Technological advancements have enabled a fundamentally new way of delivering quality. Under this approach, companies view the quality function as a partner and coach that delivers value, not just a business cost. This perspective helps them integrate quality and compliance into regular operations while enabling speed and effectiveness.
The smart-quality approach can be applied across multiple sectors, and a recent article described how some pharmaceutical and medical technology companies have implemented this framework. The best smart-quality use cases and technologies will vary by sector. When companies in advanced industries follow the smart-quality approach, leaders must adapt it to suit more complex and deep supply chains. They should also place greater emphasis on improving discrete manufacturing, building global service networks that address quality in the field, and complying with the regulators and standardization bodies that govern advanced industries. New technologies could reshape day-to-day quality operations across the value chain of advanced-industries players (see Exhibit 1 for select examples).
Generating value through smart quality
Companies that have adopted the smart-quality approach have demonstrated that it improves quality far more than traditional measures. For example, smart quality has enabled organizations to reduce their total cost of quality by up to 50 percent. The smart-quality approach has five building blocks, all of which can generate value (Exhibit 2). As more of the building blocks get implemented, the impact compounds.
Here are representative case examples for advanced industries for the first four building blocks. The fifth building block primarily applies to pharma and medtech companies.
Smart-quality controls
An aluminum-coil producer achieved 95 percent accuracy in visual-anomaly detection after just five days of training with approximately 1,000 anomaly-free images. The algorithm delivered human-interpretable pictures of the anomaly without requiring an exhaustive training data set with all possible defects. For each image analyzed, the model calculated a confidence score, allowing employees to focus their efforts on images with potential anomalies.
Companies may also improve anomaly detection by using cobots—robots intended for direct interaction with humans—that automatically handle parts and pass them to the next operator after successful inspection. McKinsey uses such hybrid systems in its Digital Capability Centers and experienced payback periods of less than six months.
Smart-quality assurance
One automotive OEM used advanced analytics to refine its entire product-development pathway and improve the right-first-time indicator for newly developed parts to more than 80 percent. The analytics model included data from 24 different sources on all factors—both human behavior and mechanical processes—that could have caused delays. Information from three years of product-development projects and analysis of 1,500 individual car components allowed the company to train the underlying algorithms. It then implemented several improvement initiatives, including those that involved scrutinizing open issues after virtual builds, enforcing stricter rules for virtual-build-process adherence, improving bill-of-materials management, identifying suppliers with low risk scores, and providing more comprehensive onboarding for new team members.
Would you like to learn more about our Industrials & Electronics Practice?
Product and process mastery
By applying advanced analytics to field-quality information, an agriculture-equipment manufacturer reduced the time needed to identify systemic field issues by 45 percent. The analytics engine calculated daily updates of several algorithms involving approximately 450,000 warranty claims over the past five years, as well as other data, such as service tickets drawn up in dealer support. By conducting Weibull analyses, the company could extrapolate expected failure rates for nearly 7,000 critical-part numbers daily, allowing it to identify potential field-quality issues.1 The company also considered other leading indicators, such as those based on data from heavy-duty cycle machines, and expert knowledge from specific dealers to anticipate issues earlier and acknowledge critical issues immediately after their first occurrence. The accelerated issue identification translated into a warranty-cost reduction of about 5 percent. The company will achieve additional value by using insights from the algorithm to prevent issues during product development.
One steel supplier reduced its technical reject rate for a high-value product from 20 percent to nearly zero within four weeks. The company gathered and structured coil-process data, meter by meter, for more than 300 variables and 13 months of production in an end-to-end approach. It then applied several analytics methods, including decision trees, random forests, and gradient-boost models, to identify the three process parameters in the rolling mill and annealing furnaces that caused the issues. Heat maps, area charts, and correlation analyses allowed the company to visualize the insights gained and prevent issues from reoccurring.
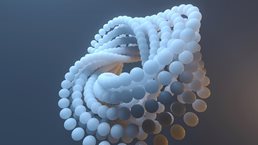
The CEO agenda for companies in advanced industries
Smart-quality ways of working
An agriculture-equipment manufacturer digitized and automated cross-functional risk and maturity management in product development to reduce new product warranty costs by more than 10 percent. The digital dashboards automatically compiled data from different sources and visualized all maturity KPIs, including the warranty costs forecast at the component and vehicle level, across functions. By using a parameterized resource model for each function, the company was able to assign required project-team capacities at the outset of each project and plan capacity requirements for the portfolio of product-development projects. The company applied industry best practices and took a systematic approach to software testing and validation to help prevent code-based quality issues.
As the case examples show, a smart-quality approach can deliver multiple benefits to companies in advanced industries. In product development, advanced analytics and digitization allow companies to improve the right-first-time rate, accelerate time to market, and increase product maturity. These changes lead to higher customer satisfaction and lower warranty costs from the start of production. In manufacturing, visual-anomaly detection enables automated quality control with significantly increased effectiveness. In addition, advanced analytics allow fast and effective resolution of production problems and prevent their recurrence. Finally, artificial intelligence accelerates identification of field-quality issues and automated detection of their root causes along the value chain. For best results, companies that embark on the path to smart quality by pursuing use cases in these areas must make a sustained commitment to change. As they implement the five building blocks, both the quality function and the organization as a whole will achieve higher levels of agility and speed.