Digital transformation is at the very core of business today, yet many companies still struggle to execute on this imperative. The Covid-19 pandemic has made this imperative even more pressing: companies that don’t act with urgency to get through the crisis and recovery mode risk falling behind at a time when they can least afford to. Among the slow adopters are those companies struggling to implement the industrial internet of things (IIoT), one of a handful of new technologies that the World Economic Forum and McKinsey consider pivotal to the future of manufacturing—and a vital improvement lever to help operations emerge from the crisis. As one executive told us, “Preparation is critical, but extremely difficult. I struggle with knowing how to apply digital-transformation concepts in the real world.”
A common mistake leaders make is to focus on new technologies in isolation, without thinking about the business value the technologies can generate. But implementing IIoT systems and tools before imagining all the possibilities they can create puts the cart before the horse. It can lead companies to squander their investment of money, management attention, and—perhaps the most precious resource of all in this rapidly evolving landscape—time.
Effective digital transformations are business-backed and business-led. Digital transformation is about envisioning how technologies like IIoT can redefine value creations by accelerating and scaling existing operations, rethinking how customers are served, and even by reinventing business models. It’s a complete reimagining of the way work is done. Above all, it is about a new way of competing.
So what’s holding some companies back? From surveys and our work with manufacturers throughout the world, we’ve identified six myths about IIoT that are needlessly troubling business leaders. Here, we debunk them, drawing from our experiences in working with a wide range of companies, and from the nearly four dozen manufacturers worldwide that are leading the way in applying Fourth Industrial Revolution technologies to help advance their companies financially and operationally (see sidebar, “The myth busters: Lighthouses guiding new-technology adoption at scale”).
Myth #1: IloT is only a high-tech dashboard
People fixate on the data-collection and predictive-maintenance aspects of IIoT, which is much like viewing the airplane solely as a conveyance or the internet as a collection of electronically delivered information. Instead, IIoT—and digital transformation more broadly— represent a wholesale rethinking of value creation: a way to increase it, improve it, and accelerate it. IIoT helps companies acquire and analyze data, turn it into actionable insights to solve problems, and make decisions faster. Consider, for example, how the speed of real-time data collection and analysis has vastly accelerated insight gathering for epidemiologists and medical researchers pursuing Covid-19 treatments, testing methods, and vaccine candidates.
Many companies are already amassing data but don’t know how to use it. In conjunction with data lakes and processing platforms, IIoT generates insights automatically and alerts users, which enables a more efficient way to identify a problem and take action. Solutions and insights can then be disseminated across other teams, locations, and applications, thus multiplying their value throughout the enterprise. When properly integrated, the data collected in real time can translate into important innovations and strategy.
Deploying IIoT wisely requires a full understanding of the business and how it creates value. It also means knowing the business’s pain points, so that the company invests in IIoT where it matters most and where it can realize end-to-end value. Where and how to deploy IIoT is therefore an important strategic decision that should be guided by the business strategy set by senior management.
At Microsoft’s plant in Suzhou, China, IIoT has given the company the ability to set up new use cases with a minimal investment. Within hours of launching machine learning, the company was able to identify inventory that was on the verge of obsolescence. According to Darren Coil, director of business strategy, “The data was always there, but we weren’t seeing it until IoT highlighted it for us.” A five-person team discovered and addressed this finding, saving the company nearly $5 million in one year and cutting inventory costs by $200 million.
BMW Group’s IoT platform serves as the backbone for all digital apps, allowing plug-and-play with minimal installation costs and effort. A connected digital toolbox boosts productivity and allows employees to share best practices quickly throughout the Group. At Texas-based Texmark, sensored devices and advanced analytics software automate the petrochemical company’s plant, generating insights and reducing the risk of human error. Planned maintenance costs have been cut by 50 percent.
Would you like to learn more about our Operations Practice?
Myth #2: IIoT will displace workers
People fear that automation will eliminate jobs. But the new technologies used in digital transformation are also job generators. These new jobs, moreover, free a substantial portion of the workforce from repetitive and often unhealthy tasks and allow them to gain new capabilities. The big concern for companies adopting IIoT is rather how to reskill their workforce to take advantage of the new technologies.
Companies need people to manage the machines and run the control towers and digital twins. They need workers who are able to carry out digital performance management, interpret the data extracted from the thousands of sensors on the shop floor, and find ways to boost yields and derive actionable insights. Companies need more people in IT who can develop apps for accessing the volume of data being generated. Beyond data scientists, data engineers, and technology leaders, companies need domain experts, digital and analytics translators, and product owners—the latter, to confer with a team of business and functional-area leaders and data and tech experts to identify problems and ensure that the right digital solutions are developed (exhibit). Reskilling must happen across the value chain as well: In procurement, for example, companies will need more cost engineers who can use cost-modeling tools to assess equipment and procurement costs.
The ability to identify opportunities for improvement requires training and education. Companies can teach employees to think and act differently, to be more involved in problem solving and devising local solutions that can later be disseminated enterprise-wide through tech platforms for maximum impact. Given the breadth of new skills that are needed—not just in training for the specific technologies, but also in new ways of working—some companies are developing programs in partnership with postsecondary educational institutions.
Tata Steel Europe established its internal Advanced Analytics Academy to train employees for the new roles triggered by the new technologies. Instead of hiring pure data scientists, Tata trains its domain experts in data science. At its plant in IJmuiden, Netherlands, the company invested in building the digital skills of its site team, an approach that enabled it to realize significant productivity, cost, and quality gains.
Leaders at Petrosea, an Indonesia mining company, trained supervisors and thousands of front-line employees in new digital tools. At digital boot camps, the company educates select team members on agile methodology, big data, IT security, and analytics. Petrosea developed a mobile training app that uses gamification to make continuous learning accessible and fun. For example, it illustrates standard operating procedures primarily through visuals. The app offers the added benefit of enabling leaders to track how well employees understand the new procedures.
Myth #3: IIoT requires greenfield sites
Some business leaders believe that older facilities are an impediment to digital transformation and that legacy equipment must be replaced. Certainly, new equipment will be needed. But equating IIoT with brand-new, “greenfield” sites capable of fully automated “lights out” manufacturing is a major overstatement. Most of IIoT’s value comes from improving brownfield sites: in connecting and optimizing existing infrastructure and augmenting it with select new machinery on an ongoing basis. By adding sensors, apps, and connectivity to existing equipment, companies can collect data and convert it into business insights that are put right at employees’ fingertips. From the shop floor throughout the value chain, IIoT and the new technologies can help employees manage results.
Formula One race cars offer a useful analogy of the immediate value IIoT can deliver. These race cars have always been high-performance cars, but until the advent of sensors, drivers and crews had little understanding of what was happening in real time under the hood. Today, dozens of sensors in the engine control unit collect data from the engine, transmission, suspension, and elsewhere and feed it to the trackside support teams in mid-race. Teams now have the ability to anticipate and correct issues on the spot, to optimize performance in a competitive environment with razor-thin of margins of error.
The 4IR factory utilizes essentially two kinds of new equipment. First, an army of sensors, which are embedded throughout the shop floor to collect data on productivity, equipment utilization, machine breakdowns, maintenance, and so forth. Second is a new device that standardizes and automates a process or task. This might be a production-line device that captures data about the number of products passing by each minute, or that monitors equipment vibration levels to help predict maintenance needs.
More important than new facilities and new machines is having a robust technology ecosystem, along with IIoT architecture that has scaling potential. In a recent McKinsey survey of managers at more than 700 industrial manufacturers worldwide, more than 40 percent pointed to IT deficiencies as the main challenge in successfully implementing digital initiatives—even though digital manufacturing, by definition, is technology driven.
Lighthouse companies are proof that new technologies don’t need brand new facilities or costly makeovers. Petkim, a Turkish petrochemical company, deployed IIoT and other digital solutions in its 35-year-old facility, successfully improving yields and quality, optimizing energy use, and instituting digital maintenance. Shanghai-based Baoshan Iron & Steel adopted advanced IIoT for process optimization, artificial intelligence for visual inspection, and other advanced technologies in its 40-year-old factory.
Procter & Gamble’s Rakona plant in the Czech Republic, which produces some 4 million cases of dishwashing soaps and fabric enhancers every day, dates back to 1875. After weathering the shift to liquid products, the plant had to ramp up capacity, which required digitization and automation. To address the shortcomings of manual sampling and subsequent delays in product releases, the company eventually rolled out an in-process quality-control system in its legacy systems. Sensors now monitor product characteristics, allowing operators to obtain data that helps determine batch quality for release. It also lets them stop the line if a deviation occurs. The result: a 50 percent reduction in reworking and complaints, less scrap, fewer quality inspections, and a throughput time reduction of 24 hours.
Myth #4: To go digital requires 100% readiness
Being 100% ready is not only not necessary; it’s impractical and perhaps even counterproductive. The early lesson of the Covid-19 outbreak is that amid the widespread business shutdowns, the digitally enabled were at an advantage—in managing operations, communications, and stakeholders in a rapidly changing environment.
In many instances, companies spend too much time planning. What’s more important is getting started right away, with the help of a digital transformation office. This central team oversees pilots and guides the organization through a fail-fast, learn-fast process. Like an execution “engine,” the transformation office helps the company scale up over time through proven methodologies, best practices, and leaders’ holistic vision of the transformation.
As Gerald C. Kane, professor of information systems at Boston College’s Carroll School of Management, observes, just because the organization “[doesn’t] know what a digitally mature version of [itself] will ultimately look like, it shouldn’t stop the process from beginning. …You may only have a better idea what digital maturity is for your company once you start moving toward it.”1
Digital transformation is an ongoing journey: in our survey of Asian executives, 64 percent noted they were still in the planning stage, while only 17 percent were scaling up their efforts. Agile methods of working facilitate rapid development and refinement and continuous improvement. Agile enables companies to move in sprints and iterate quickly, so they can learn quickly from their failures to build an even better product faster.
Leaders at a European conglomerate understood the importance of starting sooner and learning along the way. They established a dedicated digital organization to advance digital transformation throughout the group’s diverse businesses, which include automation, machine tools, and specialized manufacturing systems. The office’s goal is twofold: to transform existing operations as well as fuel new digitally enabled revenue streams.
Myth# 5: Continuous improvement is costly with IIoT
Based on the experiences of many businesses, it’s often even more expensive to be disrupted and edged out of relevance.
Continuous improvement through traditional means tends to be too incremental for dealing with the magnitude of the challenges and competitive threats manufacturers face in the global digital economy. The steady stream of big data, combined with the real-time insights that IIoT fuels and more agile ways of thinking and working, embed continuous improvement into operations to create the next normal.
In contrast, any transformation that succeeds pays for itself—almost by definition. As many lighthouse companies demonstrate, the savings that result from IIoT’s efficiencies and productivity offset the cost. It’s possible to achieve high impact with a minimal replacement of equipment by optimizing existing infrastructure. As transformation evolves and escalates, the savings and bottom-line impact can grow.
Consider the experience of a global industrial-machine manufacturer that used IIoT to develop a forecasting and availability model for spare parts. The technology improved the company’s demand modeling for parts for different regions around the globe. The result: availability rose to more than 90% and inventory fell by more than 30%. Customer service satisfaction increased sharply.
But IIoT and other digital technologies do more than boost efficiency and productivity. They enable companies to make huge leaps forward, eliminating steps in the value chain and spawning new value-creating opportunities, whether new customer solutions, new production processes, or new partnerships.
As the experience of a global electronics manufacturer shows, the move to IIoT takes only a modest investment in upgrading. With dozens of production facilities and more than 25,000 employees working three shifts, the manufacturing process at this company involves a vast number of production areas, lines, and work stations. The data generated each day by different systems, and equipment, managed by locations and teams working in siloes. Getting a holistic view of operations every day was a big challenge. But replacing the production planning system would have been a massive, time-consuming, and costly undertaking.
Instead, the company installed sensors on all its production lines to capture critical real-time data, such as equipment efficiency and line productivity. An IIoT platform processes the data, serving as a remote performance dashboard and providing real-time access across all facilities. With newfound performance transparency, the manufacturer was able to bring all its facilities up to the same level of productivity—and, in the first year alone, to raise productivity more than ten percent. The IIoT system has since helped the company maintain a high rate of continuous improvement, and at the same time, become more responsive to immediate issues.
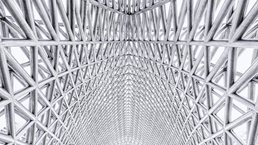
Jump-starting resilient and reimagined operations
Myth #6: IIoT is not feasible in emerging economies
Some leaders in emerging economies worry that IIoT is beyond the capabilities and infrastructure of organizations or regions, or both. In fact, companies in developing nations have had considerable success with IIoT and other 4IR technologies. It’s possible that companies in developing regions are well positioned to succeed because they are far less encumbered with brownfield facilities and legacy systems.
Although China has the greatest number of lighthouses at this writing, at 12 of 44 in total, around 20 percent of current lighthouse companies are in other emerging economies, including Brazil, the Czech Republic, India, Indonesia, Romania, and Turkey. Some of these companies operate in remote locations or in places where the physical infrastructure isn’t wholly reliable. Some are far from a metropolitan area or technology hub where services and expertise are readily available and where there’s a large pool of tech talent to draw from, yet none of these presumed shortcomings have inhibited their move to IIoT.
Tata Steel’s Kalinganagar, India—a greenfield plant—was up and running at full capacity in substantially less time than the industry standard. The company made significant investments over time, not only in digital and analytic solutions, but also in developing the capabilities of its relatively inexperienced team. Applying advanced analytics at scale has improved plant performance through gains from raw-material utilization, higher uptime, and better quality.
Petrosea, the Indonesian mining company, adopted multiple technologies at its remote project site in Tabang. Its applications included optimized truck dispatch, real-time performance monitoring, and predictive maintenance. Within six months, the operation went from loss to profit.
IIoT and other 4IR technologies are here, and the step-change improvements and value they are already delivering to many manufacturers, big and small, should dispel leaders’ lingering concerns. One reality leaders cannot ignore is the role they must play in driving digital transformation: achieving end-to-end impact from IIoT and digital technologies takes enterprise-wide commitment from the top. To ensure widespread adoption and momentum, companies must view digital transformations as a business-led transformation.
Start with a clear vision, then consider the technologies that you’ll need to advance that vision. Expect some efforts to fail; learn from them and try again. Encourage cooperation and collaboration among business units and forge a strong sense of unity. As one executive advised, “The entire company must pursue digital transformation as one with a strong sense of urgency.” Urgency, because digital transformation is a matter of competitive advantage; no company can be completely ready, and delay only results in a painful catch-up game that is often futile. Instead, be mindful that transformation is a work in progress, and that agile methods support and enhance it.
Finally, consider the capabilities that will buttress transformation, such as a scalable IIoT architecture or a technology partnership or ecosystem that will reinforce and amplify the benefits. Demonstrate to your workforce the positive effects digital will have on the company and help build sustainable employment in the future of work: a win-win-win for employees, partners, and the business.