The oil price roller coaster shows no sign of slowing down. In April 2020, during the first wave of the COVID-19 pandemic, the spot price for a barrel of oil on major exchanges fell below $25. Two years later it was above $100, driven higher by surging demand, geopolitical volatility, and supply chain disruptions. And the industry expects further challenges. In the immediate term, companies need to maintain output against a backdrop of rising factor costs and talent shortages. Meanwhile, the global energy transition is likely to lead to the closure of a significant number of assets across the oil and gas value chain in the coming decades, while all facilities are under pressure to improve efficiency and cut their direct carbon emissions.
To remain competitive, oil and gas companies are striving to transform their operations, improving the reliability and availability of their assets while reducing costs and carbon emissions. Leaders recognize the imperative to achieve significant shifts in all these areas, going beyond the incremental changes that characterize historical best practice.
Many CEOs rightly view digitization as key to unlocking the gains they seek. Over the past decade, advances in data analytics, artificial intelligence (AI), and the Industrial Internet of Things (IIoT) have helped players in many sectors to optimize complex processes; track down elusive sources of loss and inefficiency; and respond more effectively to volatility, shocks, and disruptions.
The high pace of innovation in these Fourth Industrial Revolution technologies is set to continue, building on earlier successes, and backed by significant investment. Oil and gas companies see opportunities for the application of a wide range of rapidly maturing technologies, including enterprise cloud computing, virtual and augmented reality, drones, and blockchain-based data exchange.
Technologies stuck in the pipeline
Frustratingly for executives, however, few oil and gas companies have deployed digital technologies at the scale required to make meaningful improvements to the performance indicators that matter most to them. McKinsey research shows that, while almost every company has been running digitization projects across various parts of its operations, 70 percent of them have not moved beyond the pilot phase.
And the technology isn’t usually the problem. Many of those pilot projects are highly successful, meeting or exceeding their technical goals. Instead, digital transformations stall due to one or more of three big cultural and organizational barriers.
First, the technologies and use cases don’t always generate clear value. That might be because they aren’t solving the fundamental problems that stand in the way of better bottom-line performance. Or it might be that project teams can’t demonstrate the bottom-line impact of their efforts. Either way, if management can’t see improvements in the issues that matter to them, they will be unwilling to commit the resources necessary for widespread deployment.
Would you like to learn more about our Operations Practice?
Second, even if managers are enthusiastic about digitization, that doesn’t mean that employees will be. New technologies require staff to develop new skills, adopt new processes, and change long-standing working practices. That doesn’t happen unless people receive the right incentives and support.
Finally, many companies view digitization as a series of discrete, siloed projects. That’s fine during the pilot phase, when integration with the organization’s other systems is less important and new and existing approaches may run in parallel. To succeed at scale, however, any new digital approach must integrate seamlessly with the organization’s wider IT and operational technology (OT) infrastructure.
Five big tech transformation ideas for the CEO
To overcome these barriers, oil and gas CEOs can take decisive action on five fronts. First, they can approach digital transformation with a relentless focus on value creation. Second, they can implement rigorous systems to track the bottom-line impact of digital initiatives. Third, they can implement a large-scale cultural transformation and change management program, fostering new skills and behaviors from the boardroom to the front line. Fourth, they can adapt their incentive systems to encourage large-scale adoption of digital-first practices. Finally, they can build an integrated and comprehensive IT/OT strategy, designed to ensure that new initiatives can be scaled to meet the needs of the business.
Putting value creation first—then tech
In successful digital transformations, value creation is always front and center. Oil and gas CEOs should be clear about the business problems they wish to address and the results they want to achieve with their digitization programs. The experience of the industry’s digital pioneers has shown that digital and analytics can make a meaningful difference right across the oil and gas value chain. Upstream companies are capturing additional value worth more than $5 per barrel of oil equivalent (BOE), using high-impact use cases in three key areas: tech-enabled exploration and drilling, end-to-end well and reservoir management, and condition-based maintenance. For downstream companies, end-to-end hydrocarbon optimization, reliability excellence, supply chain digitization, B2B commercial excellence, and digitally enabled B2C programs have helped to deliver cost savings of more than $1 per barrel, while also boosting asset availability and increasing profitability (see sidebar, “Quantifying the impact from eight value-creation themes across the oil and gas value chain”).
Digital methods are proving to be among the most powerful and cost-effective ways to reduce the industry’s carbon footprint, too. Yield, energy, and throughput (YET) optimization techniques in production and refining operations help companies to maximize their output for every unit of energy they consume. That boosts profitability while reducing carbon emissions. For a typical oil and gas player, energy efficiency measures alone have the potential to reduce scope 1 and scope 2 carbon emissions by around 20 percent, and most energy efficiency levers are net-present-value positive, even before the potential cost of carbon taxes is considered.
Tracking the impact
To ensure that they realize the potential value of their digital investments, companies need a mechanism to track the progress and bottom-line impact of every project. The foundations for any such mechanism include a clear understanding of the organization’s current performance baseline, robust KPIs, and visualization tools that enable rapid, fact-based decision making.
One Asian national oil company used a rigorous focus on value creation to steer a large-scale digital transformation across its operations. The company evaluated dozens of digital use cases and took action only on those that passed clear financial thresholds. It set up a transformation office to track the progress of its projects from pilot to large-scale implementation, comparing the bankable impact achieved against the original targets at every stage.
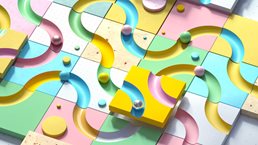
Taking the pulse of shifting supply chains
Many of the company’s most impactful digital projects involved the application of YET optimization techniques in its facilities. At one refinery and petrochemical complex, for example, it implemented an AI system to predict the best operating conditions in real time. By optimizing multiple factors including coil outlet temperature, suction pressure, and steam velocity, the system helped the facility maximize the production of higher-value products, resulting in a coke-make reduction of approximately 2 to 4 percent. That boosted overall margins by ten cents to 20 cents per barrel. Altogether, the application of advanced analytics approaches generated more than $200 million to $300 million in additional value for the company in just 18 months.
Focusing on the people
Even the most advanced technology can’t achieve anything by itself. Value emerges as a combination of the tool and the people who operate it. Advanced solutions often fail not because they produce erroneous results but because the workforce doesn’t understand, or trust, those results. That’s why successful digital transformations take a people-first approach.
Take the example of an oil and gas company in Asia. Its digital transformation focused on shifting the mindsets of people across the organization and developing new capabilities to support long-term sustainable change.
The company deployed digital specialists to train frontline teams in agile working methods and the use of new digital tools, then hosted dozens of “hackathons” across its business units to identify potential digital use cases. It hired new personnel with expertise in software development and data analytics. It also established a digital center of excellence to develop and deploy the most promising ideas that emerged from the hackathons.
To encourage employees to adopt the new tools, the company redesigned relevant processes and governance systems. And top management worked tirelessly to communicate the importance of the digital transformation and to act as highly visible role models for new ways working. In its first three years, the digital transformation generated more than $150 million in new value for the business.
Key to the success of this company’s digital transformation was its leaders’ understanding that changing the mindsets and behaviors of its people would require a multipronged approach. Decades of research into organizational change management has shown that the four elements of the influence model can determine whether new ways of working are adopted or abandoned: role modeling by management, from the CEO down; communicating a compelling change story and publicly celebrating progress; structured capability building, including the use of games, contests, and behavioral nudges to encourage participation; and formal changes to processes and KPIs. Applying each of these elements on their own improves the chances that a transformation will stick. Companies that apply all four are eight times more likely to achieve their change objectives (exhibit).
While getting the existing workforce on board is essential, large-scale digitization usually requires new talent, too. Digital projects need software developers, data scientists, and “translators” who can turn analytical insights into operational actions. The rapid and ongoing digitization in the oil and gas industry and elsewhere means that competition for people with these skills is intense. To secure and retain the talent they need, companies may have to adjust their recruitment strategies, career paths, and employee value proposition.
Providing the right incentives
Capability building, support, and leadership role modeling are powerful ways of enabling people to adopt new digital tools and ways of working, but incentives matter, too. If companies want new behaviors to stick, they need to ensure that their people are incentivized to maintain them.
Those incentives can take different forms. Companies can integrate assessment of each employee’s digital practices into annual reviews, for example, and they can link financial rewards to the bottom-line impact of digital projects. Paying market rates for in-demand digital skills matters, too.
Leading CEOs understand that nonmonetary incentives can be just as important, however. Public recognition of digital success stories is a great way to reward project participants while also helping other teams to understand the power of new approaches, for example.
Some organizations have also used gamification techniques to engage their employees and boost performance through friendly competition. One energy company, for example, built an app that reinforces the adoption of new practices by its frontline operators. The app offers daily quizzes for team members and tracks their day-to-day performance and compliance with new digital operating procedures. Live leaderboards allow team members to compare their performance in real time. And team leaders can use the app data to publicly reward high performers and to provide targeted coaching and support to team members who fall behind.
Building the right infrastructure
The technology infrastructure at most oil and gas companies is complex and fragmented. Organizations use a mix of modern and legacy IT and OT systems, and their business-critical data are distributed across those systems. Those data can be hard to access, difficult to interpret, and of inconsistent quality. Those are shaky foundations for a digital transformation, which is why successful organizations support their frontline digital initiatives with a comprehensive overhaul of their underlying infrastructure.
Another Asian national oil company, for example, set out a three-year technology road map designed to support the deployment of more than 40 digital use cases and unlock over $175 million in new value. The company upgraded its IT and OT architecture to support the systems and software it wanted to use. It also developed a new integrated data management approach that established common policies for data acquisition, storage, and quality assurance. It also upgraded cybersecurity policies and systems across the organization.
Revamping a company’s technology backbone and data architecture involves significant work by both the IT and engineering functions, but it is not a job for them alone. An effective technology infrastructure must be designed to meet the strategic objectives of the business while also supporting the tactical, day-to-day activities of all staff. Getting that right requires close collaboration between technology specialists and business stakeholders, from the CEO down, and encompasses not only IT/OT infrastructure but also data management and cybersecurity.
Digital technologies have proved their potential in the oil and gas sector. Leading players have used digitization to cut costs, boost output and improve efficiency across the end-to-end value chain. Now companies want to take the next step, embedding technology-enabled operations into every part of their business. To do that they need to upgrade the capabilities of the people and the design of their information infrastructure, while remaining laser focused on ensuring that their digital efforts generate real value.