The real estate industry faces growing pressure to reduce the emissions caused by building operations. The good news is that the technology already exists to solve the problem, and a new way to formulate decarbonization plans can make it easier and more cost effective to take action, as McKinsey partner Brodie Boland discusses with McKinsey Global Publishing’s Katy McLaughlin. An edited transcript of the conversation follows.
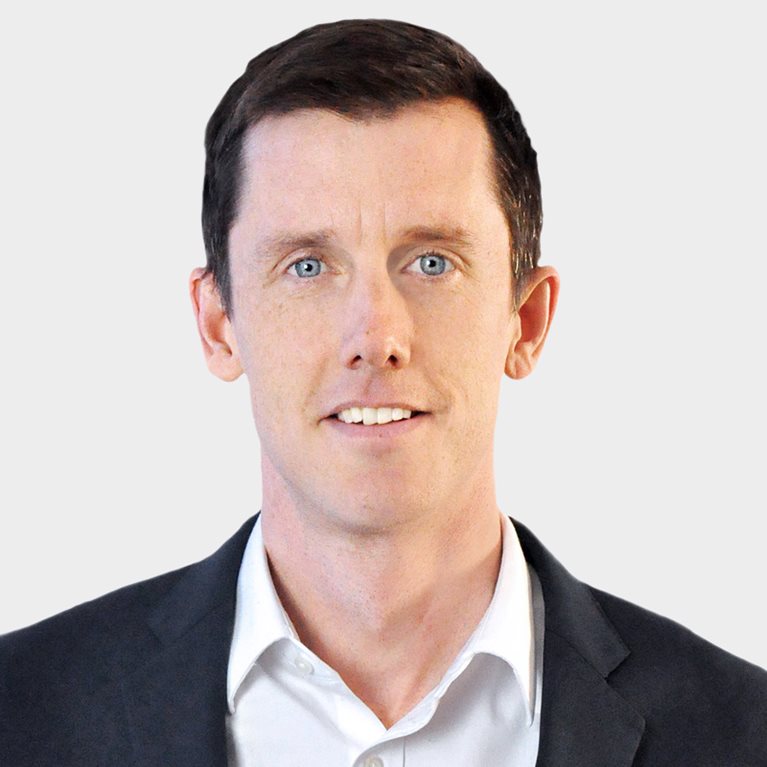
Katy McLaughlin: In early 2022, you coauthored an article about the opportunities for real estate companies that decarbonize their portfolios—and the risks for those that don’t.1 The need and the risks have only grown since then. What gives you hope that the real estate industry can meet the challenge?
Brodie Boland: The real estate industry accounts for approximately 40 percent of global combustion-related emissions, of which over 25 percentage points come from building operations. That means most of the emissions come from running buildings, as opposed to building them.
So here’s the good news: it’s often possible to get to full operational net-zero emissions in a financially neutral or positive way. The ways to do it exist at scale today. I’m not talking about newfangled technologies. I’m talking about things like heat pumps; the electrification of heating, cooling, and cooking elements; improved envelopes and better insulation; and on-site renewables. In some cases, it’s about creating automation that can do things like turn the lights off when people leave a room.
So here’s the good news: it’s often possible to get to full operational net-zero emissions in a financially neutral or positive way.
Katy McLaughlin: How could making all those upgrades be fiscally neutral or even positive?
Brodie Boland: If it’s all done according to a well-designed plan, there may be more up-front investment, but subsequent lower costs can ultimately mean that the total cost is lower. For example, if an owner can insulate a building, then they probably will need only a smaller heat pump, and they won’t need to spend as much on ducting upgrades or electrical-panel upgrades. If they have more efficient air-conditioning, then they’ll pay lower gas and electric bills.
But the crucial part of that answer is the first part: “if it’s all done according to a well-designed plan.” That has historically been the sticking point for real estate owners. It has traditionally been time consuming and expensive to create robust decarbonization plans for each building. Having someone physically go into a building, conduct an energy audit, and develop a transition plan takes time and costs money. Given owners’ constraints on capital and their obligations to investors, if transitioning a building has a significantly negative ROI, then many won’t do it.
Katy McLaughlin: What should large-portfolio owners keep in mind as they develop decarbonization plans?
Brodie Boland: For large portfolio owners, it’s important to rapidly create a plan for every single building. If they’re slowly rolling out plans across the whole portfolio and only doing ten buildings a year, they’re almost certainly doing things that don’t make sense economically over the long term.
Let’s say a company has a net-zero commitment for 2040 but hasn’t gotten around to making a plan for a particular building yet. And let’s say that in that building, the gas furnace goes out. The owner likely will end up buying a system that has a lifetime that stretches past their net-zero commitment, which means they’re either going to miss their commitment or have to tear out that system before its end of life.
It’s more cost effective to have a plan in place. If the operator knows when the gas furnace is likely to become defunct, they can be ready with the right equipment when the time comes.
Katy McLaughlin: How can owners quickly create comprehensive plans?
Brodie Boland: Fortunately, AI- and machine-learning-based solutions are now an option. These machine learning tools can use a wide range of data sources, including satellite imaging, local weather stations, and energy models of buildings, and basically do the equivalent of what before had to be done through a manual energy audit.
These machine learning tools can...do the equivalent of what before had to be done through a manual energy audit.
Using these machine-learning-based tools and the available data, building owners can very quickly get to strategies for operational and capital planning, for facility management of that building, and ultimately for achieving net-zero objectives.
Katy McLaughlin: You’ve explained how decarbonizing building operations has gotten faster and more cost effective. Has it also become more necessary?
Brodie Boland: Yes, with pressure coming from multiple angles. First, in some jurisdictions, there are regulatory pressures to improve energy efficiency and decarbonize buildings. Second, there are often also pressures from tenants who are looking for space that helps them fulfill their own net-zero commitments. And third is investor demand. Many major investors have made net-zero commitments, and so their capital goes to those with the ability to meet those commitments. These investors ask building owners, operators, and managers what their emissions are and about their plans to decarbonize.
Owners have to navigate these pressures at a time of higher interest rates and when some commercial properties are facing increasing costs and higher vacancy rates. This is why finding a financially positive path to decarbonization is so critical.
Katy McLaughlin: Accelerating a global push to decarbonize building emissions sounds like a daunting task. Give me a reason to be optimistic.
Brodie Boland: The fact that the world can get closer to net zero by decarbonizing roughly a quarter of global emissions in financially neutral or positive terms with today’s technology is enormously good news. It means no one has to wait for regulators, research labs, activists, or anything.
Create forward-looking plans so that heat pump manufacturers have the demand signals they need to dramatically scale their supply chains, so that the contractor ecosystem can dramatically scale, so that solar manufacturers are ready to manufacture and install on-site solar solutions, and so that there are technicians ready to get this done in all of these buildings.
It’s just deploy, deploy, deploy. Generate the plans, remove all the obstacles, and make it happen.