areas:
- Business
- Use-case identification and prioritization
- Plant rollout and enablement
- Organization
- Change and performance management
- Capability building and a new way of working
- Technology
- IIoT and data infrastructure—core-platform design, including IT–OT cybersecurity
- IIoT platform—the cloud imperative in manufacturing
- The tech ecosystem
We offer a brief discussion of these enabler processes here (see the report for full details).
Would you like to learn more about McKinsey Digital?
IIoT and the business: Identify, prioritize, and roll out key use cases
Both top-down and bottom-up approaches should be employed to generate a comprehensive list of use cases. Leaders should then prioritize use cases systematically, taking their potential financial impact and ease of implementation into account (Exhibit 1).
Use cases should be analyzed in terms of their replication potential across the manufacturer’s entire plant network. While some use cases will be unique one-offs, others will be replicable at least once, and some, potentially, multiple times. A scalable, overarching lighthouse use case that solves a particular problem for the first time is usually a good place to start to generate momentum. From the outset, the build team needs to focus not only on the technical implementation but also on investing time in codification, training, tutorials, and other supporting mechanisms to facilitate the quick scale-up and rollout to other plants and locations.
Manufacturers must create the road map and develop the capabilities needed to roll out the use cases across locations, without getting distracted by local solution requirements. Exhibit 2 shows an example of an auto manufacturer’s road map over three waves of use-case deployment.
IIoT and the organization: Performance, capabilities, and culture
Overcoming organizational barriers is a prerequisite to successfully managing the technological aspects of deploying IIoT in manufacturing. First, leaders should set clear target values for the entire transformation and install a team responsible for monitoring progress. This team will ensure that the implementation stays on course, quickly identifying deviations and defining mitigation measures to get the implementation back on track.
Second, priming the organization for IIoT success also means changes to organizational structures, types of collaborations, and job profiles and roles. As a result, a new way of working and a new set of capabilities are required, particularly as IT and OT converge. This framework should include the following:
- A common governance model
- Harmonized processes that once spanned IT and OT
- Centralized data and security management.
Additionally, all skills relevant to the development, deployment, and operation of IIoT use cases should be identified and developed, including training existing talent and hiring new talent (Exhibit 3).
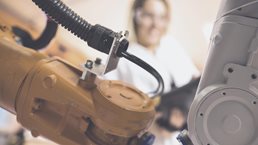
Industrial IoT generates real value—if businesses overcome six myths
IIoT and technology: Design the platform, enable the cloud, and build the ecosystem
Manufacturers will need to make decisions about technology at three levels: platform, cloud, and ecosystem.
The platform design is focused primarily on creating the future target architecture for IIoT. Central to this architecture is IT–OT integration, and manufacturers are discovering that traditional plant-focused manufacturing-execution and manufacturing-operations management systems are often not up to the task. To achieve a truly integrated technology stack, manufacturers need to assess their current brownfield setups in both OT and IT, create the future target state that enables the selected use cases, potentially select a partner to support the implementation of the platform, and manage the cybersecurity challenges inherent in an IT–OT convergence.
The cloud imperative for the IIoT transformation in manufacturing is clear: while IT cost savings are negligible, the cloud provides worthwhile benefits to the business, such as access to new artificial-intelligence (AI) and machine-learning engines; a sandbox environment for experimentation; and links to new products and services, such as sales tools, in the cloud-partner ecosystem. To achieve this, manufacturers will first need to ensure the short-term payoff by, among other actions, being smart about which applications they migrate to the cloud and in what sequence. Then they will need to implement strong governance in order to tightly manage the cloud transformation (Exhibit 4). Manufacturers should also establish an infrastructure team with the capability and mandate to build and manage standard templates, architectures, and services for use by their development teams.
Ecosystems will be essential to a manufacturer’s IIoT success, but whether the company lays the foundation for building an ecosystem or simply joins one will depend on its starting point and aspirations. Either way, the company must first understand that a solid platform on which to create and manage applications, run analytics, and store and secure data is fundamental to generating value from an IIoT ecosystem. It will also be important to create an ecosystem in which the set of partners represents sufficient diversity in terms of skills and value propositions. For most best-in-class manufacturing players, a hybrid of a highly diverse ecosystem and a monolithic ecosystem achieves the ideal balance between ease of management and efficient sourcing. Leading companies are also setting up industrial business-development teams in order to leverage the contributions of the players within the ecosystem.
A holistic approach to IIoT—one that considers the fundamentals of the organization and the business as much as technology—can help manufacturers overcome the hurdles between implementing initial scalable use cases and completing a company-wide rollout that captures full value. Our full report, Leveraging Industrial IoT and advanced technologies for digital transformation in manufacturing, provides a playbook, supported by several real-world cases, for success.