Since the onset of the COVID-19 pandemic, we have asked supply chain leaders annually about their efforts to overcome disruptions, mitigate risks, and build resilience in their operations. Our third and most recent survey shows that companies have made significant progress on measures that have been on their agenda since the start of the crisis, and that work has helped them weather supply chain challenges such as geopolitical disruption and the worldwide shortage of semiconductors.
For example, over the past year, many companies have made structural changes to their supply networks by implementing dual or multiple sourcing strategies for critical materials and moving from global to regional networks. And as companies shift their focus from visibility to improvements in demand and supply planning, supply chain digitization efforts are also entering a new phase.
However, most respondents admit that they still have significant work to do. An acute shortage of talent is holding organizations back in their efforts to accelerate digitization and implement advanced planning systems. And despite progress over the past 12 months, many companies still lack a comprehensive picture of the risks lurking deep inside complex multitier supply networks.
Data for this year’s survey were collected from 113 supply chain leaders worldwide, representing organizations from a broad range of industries. We ran the survey over a three-week period from the end of March to the middle of April 2022.
Network resilience: Footprints on the move
The turbulence of the past two years has forced many organizations to address vulnerabilities in their complex, highly globalized supply networks. But the 2020 and 2021 supply chain pulse surveys revealed a significant gap between respondents’ ambition and their action. While many respondents said they wanted to diversify their supply base and boost in-region sourcing, the most common action in response to disruption was increases in the inventory of components and finished projects.
Bigger buffers and safety stocks are still seen as an important tool for supply chain resilience. Eighty percent of respondents told us that they increased their inventories during 2021; separate McKinsey analysis of almost 300 listed companies found that inventories increased by an average of 11 percent between 2018 and 2021,1 with the largest increases in the high-tech and commodity sectors. Some supply chain leaders have told us that they would have increased inventories even further if suppliers had been able to meet their requests.
While higher overall stock levels have become the norm, our survey suggests that companies are now looking for smarter ways to ensure resilience while keeping inventory costs under control. Seventy-one percent of respondents expect to revise their inventory policies in 2022 and beyond (Exhibit 1).
Companies are also reporting significant progress in longer-term strategies designed to increase network resilience. For example, 81 percent of respondents say that they have implemented dual-sourcing strategies during the past year, up from 55 percent in 2020. Forty-four percent of respondents, up from 25 percent the previous year (an even larger relative jump), say they are developing regionalized supply networks (Exhibit 2). Most respondents expect this momentum to continue. Sixty-nine percent of supply chain leaders told us that dual sourcing will continue to be relevant in 2022 and beyond, and 51 percent think the same about regionalization.
Overall, our survey shows that disruption has reshaped almost every supply chain. Ninety-seven percent of respondents say they have applied some combination of inventory increases, dual sourcing, and regionalization to boost resilience. Supply chain leaders believe that these efforts are paying off: Eighty-three percent told us that the footprint resilience measures they have taken over the past two years helped them minimize the impact of supply chain disruptions in 2022. For example, respondents from the commodity, consumer goods, and chemicals sectors were most likely to say that recent geopolitical disruption has not resulted in significant supply chain challenges this year; it is these industries that have focused most on structural changes such as nearshoring or network redesign. This situation may change as disruption continues, however, since data collection for our survey was conducted in the spring of 2022.
Would you like to learn more about our Manufacturing & Supply Chain Practice?
Supply chain planning: A winning formula
The volatility of the past two years has rigorously tested planning teams. Our survey reveals a formula, with three key ingredients, for resilient supply chain planning (Exhibit 3).
The first of those is visibility—companies can manage their supply chains only when they have a clear picture of each link. This is one area where organizations report significant recent progress: sixty-seven percent of respondents have implemented digital dashboards for end-to-end supply chain visibility. And those companies were twice as likely as others to avoid supply chain problems caused by the disruptions of early 2022.
The second ingredient is robust scenario planning, which can be seen in the planning counterpart to footprint redesign. Scenario planning has not been as widely adopted as visibility tools, with only 37 percent of respondents saying they had implemented the practice. These companies are also twice as likely as others to have avoided supply chain challenges this year.
An essential foundation to both supply chain visibility and effective scenario planning is comprehensive, accurate master data. Just over half the respondents tell us that the quality of the data in their supply chain planning systems were “sufficient” or “high,” suggesting that many companies still have room to improve their data collection and data management processes. High-quality data were associated with lower levels of recent supply chain disruption, although the effect was less pronounced than with visibility or scenario planning.
Digitization: Building on success
Previous surveys revealed that most companies ramped up their digital supply chain investments significantly over the past two years. Digital tools have been critical to companies’ efforts to improve the resilience of supply chain planning and execution.
That story continues in our most recent survey: in almost every sector, more than 90 percent of respondents report that they invested in digital supply chain technologies last year. Only two sectors—automotive and healthcare—report lower-than-expected investments. For the automotive sector, that finding hints at implementation delays, while healthcare companies may have slowed their pace of digitization following several years of rapid progress. Overall, just over 80 percent of respondents expect to make further investments this year and beyond.
However, the focus of these investments is changing significantly, a shift that can be attributed to the success of recent digitization projects. Last year, supply chain visibility was the top priority for companies, with 77 percent of respondents saying they were investing in this area. This year, with little more than half saying they have supply chain visibility systems in place, it has fallen to fourth place (Exhibit 4).
As companies address their visibility issues, digitization efforts are shifting to the next big challenge in supply chain management: capturing the demand signal. In this year’s survey, respondents report that the top two priorities for digital investments were demand and supply planning, cited by 74 percent and 69 percent, respectively. Fifty-eight percent of respondents are prioritizing inventory optimization.
Of the companies looking to invest in advanced planning systems, more than two-thirds say they expect to use the technology offered by their existing supply chain software provider. This is indicative of a continued market shift away from specialized point solutions for specific tasks and toward integrated end-to-end technology platforms. DIY isn’t dead in the supply chain sector, however: thirty-seven percent of respondents tell us that they expect to develop at least some supply chain software in-house, with most focusing on specific point-solutions such as visibility dashboards.
Digital talent remains a significant challenge for companies. In our 2020 survey, only 8 percent of respondents felt they had sufficient in-house talent to support their digital ambitions. By 2021, when many large digitization projects were in full swing, that number had dropped to just 1 percent. The situation has improved somewhat in the past year: in our latest survey, 10 percent of companies indicate they now have the talent they need. Respondents from the high-tech sector report the most progress in acquiring digital talent, with 20 percent more respondents than last year saying they had sufficient talent to meet their needs. Respondents from the automotive, aerospace, and defense sectors, by contrast, were much more likely than last year to report “limited” or “no” in-house digital supply chain talent.
The past two years have also seen a marked shift in companies’ approach to talent acquisition. In 2020, 70 percent of companies were building talent by reskilling their existing labor force. This year, the primary approach, used by 68 percent of companies, was outside hiring. That shift might reflect the dramatic increase in labor mobility that has occurred worldwide following the lifting of coronavirus restrictions.
Risk management: Steady progress
While companies have made radical changes in the way they use technology to manage their supply chains over the past two years, the development of their supply chain risk management capabilities has been much more incremental.
Risk remains a priority for most respondents in our latest survey, with 83 percent of respondents experiencing at least some raw-materials shortages over the past year. Ninety percent say that they want to further increase resilience, and almost three-quarters expect to increase the budget allocated to resilience-related actions. Over the past 12 months, two-thirds of companies have implemented new supply chain risk management practices; among the most popular approaches are new processes to monitor supplier-related risks.
However, understanding the status of complex, multitier supply chains is still proving extremely challenging. Forty-five percent of respondents tell us that they either have no visibility into their upstream supply chain or that they can see only as far as their first-tier suppliers.
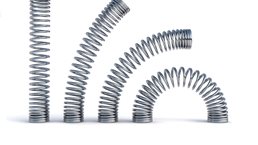
Future-proofing the supply chain
There are some signs of progress. Last year, a paltry 2 percent of respondents said they had a good picture of their supply chains down to the third tier or beyond. This year, that fraction has increased to 17 percent, with the greatest progress in sectors with shorter, simple supply chains (Exhibit 5). In the consumer products and retail sector, for example, 21 percent of respondents feel they have sufficient multitier transparency. Forty-three percent of respondents from the commodity sector believe their organizations have sufficient supply chain resilience measures in place, even though only 14 percent have a good view of third-tier suppliers. Deep supply chain transparency remains especially problematic for the automotive, aerospace, and defense sectors, with only 9 percent of respondents confident in their third-tier supplier visibility and none expressing satisfaction with their supplier visibility at all levels.
For the third year in a row, supply chains remain at the top of the corporate agenda. Our latest survey shows that companies have made significant efforts to improve supply chain resilience over the past 12 months by expanding their successful digitization programs and implementing structural changes to their networks. With volatility and disruptions likely to continue, we expect resilience to remain a key topic for the foreseeable future. For leaders, upcoming priorities include more sophisticated approaches to planning, further adaptation of supply networks, and smarter inventory management strategies.