In view of the attention it has received of late, it is easy to think artificial intelligence (AI) is a new discovery. In fact, the concept appeared in the mid-1950s. Because it was ahead of the technology then available, it languished on the shelf of “interesting ideas” for years.
Stay current on your favorite topics
Today, artificial intelligence is commonplace. Navigation systems in cars, fitness apps, Alexa and Siri, Amazon, Netflix, weather forecasting, and high-speed stock trading are among current must-have AI applications. Now, even manufacturers with heavy assets, including cement companies, are launching pilot projects to determine if and how AI might benefit their operations.
Traditionally, these manufacturers have financed improvements as capital expenditures. AI offers a less costly alternative by enabling companies to use their existing software to analyze the vast amount of data they routinely collect and, at the same time, customize their results. In doing so, they gain a better understanding of today’s evolving technologies and the value they deliver.
While AI technologies have made tangible improvements to supply chains and administrative functions, they have so far had scant presence in production—which is interesting, given that cement plants were early adopters of automation and control systems and have used digitized sensors and signals for decades.
The case for manufacturers with heavy assets to apply AI
For decades, companies have been “digitizing” their plants with distributed and supervisory control systems and, in some cases, advanced process controls. While this has greatly improved visualizations for operators, most companies with heavy assets have not kept up with the latest advances in analytics and in decision-support solutions that apply AI.
Operators still rely on their experience, intuition, and judgment. For example, today’s downsized teams of control-room operators are expected to manually monitor a multitude of signals on numerous screens and adjust settings as needed. At the same time, they must troubleshoot and run tests and trials, to name just a few of the tasks that strain the limits of their human capacity. As a result, many operators take shortcuts and prioritize urgent activities that don’t necessarily add value.
This heavy reliance on experience makes it difficult to replace a highly skilled operator at retirement. Since variations in operators’ qualifications can affect not only performance but also profits, AI’s ability to preserve, improve, and standardize knowledge is all the more important. Moreover, since it can make complex operational set-point decisions on its own, AI is able to reliably deliver predictable and consistent output in markets that have difficulty attracting and retaining operator talent.
With respect to operational improvement and dynamic adaptability, artificial intelligence can outperform conventional decision-support technologies. Also, thanks to new, high-performance software tools, processing power, and cheap memory, AI enables companies to cost-effectively create and maintain their own algorithms and intellectual property in-house, which is cheaper, more versatile, and more adaptive to constantly changing equipment and market conditions. AI can fully automate complex tasks and provide consistent and precise optimum set points in autopilot mode. It requires less manpower to maintain, and—equally important—it can be adjusted quickly when management revises manufacturing strategy and production plans.
How a cement company benefited from AI asset optimizers
In response to strong market demand, a cement company had embarked on a throughput upgrade at the beginning of 2016. Hardware upgrades had produced an 8 percent fee-rate gain, and installing an equipment vendor’s off-the-shelf advanced process-control solution brought an incremental 2 percent gain. But the client wanted to move the needle even further.
We were engaged to create and install real-time optimizers in the company’s core assets—the kiln, vertical raw mill, and finishing mills. Working as an agile mixed team of McKinsey data scientists, digital and analytics consultants, and the cement company’s process-engineering experts and plant engineers, we created AI, using free, in-house process data, a structured proprietary methodology, and the software and operating platform of a technology partner.
Would you like to learn more about McKinsey Analytics?
For this article, we illustrate our step-by-step approach to the vertical raw mill. To create and install its real-time asset optimizers, we did the following:
- Captured millions of lines of data from hundreds of process variables
- Prepared and analyzed the data using advanced analytics tools and techniques
- Mapped the data against automation process flows
- Constructed the offline optimizer using design software and applying neural networks and other advanced analytics techniques and algorithms
- Created the online optimizer version and connected the asset optimizer to the automation and control system via data interfaces
- Went online in autopilot mode after a series of tests and trials, with the asset optimizer operating autonomously without operator intervention
The installation significantly improved profits within a few weeks. Performance reviews at four and eight months after installation showed that the AI asset optimizer had consistently outperformed the existing advanced process-control system by significant percentages in both feed rate and specific energy consumption (Exhibit 1). Activating AI boosted asset performance and profit per hour for both the vertical mill and the kiln, while adhering to set-point constraints in a precise and secure manner.
Since operators could now easily switch from on-screen, visual set-point information mode to autonomous mode, they developed a preference for autopilot mode, as it enabled them to focus on complex tasks and leave the fine-tuning for optimum performance to machine intelligence. Autopilot mode also assured maximum value capture, as the system operated continuously and independently of any variations in experience, attention, or other negative influences.
The cement company’s results confirmed that algorithms and models created with advanced analytics techniques can significantly improve the yield, energy consumption, and throughput performance of heavy-asset operations and immediately enhance profit. Specifically, using existing information and software, AI can deliver improvements without capital-intensive equipment upgrades and thus produce attractive returns quickly. In addition, AI generates machine learning that is easily transferred to similar assets and sites, which adds to its appeal as an investment.
Asset-optimizer solutions have been developed and successfully deployed in chemicals, metals, mining, and other heavy-manufacturing environments, demonstrating that AI solutions are viable and economically attractive to a range of companies with heavy assets. As ongoing experience and new deployments increase, we predict AI optimizers will develop and operate even faster and become prevalent in an ever-larger number of plants—and more and more companies will seek to develop their own systems to meet their unique needs.
What manufacturers with heavy assets need for AI independence
The journey toward AI independence starts with a demonstration pilot for observation and learning purposes, followed by co-creations and, ultimately, self-creation without external help once in-house skills have been developed (Exhibit 2).
It’s important to realize that, for all their embedded artificial intelligence and machine learning algorithms, the success or failure of real-time asset optimizers springs from the people who create, use, and maintain them, from operators who steer processes, to process engineers who use deep insights to drive improvements, to managers who oversee performance, to C-level executives. A people-oriented, holistic, forward-looking approach can unleash tremendous power when individuals, digital technologies, and advanced analytics work together.
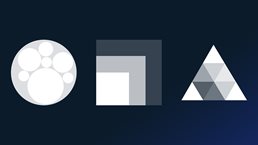
The executive’s AI playbook
Successfully creating and maintaining your own AI entails assembling the right people. Designing, building, connecting, improving, and maintaining an AI solution such as the asset optimizer requires people with solid skills and experience, a big-picture perspective, and the interpersonal skills to work collaboratively toward a common goal. Since talent of this caliber is in high demand and therefore scarce, companies might consider upskilling current employees, such as data-savvy engineers, or hiring experts from outside.
Wherever they acquire the talent, there are certain roles management must fill to succeed with AI (Exhibit 3).
Multiskilled project managers (translators) and AI creation experts with technical, change-management, and business skills are critically important. Translators and AI experts bring the knowledge and insights to integrate process engineering, data science, and business and management expertise into the AI solution. They also bring an objective perspective to transformational change and the process of incorporating business mind-sets, people, and objectives into the AI solution.
Domain experts, such as process and production engineers, understand how processes behave and how plants are set up and operated. Especially relevant to AI real-time optimization, they must be trained to work productively with professionals with a different perspective, including translators, data engineers, and data scientists, and to offer useful insights into optimization models.
Building a strong in-house team of IT and data specialists is a priority, as their education focuses on the key elements of AI: computer science, databases, data architecture, modeling, statistics, analytics, and mathematics. Within this group, you might consider data engineers, who are able to manage and navigate data-storage solutions and protocols, and data scientists, who can interpret and process data and create algorithms and models to solve complex, multivariable problems.
Handling big data efficiently requires powerful new tools for data visualization, data cleaning, data classification, and data model design. If top data-science talent is hard to attract and retain, easy-to-use data-wrangling and AI design tools can fill the void and, in doing so, upskill your in-house engineering talent.
Unlike open-source languages such as R or Python, these new AI design tools automate many time-consuming tasks, such as data extraction, data cleansing, data structuring, data visualization, and the simulation of outcomes. As a result, they do not require expert data-science knowledge and can be used by data-savvy process engineers and other tech-savvy users to create good AI models.
The opportunity cost of not investing in AI adoption
Artificial intelligence is a paradigm shift—from hard-coded, expensive, first-principles-based, inflexible solutions to adaptive self-learning solutions based on large amounts of data and machine learning algorithms. Companies that realized the potential of AI early, such as Google and Amazon, have far outperformed their peers and grown aggressively, largely due to their superior ability to predict and continuously adapt to changing conditions and to generate higher margins.
For companies with volatile margins and capital-market pressures, the stakes and the opportunity cost of not adapting are high. Manufacturers with heavy assets that are unable to read, interpret, and use their own machine-generated data to improve performance by addressing the changing needs of customers and suppliers will quickly lose out to their competitors or be acquired.
The good news is that process-industry plants are routinely capturing and storing vast amounts of machine data that they can readily mine to create algorithms. This means that although they may have fallen behind on the technological front, with guidance from external experts and interim external resources as a bridge, cement plants and manufacturers with heavy assets can quickly catch up.