Established OEMs and start-ups have invested $106 billion in autonomous-driving capabilities since 2010. Much of this funding has gone toward enhancing advanced driver-assistance systems (ADASs), which handle braking, object detection, and other critical vehicle functions. Many OEMs are also envisioning a day when fully self-driving cars will move from pilots and become mainstream, although development timelines are constantly changing and approval dates are uncertain.
The strong focus on autonomous vehicles (AVs) has already altered demand patterns for automotive semiconductors, with sales of specialty silicon—chips tailored to specific applications—growing strongly. These customized chips are only available from a few semiconductor companies, and some OEMs are now designing them in-house to reduce development timelines and gain more control. With demand for specialty silicon continuing to grow, other OEMs could take the same route.
To navigate the changes ahead and become market leaders, both automotive and semiconductor companies must understand the impact of new and future AV technologies on chip demand. Tier-one suppliers must also reassess their capabilities and offerings to ensure that their products remain relevant. With autonomous chips—those used to enable AV functions—expected to generate $29 billion in revenue by 2030, the stakes are high.
A changing market for automotive semiconductors
While the COVID-19 pandemic sent consumer purchases into a free fall—car sales were down 47 percent in the United States and 80 percent in Europe in April 2020—some countries are rebounding strongly across sectors. With demand rising for everything from smartphones to appliances to new cars, semiconductor orders are up, and fabs are struggling to increase their output.
After recent economic gains in some countries, the automotive sector is once again an important source of revenue for semiconductor companies. Most growth in this area stems from the shift to ADAS, since these systems must instantly process data when responding to unexpected changes, such as a sudden stop in traffic. Such capabilities require multiple interconnections within the vehicle and high-performance chips. In consequence, they have a more centralized electrical and electronic (E/E) architecture compared with traditional vehicles, as well as more sensors and compute-electronics content.
Not all AVs are alike, however, and the number and type of semiconductors required will depend largely on their level of automation. One common AV-classification system, which was defined by the Society of Automotive Engineers (SAE), divides AVs into six categories ranging from 0 (no automation) to 5 (full automation with self-driving capabilities) (Exhibit 1). Note that level 2 is divided into two parts: entry level (vehicles with some autonomous features, such as braking, but still require drivers to keep their hands on the wheel at all times) and advanced (vehicles with more extensive autonomous features that allow drivers to take their hands from the wheel at times).
Vehicles in levels 0 through 2 (entry) achieve adequate performance with standard chips, but those in levels 2 (advanced) through 5 are expected to require a growing share of specialty silicon. Such chips are more efficient, enable rapid performance increases within vehicle systems, and allow the execution of complex software functionalities and analytics, such as those that enable sensor fusion of cameras, laser, LiDAR, and other devices. But many OEMS now have difficulty obtaining the silicon that exactly matches their needs, which interferes with their ambitious AV-development programs. What’s more, there are few solutions available that fit to the targeted software stack of OEMs.
Faced with these constraints, some OEMs have already begun designing chips in-house. This route comes with several benefits, including optimized performance for specific algorithms and shorter development timelines for continuous feature improvements. In-house design also allows OEMs to define the software stack and gives them greater control over chip design so they can create customized solutions that could differentiate their AVs (for instance, by allowing earlier time to market or providing greater availability of features). Some tier-one suppliers are also claiming ownership of certain vehicle systems, such as software stacks. With such divisions, the value chain is becoming increasingly disaggregated, and the division of expertise means that companies increasingly look for partners that complement their skills and products.
Given these developments, players in the industry commonly ask several questions: What model will most OEMs favor when it comes to chip procurement? How do we need to evolve to remain strong in the changing landscape? And what is our future role in the value chain and technology stack?
Would you like to learn more about our Advanced Electronics Practice?
Navigating the changing landscape for automotive semiconductors
Analysis suggests that most OEMs will fit into one of four models when it comes to procuring semiconductors (Exhibit 2). In the first model, which is most common today, OEMs work directly with tier-one suppliers. In addition to defining chip requirements, the suppliers contract integrated device manufacturers (IDMs) to design or select the chips required. After the chips are produced by the IDM or a foundry, the supplier builds them into the system. In the second model, which is a variation of the first model, a tier-one supplier takes the lead for both defining requirements and designing the chips. Since IDM services are not required in the second model, the tier-one supplier would directly approach a foundry for production.
The third model, which is emerging as OEMs become more involved with design, involves what could be termed shallow verticalization. Under this model, OEMs define the chip requirements and directly approach IDMs and design services. They then commission production at a foundry. Some OEMs like this model because it requires limited in-house talent and shifts the burden for ensuring quality to the IDM or manufacturer. On the downside, the shallow-verticalization model increases material costs and gives OEMs little opportunity to incorporate their own specifications and create specialty chips. The lack of customization may make it difficult to differentiate their products from the pack, especially if competitors use specialty chips that deliver better computational efficiency.
A McKinsey survey of more than 100 leading automotive and semiconductor specialists showed that 68 percent of respondents believed that OEMs would favor the shallow-verticalization approach to navigating the value chain. This path makes sense for many companies, since usecase requirements are similar across OEMs and chip-development costs are higher when smaller volumes are produced.
The last model, full verticalization, is just emerging. This model gives OEMs the most independence, since they define requirements and oversee chip design before commissioning production at a foundry. There are two potential strategies for full verticalization:
- The independent route, in which OEMs develop their own silicon, architecture, and chip design—all while keeping material costs relatively low. By working independently, OEMs can create specialized chips that differentiate their products from competitors. Of course, independence comes with greater risks, since a single OEM bears all costs and has complete responsibility for meeting timelines and ensuring quality. OEMs may also encounter some delays, at least initially, since many lack employees with strong expertise in chip design and architecture.
- The formation of a cross-OEM consortium, in which multiple companies collaborate on chip design and architecture. While individual companies might be able to incorporate some of their own specifications into the chips, compromises are inevitable and there are limited opportunities for differentiation. In some cases, it may be difficult to reach an agreement about joint requirements and priorities or to align on processes. On the plus side, OEMs share both development costs and risks, reducing the burden on individual companies. Consortium members can also pool their staff, which may reduce the competition for top talent.
Opportunities still abound for semiconductor companies
The increased involvement of OEMs in chip design could cut into profits at semiconductor companies. That said, the growth of AVs could significantly increase the market for automotive chips and could help compensate for much lost business. Analysis suggests that revenues for autonomous chips—one important subcategory—are expected to rise to about $29 billion per year by 2030, representing about $350 per vehicle (Exhibit 3). That’s up from $11 billion in 2019.
Most demand is expected to come from vehicles with autonomy levels of 2 or higher. In 2019, these vehicles only accounted for about 23 percent of revenues for automotive chips. By 2030, they will account for 93 percent of demand.
Shifting chip demand
High-performance central-compute chips, such as domain control units (DCUs) and sensors, could see the fastest growth. Revenues from these products are expected to rise by about 12 percent annually from 2025 through 2030, when they will account for almost one-third of revenues. Chips for decentral electronic control units (ECUs) and sensors are only expected to see annual growth of about 6 percent from 2019 through 2030.
Looking more deeply at high-performance chips, analysis revealed that ECUs and DCUs are likely to account for a greater proportion of autonomous-chip revenues than sensors, with their share expected to increase from about 55 percent in 2019 to around 70 percent in 2030, driven primarily by the trend of increasing central calculation of autonomous-driving (AD) operations without significant preprocessing in the sensors. The most dramatic changes may occur between 2025 and 2030, when ECU and DCU values could nearly double because of faster technology adoption and reduced R&D costs. Over the same period, the value derived from sensors is likely to remain relatively flat because price decreases, such as those for LiDAR, will offset any increases in sales.
Regional variations
An examination of regional differences suggested that the Chinese market may be poised for strong growth. In 2019, China accounted for under 30 percent of global autonomous semiconductor revenues—about $3 billion. With an expected annual growth rate of about 12 percent, the Chinese semiconductor market is expected to see its share rise to nearly 40 percent by 2030. The main driver of this strong growth is high ADAS and AD adoption in China, supported by a receptive public, high demand, and a strong regulatory push. This increase, combined with overall market growth, could bring annual revenues in China to about $11 billion. Markets in the rest of the world (ROW) are expected to see more moderate revenue growth of about 8 percent annually through 2030.
The outlook for semiconductor manufacturers
Semiconductor companies will need to understand how the possible shifts could affect their market share. It is difficult to quantify the exact impact, however, since it will largely depend on the extent to which OEMs begin to design their own chips. The shift to in-house design of central DCUs could have the greatest impact, and some major OEMs have already announced their plans to do so.
With so much uncertainty ahead, it may be helpful to consider three scenarios about the shift toward in-house design at OEMs. Out of the about $6 billion market for central DCUs in 2030, OEMs would account for approximately one-third of the value, or about $2 billion, if there is a low shift in this direction. That figure would rise to about 50 percent ($3 billion) in the medium scenario and 80 percent ($5 billion) in the high scenario (Exhibit 4). Even better, those shifts can lead to large revenue increases for the semiconductor companies if they have appropriate strategies to assess the changes and react accordingly. Those figures all represent lost revenue for semiconductor IDMs or fabless companies.
A more detailed breakdown of the Chinese market showed that volume OEMs, premium OEMs, and local Chinese OEMs could all potentially gain value, although the revenue impact varies by scenario. For instance, the low scenario assumes that two volume OEMs and one premium OEM will move to in-house product in 2030. The scenario does not assume that any local Chinese OEMs will make the shift, so we did not allot them any value. The high and medium scenarios do assume that Chinese OEMs will make the shift, along with premium and volume OEMs.1
A strategic response
Semiconductor companies could benefit from new strategies. A few no-regret moves could help in all instances:
- Taking a holistic approach to chip design. Semiconductor companies could benefit from combining their software and semiconductor knowledge and talent. Consider a chip that enables vehicles to perceive people walking in the street. To build a chip with the right capabilities, it might be helpful to have software and analytics experts involved from the outset or performance may fall short.
- Onboarding talent for chip design, E/E architectures, and software. Semiconductor companies could benefit from aggressively seeking the best talent. To attract software specialists who are in great demand, they may need to adapt their company culture by adopting the agile principles common to software development. Semiconductor companies may also need to evaluate the skill sets of current employees, mainly around chip design and intellectual property (IP) block integration, and determine if any gaps exist.
- Ensuring a thorough understanding of new requirements for specialized silicon. OEMs that collaborate directly with semiconductor players on chip design could get important insights that are not available from tier-one suppliers. For semiconductor companies, this close collaboration could result in a deeper understanding of customer requirements and a better end product.
- Define separate regional strategies. E/E and software architectures, as well as the requirements for specialized silicon, may be different in certain regions, compared with the rest of the world, because of country-specific regulations, technology requirements, and customer preferences. For instance, more than 90 percent of respondents in a McKinsey survey of automotive and semiconductor executives expect that regional variations in the software stack will require different silicon in China. Most respondents—about 60 percent—also said that the best solution for serving multiple countries involved building one joint architecture that can be customized to fit market-specific requirements.
- Building strong partnerships to ensure excellence throughout the value chain. In addition to partnerships with OEMs, semiconductor companies could form strong relationships with other companies along the value chain, including specialty-software players, integrated-device manufacturers, and tier-one suppliers. Such collaboration with complementary silicon products or IP companies could further improve end products, since each player can contribute specialized knowledge and different expertise.
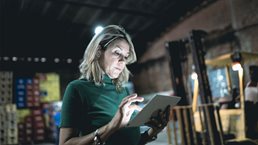
Implementing a digital transformation at industrial companies
Strategic imperatives for automotive OEMs and tier-one suppliers
While the upcoming changes to the AD chip market might hit semiconductor companies first, companies in other industries would be wise to rethink their strategic position and invest in essential capabilities to understand and navigate the changing environment.
Automotive OEMs face a multitude of challenges because of the rising complexity of the on-board software and electronics architecture required to fulfill autonomous driving, connected vehicles, electrification of the powertrain, and shared mobility (ACES) requirements. While most OEMs decided to ramp up their in-house capabilities for software development and integration, they are just beginning to create strategies for semiconductors. A few no-regret moves could assist their efforts:
- developing a strong understanding of end-to-end architecture, from software applications to semiconductors, to optimize systems
- ramping up recruitment and retention for semiconductor talent; regardless of their design decisions, they need staff that can understand and judge concepts
- ensuring that they focus their efforts if they plan to design semiconductors, which will help to avoid fragmentation of talent and allow them to double down where it really matters (for instance, concentrating on only one application area in ADAS)
- identifying strategic partners to help implement their semiconductor strategies and accelerate their efforts
Tier-one suppliers are also encountering many challenges as OEMs move down the technology stack by insourcing more parts of software development and undertaking semiconductor design. Simultaneously, semiconductor players are becoming more aggressive in linking proprietary platform software with their chips. To remain strong, tier-one suppliers could benefit from a clear semiconductor strategy, especially in the R&D-intensive areas of ADAS and AD. First, they could develop flexible offerings to avoid being locked out of the market. For instance, ADAS applications could be configured to to run on any chip. Tier-one suppliers could also consider investing in semiconductor capabilities to complement their electronics and systems-integration knowledge. Finally, tier-one suppliers could actively pursue partnerships with OEMs, semiconductor companies, and tech players within their ecosystem to avoid becoming the odd one out.
The pursuit of the best semiconductors within the automotive sector could become more severe as ADAS systems, AD, and vehicle connectivity advance. Semiconductor companies can gain insight into shifting chip demand and then develop the capabilities and products needed to remain strong. Likewise, OEMs and tier-one suppliers will benefit from taking a hard look at their capabilities and current strategies, especially in relation to semiconductors. In the new landscape, collaboration among semiconductor companies, automotive OEMs, and tier-one suppliers along the value chain may be critical for success. Those companies that monitor market trends and proactively take action may be in the best position to succeed.
This work is independent, reflects the views of the authors (McKinsey & Company and GSA), and has not been commissioned by any business, government, or other institution.