Supply chains matter. The plumbing of global commerce has rarely been a topic of much discussion in newsrooms or boardrooms, but the past two years have pushed the subject to the top of the agenda. The COVID-19 crisis, postpandemic economic effects, and the ongoing conflict in Ukraine have exposed the vulnerabilities of today’s global supply chains. They have also made heroes of the teams that keep products flowing in a complex, uncertain, and fast-changing environment. Supply chain leaders now find themselves in an unfamiliar position: they have the attention of top management and a mandate to make real change.
Forward-thinking chief supply chain officers (CSCOs) now have a once-in-a-generation opportunity to future-proof their supply chains. And they can do that by recognizing the three new priorities alongside the function’s traditional objectives of cost/capital, quality, and service1 and redesigning their supply chains accordingly.
The first of these new priorities, resilience, addresses the challenges that have made supply chain a widespread topic of conversation. The second, agility, will equip companies with the ability to meet rapidly evolving, and increasingly volatile, customer and consumer needs. The third, sustainability, recognizes the key role that supply chains will play in the transition to a clean and socially just economy (Exhibit 1).
Boosting supply chain resilience
Supply chains have always been vulnerable to disruption. Prepandemic research by the McKinsey Global Institute found that, on average, companies experience a disruption of one to two months in duration every 3.7 years. In the consumer goods sector, for example, the financial fallout of these disruptions over a decade is likely to equal 30 percent of one year’s EBITDA.
Historical data also show that these costs are not inevitable. In 2011, Toyota suffered six months of reduced production following the devastating Tohoku earthquake and tsunami. But the carmaker revamped its production strategy, regionalized supply chains, and addressed supplier vulnerabilities. When another major earthquake hit Japan in April 2016, Toyota was able to resume production after only two weeks.
During the pandemic’s early stages, sportswear maker Nike accelerated a supply chain technology program that used radio frequency identification (RFID) technology to track products flowing through outsourced manufacturing operations. The company also used predictive-demand analytics to minimize the impact of store closures across China. By rerouting inventory from in-store to digital-sales channels and acting early to minimize excess inventory buildup across its network, the company was able to limit sales declines in the region to just 5 percent. Over the same period, major competitors suffered much more significant drops in sales.
Supply chain risk manifests at the intersection of vulnerability and exposure to unforeseen events (Exhibit 2). The first step in mitigating that risk is a clear understanding of the organization’s supply chain vulnerabilities. Which suppliers, processes, or facilities present potential single points of failure in the supply chain? Which critical inputs are at risk from shortages or price volatility?
Would you like to learn more about our Operations Practice?
In 2021, for example, many companies in North America were affected by labor shortages across their supply chain operations. Tackling those shortages has forced companies to be creative in their hiring and staffing strategy. One food distributor created regional floating labor pools of drivers, warehouse workers, and supervisors, recruiting staff in areas where they were more available and deploying them wherever they were most needed. Other companies are building their labor pipeline-management capabilities—from recruiting through retention—and sharpening their labor planning as well.
Today, most organizations lack effective systems to measure and monitor those vulnerabilities, and few have such visibility beyond their direct suppliers. In a 2021 McKinsey survey of senior supply chain executives, just under half said they understood the location of their tier-one suppliers and the key risks those suppliers face. But only 2 percent could make the same claim about suppliers in the third tier and beyond. That matters because most disruptions originate in these deeper supply chain tiers.
Closing the industry’s current knowledge gaps will require it to increase its surveillance of supply chain participants and its understanding of the physical, financial, political, and social risks they may face (Exhibit 3). The complexity and diversity of supply chain risks require smart management tools, and leading companies are applying a range of new techniques, from digital alerting systems to track potential disruptive events to risk “heat maps” that help them focus their attention on high-risk regions and suppliers.
Companies will also need a management infrastructure to steer a proactive response to these risks. Such an infrastructure would include a dedicated team, headed by a senior leader, with the remit to identify, prioritize, and respond to vulnerabilities. Those responses might include structural changes to the supply chain, as well as the development of detailed contingency plans for disruptive events. Introducing resilience metrics into supply chain KPIs helps the whole organization to ensure supply chain design and execution decisions are made in a way that balances efficiency and vulnerability. And because supply chain risk is a continually moving target, the organization should conduct regular stress tests and reviews to ensure its resilience measures remain appropriate.
Increasing supply chain agility
Customer loyalty is no longer a given. During the COVID-19 pandemic, for example, 77 percent of US consumers changed stores, brands, or the way they shop. Much of that change was driven by necessity. People went online when they couldn’t access their regular stores, and two-thirds said that lack of availability was the primary reason for switching brands. The big winners of the crisis were companies, often the largest players, that could keep products flowing to their customers in a difficult operating environment.
In the postpandemic economy, established brands will face new challenges. As consumer-generated content replaces traditional brand marketing campaigns, companies have less control over the peaks or troughs of demand. Where a business might have once spent months preparing its supply chains for a carefully targeted promotional campaign, now a single viral video can bring attention from millions of consumers overnight. One consumer goods manufacturer experienced a surge in demand in 2020 after a video of a customer enjoying its product on a skateboard ride received millions of views and spawned dozens of imitators.
New players are disrupting retail channels too, widening available choices and creating space for smaller, independent manufacturers. While consumers opted for the security of big brands during the COVID-19 pandemic, a preference for smaller producers is rising, especially among younger cohorts. And the growth of comanufacturing businesses and third-party logistics (3PLs) organizations means new entrants can compete in consumer markets with fewer expensive manufacturing and supply chain assets.
For incumbents, the lesson is clear: move at the same speed as consumers. That means creating innovative products and brands that meet the changing needs of different consumer groups as those needs emerge. And it means greater skill in managing complex portfolios of brands with different market characteristics and delivering their products through multiple channels. These same pressures increasingly hold true for B2B businesses as well, as increased consumer product complexity and demand volatility trickle down the supply chain.
This fast-moving, fragmented, consumer-centric world will require a different sort of supply chain. Traditional supply chains sought to achieve stability and minimize costs. Future supply chains will need to be much more dynamic—and be able to predict, prepare, and respond to rapidly evolving demand and a continually changing product and channel mix. In short, supply chains will need to become agile.
The good news for CSCOs is that agility and resilience are highly complementary: an agile supply chain is inherently more resilient. To be truly effective, however, this agility would need to extend into R&D, procurement, planning, manufacturing, and logistics (Exhibit 4).
At the planning stage, for example, supply chain teams will need to work in a much more proactive way. As potential market opportunities are identified, the supply chain function can begin creating scenarios that are ready for implementation alongside the development of the new product or market offering. After launch, the use of advanced techniques for demand sensing and dynamic forecasting, aided by machine learning technologies, is set to become an essential part of day-to-day supply chain operations.
In supply chain execution, agility requires new capabilities and tools. Agile operations make extensive use of digital technologies in manufacturing, for example, and maximize the use of smart automation in both production and logistics settings. Unlike the rigid supply chain automation systems of the past, technologies such as collaborative robots and smart packaging machines are capable of faster changeovers and can handle a much wider range of products and shipment types.
The drive for agility may require companies to reassess make-versus-buy decisions. In manufacturing, for example, big players typically keep the production of their stable, high-volume products in-house, using comanufacturers for niche and special projects. Leading companies appear likely to invert this trend, investing in flexible core assets and skills that allow their own manufacturing to respond quickly to rapidly changing demands—and, in some cases, outsourcing stable, high-volume products to cost-advantaged external providers. In downstream logistics, meanwhile, greater use of 3PLs may become the most cost-effective way to increase asset flexibility and proximity to customers.
Agile supply chains will also need skilled, flexible people. An agile supply chain workforce is comfortable working with and alongside advanced technologies, and personnel may need a wider range of skills so they can move between tasks as business needs change. Accordingly, agile supply chains make use of agile teams and working methods, borrowing elements of the approach that have transformed flexibility, productivity, and quality in the software industry and beyond. Agile organizational principles are well-described elsewhere, but key elements of the approach include the use of tight-knit, cross-functional teams that work together to implement new concepts and solve difficult problems in short, incremental sprints. These principles are already gaining traction across a range of industries: one major consumer products manufacturer is using “flow to work” pools in its global support functions to dynamically allocate staff to projects, for example.
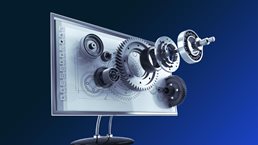
Digital twins: The art of the possible in product development and beyond
Achieving supply chain sustainability
Post-COVID-19 consumers have become even more likely to prefer brands that offer robust sustainability credentials and a strong purpose, but industry surveys conducted in mid-2020 suggested that environmental, social, and governance (ESG) topics slipped down companies’ list of priorities during the pandemic. Big players are now making up for lost time. In 2021, 29 percent of companies included ESG metrics in their staff incentive plans, for example, a seven percentage-point uptick over the previous year.
Companies looking to avoid the increasing reputational, regulatory, and financial risks of poor ESG performance are being pressed to act. And as companies such as Henkel have shown, strong environmental actions are also delivering real operational results: a digital twin connects and benchmarks 30 factories and prescribes real-time sustainability actions, which over ten years have reduced energy consumption by almost 40 percent and waste by 20 percent.
The supply chain has a central role to play in the enterprise sustainability transformation. Of nine ESG initiatives highlighted by senior executives in a 2020 industry survey, most either involve the supply chain directly, or have significant implications for supply chain setups (Exhibit 5).
The foundation for an ESG-focused transformation is a clear understanding of the organization’s baseline impact. That would include, for example, quantification of the resources consumed and emissions generated by the company’s direct activities (Scopes 1 and 2) and by participants in its wider supply chain (Scope 3). This baseline allows an organization to identify the largest opportunities for improvement, helping it set challenging but realistic goals and timescales that can be communicated to external stakeholders. Capturing those improvements requires rigorous sustainability KPIs and changes from the shop floor to the boardroom, including optimized operating practices, an ESG focus in procurement decisions, and the adoption of more sustainable technologies in existing and planned manufacturing or logistics projects.
These new priorities of resilience, agility, and sustainability can’t be tacked on to existing supply chain setups. Realistically, they will need to be built in from the foundation and considered in every element of supply chain design, organization, and operation. For many companies, that will likely require a change in mindset from the top, with risk, agility, and sustainability KPIs considered alongside traditional ones focused on cost, capital usage, service, and quality. To excel in these six supply chain dimensions, workforce management and digital capabilities will be essential.