More and more manufacturing organizations are undergoing digital transformations enabled by use cases powered by the Industrial Internet of Things (IIoT). However, many are having trouble scaling these pilots to achieve significant operational or financial benefits.
One reason for this “pilot trap” is because at most companies, the IT (information technology) and OT (operational-technology) stacks are siloed, resulting in poor solution definition, deployment, and adoption. Consequently, business sponsors often cannot see the value of the pilot or the results it produces. These are serious hindrances, given that IIoT use cases need the support of the business as a whole. They rely on data from a wide range of production and supply chain processes, encompassing sources across all facilities, enterprise systems, and even suppliers for input into IT applications sitting on enterprise platforms.
As digital capabilities become more strategic, and complex work-arounds become less and less feasible, more companies are getting serious about breaking down these silos and converging the IT/OT operating model. Doing so promises to accelerate in-flight use cases, democratize access to data and technology across the value chain, launch new use cases that utilize cloud-native capabilities, and improve frontline decision making by using data from both IT and OT systems.
Would you like to learn more about our Operations Practice?
Such a convergence does, to be sure, pose significant execution challenges. But an electronics company’s experience shows that for organizations that are ahead in this transition, the incremental value can add up to more than $100 million. Five elements are emerging as critical to lay the foundation.
The obstacles to convergence
Enterprise IT is typically managed by the chief information officer (CIO), whereas OT systems, shop floor IT, and plant maintenance are typically managed by the COO (and sometimes business unit managers or plant leaders). Historically, IT and OT implementations have catered to different problems and therefore evolved into significantly different architectures and protocols.
Not surprisingly, there are now significant structural and cultural obstacles to convergence. At most companies, there is no joint governance covering IT and OT, and only limited joint management and execution of cross-technology strategies and policies. This results in a high degree of duplicate and overlapping processes, compounded by a lack of interdisciplinary profiles and skills. Moreover, OT environments have tended to adopt new technologies more slowly than IT environments involving less up-front investment (such as cloud-based technologies or ones featuring continuous feature releases).
Some of the more specific challenges to convergence include:
- the need for manual translations between the enterprise and operations layers, often via spreadsheets
- data that either are not collected or are fragmented in silos within IT and OT layers
- the lack of an integrated management execution system—or multiple systems without any interconnection
- control and supervision layers without adequate interconnection, sensors, or analytics, with minimal integration into adjacent process steps
This organizational divide leads to other challenges, such as inconsistencies in technical standards, cybersecurity policies, and guidelines. As one chief information security officer at a consumer goods company recently said: “I think about IT/OT convergence a lot, but the current tools are not ready for the complexity we need in terms of size and legacy systems.”
The new industrial automation stack
While the rationale for converging IT and OT originated years ago, the emergence of IIoT is driving momentum today—particularly IIoT’s need for data from a vast number of sources. Compared with a traditional IT stack, the IIoT-based industrial automation stack adds a new layer for analytics, end-user digital applications, data management, and storage.
This new platform layer shifts the stack from a linear and hierarchical structure to one that is integrated across all layers of the architecture to gather and process real-time or near-real-time data. On the manufacturing floor, semantic data integration enhances and blends data from a wide range of frontline equipment and processes, making the data easier to analyze on the edge and use elsewhere in the organization. Revamped connectivity strengthens security for data transmission and communication across different network connections, minimizing risk. Back-end integration links operational shop floor data with systems for enterprise resource planning, product life cycle management, product design (with bill-of-material generation), and supply chain management—enabling more accurate decisions. At the top of the stack, access to a holistic data set means that analytics and applications can then work together to improve operations, such as through advanced predictive maintenance based on edge analytics.
Another major shift in this new IIoT-based industrial automation stack is the widespread use of cloud technology, which improves agility, access to innovation, remote collaboration, resilience, and productivity. In these configurations, it’s best practice for OT systems to leverage edge-based cloud options in factories to improve compatibility with central IIoT platforms that use public and private clouds.
The foundations of IT/OT convergence
To tackle convergence challenges, companies can transform the IT/OT operating model before moving into technical and architectural transformations. Five elements have shown to be especially important for converging the IT/OT operating model.
Common governance. The first step is to establish the organization, roles, and responsibilities for standardization and consistency across processes, KPIs, skills, data, and security guidelines. At the electronics company, leaders established a centralized local IT front office to govern shop floor IT and OT systems at individual plants, which are bridged to the central IT systems. This setup helped ensure that standards were applied consistently across all plants and could be scaled effectively. This setup also enabled a comprehensive view for identifying which data should be integrated to deploy IIoT use cases (exhibit).
Process harmonization. It’s best practice to harmonize central and local IT and OT processes to increase collaboration and more synchronized milestones to deliver digital use cases. Adopting industry standards, such as those from the Information Technology Infrastructure Library, can help. Clear, centralized governance, with checkpoints defined throughout the process of harmonization, helps reinforce alignment and resolve problems before they derail progress.
Common KPIs. A common set of KPIs is essential to track both IT and OT systems across main dimensions, such as productivity, timeliness, quality, and resilience—bearing in mind the different starting points of OT systems. This task helps the business understand the benefits of pilots and supports efforts to adopt and scale them. The electronics company began tracking KPIs measuring escaped defects, failed deployments, and test coverage. This increased transparency helped change the perception that IT was underperforming. Emphasizing test KPIs also promoted business owner involvement in testing and change management, which is critical for scaling IoT applications.
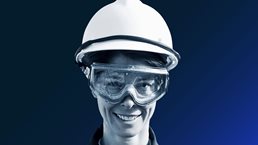
A manufacturer’s guide to scaling Industrial IoT
Skill transformation. Companies need to build new in-house digital capabilities, such as data science and cloud architecture, either through internal training or hiring external expertise. It’s also important to enforce common standards for these skills across all plants and central IT.
Central data and security management. IT and OT security standards are separate, and may remain so. However, to manage and maintain a high level of cybersecurity, the two standards must share a single operating model to ensure that controls—such as for asset management, data loss prevention, security operations, and incident response and recovery—are consistently applied to both IT and OT systems. The challenge many companies face is the pressure to “prove” that these efforts pay for themselves by avoiding data leakages or security incidents. As security attacks become more prevalent, this mindset can pose an increasingly unrealistic barrier to effective security.
Convergence in action
The experience of a global electronics manufacturer illustrates the impact of these changes. The company sought to evaluate its current IT/OT infrastructure and spending, with a view to identifying the digital use cases that would most increase its bottom line. Company leaders therefore launched a three-year digital transformation focused on creating an enhanced collaboration model between the IT/OT structure and the business units.
The company started with a ten-week assessment of the tech architecture, data, IT spend, and talent. In parallel, it sought to identify digital use cases, validate their feasibility, and prioritize them to create a road map for deployment comprising three crucial elements:
- Setting up a digital center of excellence (CoE) to design, implement, and deploy the use cases, drawing members from business, OT, and IT organizations to fulfill important roles (see sidebar, “Focusing on eight IT/OT roles helps ensure a smooth digital rollout”). Creating this team allowed for a two-speed digital organization operating in parallel that could rapidly deploy use cases on top of the traditional IT/OT functions. The electronics company’s CoE focused on introducing business product owners, together with new templates based on user stories, to help define use cases so that they met both business and technology needs. IT/OT architects then helped ensure that the use cases could be built in a scalable way, leading to clearer requirements and reduced rework.
- Linking all digital use case deliveries to business initiatives with clearly defined benefits, using a centralized program management tool to allow synchronization, transparency, and accountability. The degree of centralization will vary by company. The electronics company opted for a centralized transformation office assisted by a digital project management tool, which kept business initiatives and digital use cases on track. Early indications are that less than 10 percent of use cases will miss their deployment deadlines.
- Introducing an agile operating model, including workshops to train all members of the digital CoE to adopt proven agile practices and get comfortable with uncertainty during product development. The ability to manage and reprioritize requirements in sprints proved especially important for the electronics company, reducing time-to-market of user demo-ready prototypes (or minimum viable products) by 50 percent, from six months to three months on average.
The results were impressive: after the first six months, the transformation effort generated more than 500 business initiatives enabled by more than 30 use cases across different value streams. In total, the company estimated that these use cases will have a yearly impact of more than $200 million.
By committing to converge the IT and OT stacks, transformations need to address the five elements outlined and link these changes to business initiatives driving real financial impact to stake a claim to a more agile, digital enterprise.