In almost every conceivable dimension, the COVID-19 crisis is fundamentally challenging companies’ assumptions about how they do business. The scale of the pandemic’s impact and the uncertainty about its future course and consequences are forcing changes in organizational structure, decision-making processes, technology, and operations, from manufacturing to sales and marketing.
As discussed in an earlier article, many companies have already undertaken major shifts in these areas. They have reconsidered ways of working, organizational structures, and talent. The common factor in these changes has been increased operational and decision-making speed in an unprecedentedly dynamic environment. And it is already clear that this requirement is here to stay. The question facing companies in all sectors is how to move from adrenaline-based speed to speed by design—in other words, how to build increased speed into their operations on a permanent basis.
In McKinsey’s recent Global Leadership Survey on organizational speed, which included about 900 senior executives from nine industries, respondents revealed that they were already focused on the need for speed. A large majority, including leaders from advanced industries,1 expect major change in almost every facet of their organizations as a result of the COVID-19 crisis. Fundamental and lasting shifts are predicted in everything from the structure of meetings to the role of leadership, and from core processes and technology to talent, skills, and organizational culture. “Purpose” is one of the only areas where less than 20 percent of respondents anticipate meaningful change.
Respondents from companies in advanced industries, like those in other sectors, already report significant successes in boosting efficiency, effectiveness, and speed during the crisis. Another survey finding, however, should be of concern: while executives in advanced industries agree that lasting and broad-based change is coming, they are markedly less optimistic than their peers in other industries about their organizations’ ability to sustain performance improvements in a post-COVID-19 world. This article investigates the perceived obstacles ahead and suggests ways to address them.
Acceleration in the face of crisis
Speed is not, of course, an unfamiliar concept in advanced industries. In normal times, a fast-paced operating model helps companies in this sector manage the broad ecosystem of interdependencies across their supply chains in the face of disruption and the rapid innovation and digital transformation required by changing sector dynamics.
In the same spirit, advanced-industries organizations have adapted their operating models to meet the challenges presented by the coronavirus pandemic. They have increased the speed of decision making, implemented radical changes in work practices, and rapidly implemented transformational investments that have allowed many companies to maintain productivity and meet customer expectations. Consider a few success stories:
- Multiplying productivity. A major industrial factory ran at more than 90 percent capacity with only about 40 percent of the typical workforce.
- Turbocharging improvements. A US industrial player drove a lean-manufacturing program with 90 percent of its support employees working remotely. It accelerated progress on maturing frontline initiatives to achieve 30 percent greater productivity and quality.
- Developing new products. A major engineering company in aerospace and defense designed and manufactured ventilators within a week.
- Going remote. A US defense contractor shifted two-thirds of its workforce to remote work. This required significant process innovation, given its need to support sensitive customer missions.
- Shifting operations. A major shipbuilder switched from three to two shifts for thousands of employees, coordinating directly with local officials.
Survey respondents report myriad larger and smaller efficiency improvements, including big supply-chain changes, reductions in business travel time, better technology use to speed up meetings, streamlined electronic-approval processes, and a shift from in-person to online marketing.
Many respondents mentioned the benefits of greater remote and online working. One said remote working “ushered in a new paradigm where the best experts from anywhere in the world can easily offer perspectives on how to resolve complex production problems.”
Another reported that remote work, coupled with time made available by production slowdowns, enabled engineers to “meet their mechanics” and deepen their understanding of practical issues in handling parts.
“Meeting online to make decisions, which still puts people face to face, had a massive impact on our ability to quickly move forward and implement with the working teams,” wrote one executive from a firm operating on a far-off campus, where meetings previously required travel between buildings.
Would you like to learn more about our Industrials & Electronics Practice?
“Approvals for projects that yield significant benefits are being fast-tracked,” said another. The result: normal approval lead times fell by 50 percent.
A respondent at one company described moving testing and design processes online, using remotely accessed data, computer-aided design (CAD) and computer-aided management (CAM), and design-review programs. The company also used online tools to review plant operations, rather than making in-person visits.
Others reported organizational and structural changes. “During COVID-19, we chose to integrate three business units/legal entities into one,” said one respondent. “This was done completely virtually...... This integration allowed our customers to deal with one business unit regardless of brand, streamline warehousing procedures, and unite the accounting platform. The immediate result is a 15 percent increase in speed to fulfill spare-parts orders and onsite requests for assistance.”
While these results are impressive, they occurred during a time of crisis. Companies knew that they had to move quickly and decisively in response to the COVID-19 crisis, and they did not hesitate to make changes. It was something of an adrenaline-based response. As advanced-industries companies try to make organizational speed a permanent part of their culture, they may encounter more obstacles, and they need to build the muscle to sustain this bias to action.
Challenges to achieving speed by design within advanced industries
If companies can maintain the improvements prompted by the COVID-19 crisis—flatter hierarchies, faster decision making, nimble teamwork, and a new approach to learning and talent development—they could achieve significant benefits. Our research suggests that companies that successfully create a faster operating model tend to be more profitable, have stronger innovation outcomes, and experience greater growth.
With this in mind, advanced-industries companies should strive to make recent changes permanent. Our survey suggested, however, that they struggle more with implementation than their peers in other sectors. There is a notable mismatch between executives’ expectations of change and their beliefs in their companies’ ability to make that change.
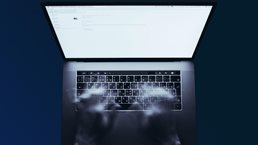
Ready, set, go: Reinventing the organization for speed in the post-COVID-19 era
At a macro level, more than 70 percent of executives in advanced industries who responded either agreed or strongly agreed that their companies would see large-scale changes in ways of working, leadership, technology and systems, and core processes (Exhibit 1). The principal drivers of this change in advanced industries were the need to reduce costs (59 percent), to increase speed of reaction to changes in the marketplace (47 percent), and to increase productivity (39 percent).
Across sectors, respondents noted that the COVID-19 crisis had already led to significant changes in operations, sales, supply chains, manufacturing, and human resources. Fully 71 percent of advanced-industries respondents reported that the pandemic had already had a significant negative impact on the stability of business outcomes—a higher proportion than in any other sector (Exhibit 2).
Yet in assessing their own companies’ performance relative to peers, these executives were less positive than those from other sectors. A higher percentage of executives in advanced industries believed their companies were underperforming other sectors on organizational resilience, profitability, speed, and digital development; similarly, a smaller percentage of executives in advanced industries thought their companies were outperforming peers in other sectors.
Questioned about perceived obstacles to operating at greater speed, executives in advanced industries cited organizational silos, slow decision making, and a lack of strategic clarity. Further, 31 percent of advanced-industries respondents reported problems with formal hierarchy—a much higher percentage compared with other sectors.
Building speed
This analysis suggests that advanced-industries organizations have considerable work ahead if they want to make speed a permanent feature of their businesses. Key activities must include rethinking ways of working, reimagining organizational structures, and reshaping talent (Exhibit 3).
Fortunately, survey results suggest that organizations are beginning to understand the type and scale of changes required. Consider a few examples:
- Rethinking ways of working. An aerospace company envisages a radically streamlined process to design, test, and install new passenger-facing features on aircraft, such as touchless boarding, self-cleaning surfaces, and redesigned security-screening procedures. Ideally, the path to adopting new features and processes will be measured in weeks or months. Another company suggests teleworking will become a cornerstone of its operations, with the aim of sharing expertise and spreading work around the globe and around the clock.
- Reimagining structures. Building on experience during the COVID-19 crisis, advanced-industries companies are significantly simplifying internal processes for project approval. One executive spoke of going from 30 handoffs to just three and reducing new-project cycle times from more than 20 weeks to five. Another was planning to institutionalize new forms of teamwork and collaboration between engineers and technical teams, with a focus on making parts easier to manufacture.
- Re-adapting talent. Advanced-industries companies are unlocking hidden reserves of talent in their efforts to navigate the challenging COVID-19 business environment. One surveyed company said it was now drawing on talented leaders one or two layers below the head of business or function and redeploying them to focus entirely on planning and generating new scenarios every week. This is excellent training for more senior roles. Another advanced-industries company, with its attention drawn by the crisis to the risks of supply-chain instability, is redirecting its recruitment effort to hiring procurement experts who can help improve supply-chain management. This major change could add 10 percent to the company’s workforce.
These are just a few examples of changes underway. But the scale of the challenges facing advanced-industries companies will require many more adjustments. Survey results suggest that companies in this sector will not succeed in building for speed unless their leaders take a hard and fundamental look at the way their organizations are constructed and managed at every level, starting at the top.
To get started, organizations can pursue a two-speed approach. They can make quick moves to lock in new changes that have generated positive outcomes, while simultaneously undertaking a broader evaluation of the structural and procedural foundations upon which the organization is built. This two-speed approach allows organizations to obtain some immediate gains while building the proper foundation for sustained speed going forward.
Momentum is here (for now). Leaders see the art in what is possible, and employees have their eyes open to sustainable ways of working. The talent market is democratizing. Moreover, we know that in advanced-industries, the market favors those who are able to innovate fast, make bold moves, and rapidly reallocate resources to lock in speed. We admire the incredible impact that advanced-industries companies have generated in such a short period of time and are optimistic about their potential to do more as they reimagine their work processes and organizational structures.