Automation will drastically alter the way companies work, and this potential makes it a top priority for many business leaders. Indeed, McKinsey research shows that up to 50 percent of work performed today can already be automated with currently available technology. However, companies in the heavy industry sector (such as in energy, mining, utilities, and manufacturing) tend to struggle to set bold aspirations, develop robust business cases, and devise effective deployment approaches to take advantage of automation. Building these capabilities could help these companies capture benefits at scale, improve customer and employee experience, and build a long-term competitive advantage.
Although an array of automation initiatives in the sector are targeted at physical processes that increase the efficiency of site operations, research indicates that nonphysical core processes have higher automation potential. Nonphysical core processes, which involve the collection, processing, and analysis of data, are more easily and effectively automated compared with their physical counterparts. And once automated, these nonphysical processes can help bolster broader automation and digitization programs.1 For example, wrench-time (direct maintenance activity that adds value to a process, system, or asset) records of chemical technicians at a nuclear plant reveal that about 25 percent of their work adds value. Our analysis suggests that automating repetitive work, such as data entry or verifying system trends, can double the share of a technician’s value-added work. Doing so can help heavy industry secure significant economic benefits, increase efficiency, and improve employee experience—all at much lower levels of risk to production, safety, and health than what is involved in automating physical processes.
Streamlining core processes is becoming easier with maturing technologies, lower implementation costs, and greater awareness of and skills in lean processes, agile, and design-thinking methodologies. In such an environment, companies that don’t prioritize automation in their core enterprise strategy risk falling behind more forward-looking competitors.
Delayed impact at heavy industry companies
The heavy industry sector isn’t lacking in exploring or attempting automation, but those attempts rarely benefit the bottom line. A recent McKinsey survey found that 88 percent of respondents from the heavy industry sector have either embarked on an automation transformation or are planning to start one in the next year (Exhibit 1). Less encouraging, only 4 percent report capturing significant bottom-line improvements. Worse still, more than half of respondents believe it will take anywhere from a year to more than three years to realize bottom-line benefits—or simply don’t know. Yet more than 40 percent believe their organizations have been “successful” or “very successful” at meeting their automation targets.
This mismatch between measurable results and respondents’ perception of the success of their automation initiatives suggests that respondents use a different metric. Instead of fundamentally changing the way their organizations work, they have been measuring their ability to raise awareness about automation and deploying automation technology. But this mind-set impairs organizations’ abilities to make meaningful changes and generate value. In fact, many automation programs in heavy industry exceed their budgets while making no quantifiable operational impact. Done right, we have seen the most successful automation transformations allow companies to capture 20 to 40 percent efficiency gains and generate a positive return on investment in 12 to 18 months.
The main culprit for a bungled automation transformation is a failure to scale. Companies often find themselves stuck in pilot mode, testing a smattering of technologies such as robotic process automation (RPA) or business-process-management tools to address isolated obstacles without improving end-to-end processes. Such efforts are typically not anchored in robust, comprehensive business cases that focus on transforming core processes with clearly defined change management and workforce reskilling.
The full power of automation in heavy industry
Heavy industry’s distinctive characteristics necessitate a tailored approach to accomplish ambitious automation goals and ensure sustainable process changes.
First, operations and technology functions are already somewhat integrated in sectors such as banking and high tech; this is ideal for scaling automation transformations. By comparison, heavy industry typically has highly fragmented field workforces that operate separately from technology functions. Second, heavy industry often has more risk-averse cultures than companies in other sectors, sometimes contributing to a distrust of digital technology. Line workers often prefer a high level of human involvement over digital tools, largely because of misgivings about changing effective manual processes and automating high-risk processes that affect production or safety.
Finally, the labor-force dynamics in heavy industry can make the short-term business case for automation difficult to justify. For instance, utility companies in the United States represent the second-highest unionized workforce in the country,2 which makes reskilling roles around technology and reassigning a significant share of the workforce to higher-value activities challenging.
Despite these hurdles, industrial companies are identifying exciting use cases for automation, and some have managed to transform at scale. Examples include mining companies using analytics and machine learning for work-order planning and scheduling, utility companies using RPA to replace time-consuming regulatory reporting, and energy companies automating their budgeting process and using analytics to highlight potential performance gaps to make operational improvements. To help industrials undergo successful automation transformations, we identify five critical steps to scale up from these pilots in a way that addresses the sector’s discrete challenges.
Would you like to learn more about our Electric Power & Natural Gas Practice?
Set an aspirational target and support it with strong executive sponsorship
Setting the tone for a successful automation transformation requires the leadership team to weave an ambitious vision into the overall enterprise strategy. This vision should be defined in terms of measurable efficiency and effectiveness improvements that would add value to the organization. It should also extend beyond financial measures to include key performance indicators such as risk management, employee satisfaction, and customer experience. Because technology-enabled transformations often demand cultural changes and retraining of the workforce, executives must model these practices and values and clearly articulate the necessity and value of refocusing work (see case study, “Vision setting for a utilities company”).
Transform processes end to end instead of grafting technology enhancements
On average, a majority of work can be automated, though few individual roles can be fully automated, which means most roles will continue to require some level of human intervention. For example, 27 percent of activities in a record-to-report process in finance can be automated (Exhibit 2). The only way to capture that productivity gain is to redesign the end-to-end process, redefine roles, and reassign people to higher-value activities (see case study “An end-to-end transformation of a procure-to-pay process”).
Indeed, the key to comprehensive automation is to fundamentally recalibrate employees’ focus to encourage work that requires human problem-solving and decision making. When beginning such an undertaking, organizations must consider all associated activities (including ones across functional boundaries) and stakeholders (including external ones, such as customers and suppliers).
To fully realize efficiencies from automation, companies can combine traditional approaches (such as demand management, which involves streamlining processes and requirements) with automation tools (such as RPA and workflow tools) to promote automation and more seamless handoffs between workers. This transformation is not a technological project but a core reboot of the way work is done.
Incorporate a portfolio of automation technologies
A recent McKinsey survey found that heavy industry companies tend to rely most heavily on RPA for their automation initiatives; 44 percent of heavy industry uses this technology.3 But the most successful companies across industries have more varied portfolios of automation technologies. For example, 20 percent of companies outside the heavy industry sector are experimenting with natural language processing, compared with only 6 percent of heavy industry4 (see case study “Automating a reporting process with a collection of digital tools”).
Thanks to easy-to-deploy digital tools, it is now relatively low risk for industrials to incorporate more technologies and amplify the effects of automation. Indeed, maturing technologies have introduced a variety of automation tools for performing a range of tasks (see sidebar “Digital tools can help companies comprehensively transform processes”).
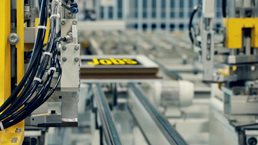
Jobs lost, jobs gained: What the future of work will mean for jobs, skills, and wages
Develop organizational capabilities to sustain automation transformations
For automation transformations to be sustainable, they cannot be isolated to the project level. As such, companies that succeed at achieving at-scale transformations invest in building in-house capabilities that can weather rapid technological changes and enable agility in day-to-day operations.
While an exhaustive inventory of capabilities to sustain automation transformations isn’t required, companies do need to develop and maintain some key skills, such as agile methodologies, design thinking, and full-stack development. Those that have been most successful at creating value through automation invest heavily in building and maintaining capabilities—both by hiring new employees with the necessary technical skills and by reskilling high-potential employees for higher-value business areas. Companies can also maintain a steady pace of internal development by providing training curriculums for roles that are crucial to the automation transformation team. Such training would ideally combine theoretical learning with practical applications. No matter the specific approach, continuous upskilling should be framed as an ongoing journey rather than a one-off exercise.
Companies can begin to develop internal capabilities in low-stakes ways. The best first step is simply to get started. A best practice is to assemble a small cross-functional team of eight to 12 members (see case study “Launching transformations with small cross-functional teams”). This team should include representatives from IT (such as developers and architects) and the business (such as process designers and subject-matter experts) and receive support and coaching to develop new-to-the-company skills (such as agile methods and design thinking). Once the organization has confirmed that the team’s work and training are valuable and replicable, it can scale the team to implement the full road map of opportunities and create similar teams in other areas of the organization.
Manage implementations as business transformations
Many industrials mistakenly manage automation as a technological transformation when the goal should be to achieve business results. Certainly, automation transformations should take place in close collaboration with IT—but organizations should take care to validate proofs of concept then quickly pivot to building solutions that yield bottom-line value.
Proofs of concept demonstrate the organization can implement the proposed technologies and create value. In parallel, organizations should create comprehensive business cases for each underlying technology to generate the investments required to launch and scale automation programs. A detailed execution plan (that includes strategies for scaling up the team) must complement the business case so the organization can manage the execution as a business process, complete with regularly reviewed performance targets and indicators (see case study “Building an investable execution plan”).
The key and the challenge for industrials attempting automation transformations will be to act quickly without waiting for perfection. Companies can extract value from automation by setting high aspirations at the outset, empowering a pilot team to pioneer small-scale transformations and scaling the transformation through end-to-end processes in partnership with IT. Managed properly, automation transformations can produce significant business impact and provide a strategic advantage.