The Asia-Pacific region is at widely varying points on its journey through the COVID-19 pandemic. China is broadly beginning to restart its operations amid recovering domestic demand, while other geographies, such as Southeast Asia, Japan, and South Korea, are still tackling cases and under a range of control measures to help stop the spread.
To understand the differing sentiment and responses among manufacturing leaders across the whole region, we surveyed more than 200 manufacturing and supply-chain leaders across industries including advanced industries; consumer goods; chemicals; metals and mining; oil and gas; construction, engineering and infrastructure; and transportation and logistics.
Recovery is coming, but isn’t here yet
Overall, 39 percent of respondents are confident that the manufacturing sector will recover rapidly from disruptions caused by COVID-19, estimating that as little as two to three months will be sufficient. However, 61 percent expect that recovery will take at least six months (Exhibit 1).
Once we looked at responses split by subregions across Asia Pacific—Australia and New Zealand; China; Japan and South Korea; South Asia; and Southeast Asia—we saw that optimism closely aligns with the stage of progression through the pandemic timeline (Exhibit 2).
Nearly half of respondents in China expect rapid recovery, possibly because the country is further along the timeline in its pandemic response. Responses from Southeast Asia, Japan, and South Korea, on the other hand, report markedly lower confidence in a swift recovery. The majority of these regions are still tackling cases and only just beginning to ease lockdown measures—South Korea is currently preparing to slowly and cautiously proceed to the next normal under “everyday quarantine” measures. Japan’s lack of confidence is worth noting, as the country has a wealth of experience managing natural disasters and boasts a manufacturing sector that is well-versed in responding to and recovering from them. Nevertheless, the dynamic nature of COVID-19 appears to have challenged the Japanese manufacturing sector.
Would you like to learn more about our Operations Practice?
Despite the relative success of Australia and New Zealand in controlling the spread of COVID-19—at this writing, the two countries’ incidence rates are both less than one-tenth of rates seen in Western European and North America—almost 20 percent of respondents from Australia and New Zealand expect manufacturing operations to take longer than 12 months to recover. In Australia, this negative sentiment may be due to its manufacturing profile which is largely focused on the hardest hit primary industries.
The impact of COVID-19 is being felt across industries
Five common challenges are identified by leaders across industries: material shortages; drop in demand; worker shortages; cash-flow issues; and planning issues (Exhibits 3 and 4).
- Advanced industries are most affected by material shortages, primarily due to interconnected supply chains spanning multiple geographies. For example, a respondent from an auto company in Southeast Asia commented, “We are facing raw-material shortages from tier-2 companies, including aluminum and imported chemicals.”
- The biggest impact on consumer-facing companies is decreased demand, particularly in discretionary categories such as apparel, fashion, luxury goods, skincare, and cosmetics, where demand has dropped significantly during the pandemic.
- Labor-intensive industries are suffering the most from worker shortages, many of which are due to restrictions on workplace capacity and physical-distancing measures. This challenge is expected to resolve independently as restrictions are lifted and more employees are able to return to the workplace.
Demand volatility is causing issues for planning, with many leaders reporting that they are finding it challenging to trigger new orders because they cannot make accurate demand forecasts.
Leaders also reported cash-flow issues—both on their own part and across their multitier supplier chains. Additionally, our research reveals some examples of automotive original equipment manufacturers (OEMs) partnering with other organizations to jointly manage risks for suppliers. For example, a leading auto OEM provided a lower commercial discount rate and multichannel financing support to its suppliers.
Digital options can also help. While many of the top challenges faced by each industry seem to be influenced by their specific external situations, there is an opportunity across sectors for companies to leverage their data to create transparency and better address short- and medium-term demand and supply-chain implications. In this way, companies can minimize disruptions and optimize cost.
Resilience and reimagination—short-term actions and long-term strategy
To respond to these challenges, industry leaders are making quick short-term pivots as they take immediate actions to restart operations and ramp up production while considering resource availability and demand fluctuations. In the medium to long term, more strategic changes are being made to build resilience and enhance efficiency.
To deal with challenges concerning material shortage, leaders are increasing end-to-end transparency and implementing nerve centers to help navigate the storm, while also increasing their supplier and logistics bases to mitigate potential long-term risk (Exhibit 5). For example, a leading automotive manufacturer decided to move away from a sole-supplier partnership for one of its critical components, while another respondent reported that it is engaging with vendors much earlier to ensure supply continuity over a period of 6-12 months.
In response to reduced capacity due to worker shortages, most of the industry leaders reported that they are focusing their efforts on fulfilling demand from priority customers (Exhibit 6). For example, a leading automotive player in China resumed its production in stages, beginning with production of its fastest-selling products, while a consumer-products manufacturer in New Zealand reported changing its production mix, and an oil and gas respondent in Singapore is prioritizing work type in order of safety, compliance, and reliability.
Additionally, leaders are also considering investments to automate production lines to enhance productivity where they are dealing with a shortage of workers, while in some less-skilled environments, leaders are preferring to hire additional temporary employees and implementing rapid capability-building programs. A white-goods manufacturer in China solved its understaffing problem through cross-training its employees, deploying their administrative staff to production-related tasks.
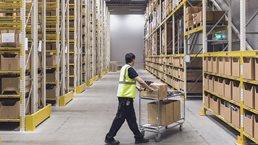
Is your supply chain risk blind—or risk resilient?
Yes to safety measures, no to shop-floor reconfiguration
As leaders plan the return phase of their operations, employee safety is their primary concern while they restart and stabilize their operations in the next normal. Across subregions, respondents report that implementing basic safety measures, such as employee temperature checks and the use of face masks, has been a top priority (Exhibit 7).
Though many respondents are prioritizing the reconfiguration of common areas such as canteens and factory entrances to allow for physical distancing, there is lower inclination towards reconfiguring shop floors. Some of this may be due to challenges such as inadequate floorspace, an inability to deploy support services because of lockdown measures, or a potential fear of falling productivity. Such reconfigurations will also likely require investment that leaders may be less inclined to make, as they may not offer long-term value once restrictions on physical distancing are lifted. However, one automotive-company executive has suggested that there may be a possibility to increase manufacturing productivity while adopting some these safety measures.
While the COVID-19 pandemic remains first and foremost a humanitarian challenge, as we move further along the timeline it is creating an opportunity for companies to reimagine their operations. Many have already begun to do so, and history tells us that those which build resilience into their operations will be well placed to move further and faster than their peers in recovery as we transition into our next normal.